1. Introduction
With the development of space technology, especially the successful application of the space station, space shuttles, space robot, etc., the space manipulator, as a critical technology of in-orbit support and service, has shown strong application ability and broad application prospect and has played a significant, influential role in the development of space science and application. There are considerable achievements in the research of the space manipulator [Reference Holcomb and Montemerlo1, Reference Fukushima, Inaba and Oda2, 3, Reference Stefano, Balachandran and Secchi4, Reference Oda5, Reference Oda and Fukushima6, Reference Wang, Luo and Walter7, Reference Angel, Ou, Khanh and Steve8, Reference Rybus, Seweryn and Sasiadek9, Reference King10, Reference Zhou, Luo and Wang11, Reference Xu, Liu and Xu12]. Many control methods have been proposed, such as PID control, robust control [Reference Xu, Gu, Wu and Sclabassi13, Reference Pathak, Kumar, Mukherjee and Dasgupta14, Reference Chu, Sun and Cui15], adaptive control [Reference Parlaktuna and Ozkan16, Reference Abiko and Hirzinger17, Reference Abiko and Hirzinger18], fuzzy control, neural network control, and many hybrid control methods [Reference Liu, Liang and Gao19, Reference Cheng and Chen20, Reference Guo and Li21, Reference Yu22, Reference Pisculli, Felicetti, Gasbarri, Palmerini and Sabatimi23, Reference Chu, Cui and Sun24, Reference Zhang, Fu, Qu and Wang25, Reference Kalaycioglu and Brown26].
Most of the current researches usually assume that space manipulator is a rigid system. But, in practice, the space manipulator often contains flexible components, such as the flexible joint and the flexible link. The flexible link has lightweight, less inertia, low energy consumption, sizeable working place, and high work efficiency. But, it may deform and vibrate [Reference Siciliano and Book27, Reference Benosman and Le Vey28, Reference Zarafshan, Ali, Moosavian and Papadopoulos29]. The flexible joint, caused by the harmonic drive gears, can reduce the damage caused by a collision when the manipulator grabs the target object and can compensate for the torque. But, it will cause error and vibration [Reference Spong30, Reference Ozgoli and Taghirad31, Reference Dwivedy and Eberhard32].
With the increasing requirement of lightweight, high speed, and high precision, we cannot ignore the influence of flexibility. Especially for the free-floating flexible space manipulator system, the system is nonlinear and strongly coupled. The flexible link makes the system uncertain; the flexible joints make the system’s degrees of freedom be twice the number of control inputs. So, the dynamic analysis and the motion control design become difficult. There are some researches on the flexible space manipulator, and many control methods are proposed. Komats [Reference Komats and Modi33] had dynamical analysis for a redundant flexible space manipulator with slewing and deployable links on the space platform. Wu [Reference Wu, Sun, Sun and Wu34] proposed an optimal trajectory planning method with vibration reduction for a dual-arm space robot with flexible links using Particle Swarm Optimization (PSO). Xie [Reference Xie and Chen35] offered a robust and adaptive control for the free-floating flexible space manipulator with bounded control torques. Sabatini [Reference Sabatini, Gasbarri, Monti and Palmerini36] presented an optimized adaptive vibration control via piezoelectric devices for a space manipulator with flexible links during its on-orbit operations. Huang [Reference Huang, Tang and Chen37] carried out some simulation experiments on the trajectory tracking of multi-flexible-link space robot with a dead zone. Kumar [Reference Kumar, Pathak and Sukavanam38] developed a simplified model controller that only needs the space robot’s base velocity and link parameters. Kayastha [Reference Kayastha, Katupitiya and Pearce39] adopted linear quadratic regulator (LQR) and model predictive control (MPC) algorithms to control the motion of a two-link flexible space robot system under external force. But, they are only for the space manipulator with flexible link. Yu [Reference Yu and Chen40] proposed an observer-based two-time scale robust control of free-flying flexible-joint space manipulators. Nanos [Reference Nanos and Papadopoulos41] established the flexible-joint space manipulator dynamics model. Ulrich proposed an adaptive trajectory control [Reference Ulrich, Sasiadek and Barkana42], an extended Kalman filter (EKF) strategy [Reference Ulrich and Sasiadek43], and a nonlinear adaptive output feedback control [Reference Ulrich, Sasiadek and Barkana44] for the flexible-joint space manipulator. Liang [Reference Liang, Han, Chen and Yu45] discussed a radial basis function neural network adaptive control and elastic vibration suppression for flexible-joint space robots with unknown parameters. But, they are only for the space manipulator with flexible joint. The researches on the space manipulator with both flexible link and flexible joint are few. Dong [Reference Dong, Yang, Yue, Cheng and Wei46] considered the flexibility of joint and link and discussed the dynamic modeling and analysis of space manipulator. Xie [Reference Xie and Chen47] established the free-floating flexible-joint and flexible-link space robot’s singular perturbation model and proposed a nonlinear sliding mode motion control. Zhang [Reference Zhang, Liu and Cai48] designed a trajectory tracking controller with friction compensation based on the computed torque method. Yu [Reference Yu49] offered an augmented robust control method based on a singularly perturbed model. Zhang [Reference Zhang and Chen50] designed a
${L_2}$
-gain robust control for space robot with flexible joints and flexible link, which directly avoided solving the HJI inequality.
Simultaneously, we notice that some physical parameters of the space manipulator system are uncertain or time varying due to the changes in parameters, load, fuel, etc. [Reference Feng and Palaniswami51,Reference Spong and Ortega52] So, the controller, which is usually used for the fixed base manipulator, is challenging to apply to the space manipulator’s control directly. Meanwhile, the space manipulator system will inevitably be affected by the friction between the arm joints, movement noise, fuel change, solar wind, particle ray flow, and other external interference.
To save fuel, prolong the space robot system’s service life, and reduce the launch cost, it is essential to study the free-floating space manipulator in which the base’s position and attitude are not actively controlled [Reference Dubowsky and Papadopoulos53]. In this paper, the dynamic modeling, motion control, and double vibration active suppression for the free-floating flexible-link and flexible-joint space manipulator system with external interference and uncertain parameters are studied. We consider the flexibility of the link and joints. The system’s dynamic equations are established according to linear momentum conservation, angular momentum conservation, assumed mode method [Reference Cai and Hong54], and Lagrange equation. To facilitate the design of the control, according to the singular perturbation theory [Reference Kokotovic55], the system is decomposed into three subsystems:
-
the slow subsystem
-
the flexible-joints fast subsystem
-
the flexible-link fast subsystem
Then, for the slow subsystem, a robust fuzzy sliding mode control is proposed. It can compensate for the system’s uncertain parameters and external interference by the robust controller and can reduce the chattering of sliding mode control by the saturated function and the fuzzy controller. And, the fuzzy controller is designed based on the results of the system stability analysis. For the flexible-joints fast subsystem, a velocity difference feedback controller is designed to suppress the flexible-joints vibration. For the flexible-link fast subsystem, a linear quadratic regulator (LQR) [Reference Bemporad, Morari, Dua and Pistikopoulos56] is presented to stop the flexible-link vibration. Finally, the MATLAB simulations with different desired trajectories and external interference are taken to verify the proposed controller’s effectiveness. The simulation results proved that the proposed hybrid control could control the system to track the desired trajectory accurately and suppress the vibration caused by the flexible joints and the flexible link.
The main contributions of this study are summarized as follows:
-
(1) Both flexible link and flexible joint are considered in the space manipulator system.
-
(2) The uncertain parameters and external interference are considered.
-
(3) The dynamic model of the system is established and decomposed by the singular perturbed method.
-
(4) A hybrid controller is proposed to track the desired trajectory and suppress the vibration caused by the flexible joints and the flexible link.
2. System dynamic analysis and modeling
The free-floating flexible-link and flexible-joints space manipulator system is composed of a rigid base
${{{B}}_0}$
, a rigid link
${{{B}}_1}$
, a flexible link
${{{B}}_2}$
, and two flexible joints
${{{O}}_i}({{i}} = 1,2)$
, as shown in Fig. 1.
$\boldsymbol{OXY}$
is the inertial coordinate system, and
${{{O}}_{{j}}}{{{x}}_{{j}}}{{{y}}_{{j}}}$
is the main axis coordinate of
${{{B}}_{{j}}}\left( {{{j}} = 0,1,2} \right)$
. The centroids of
${{{B}}_0}$
,
${{{B}}_1}$
, and the system are
${{{O}}_{c0}}$
,
${{{O}}_{c1}}$
, and
${{C}}$
. Their position vectors are
${{\boldsymbol{r}}_0}$
,
${{\boldsymbol{r}}_1}$
, and
${{\boldsymbol{r}}_c}$
. The arbitrary point’s position vector on the flexible link
${{{B}}_2}$
is
${r_2}$
.
${{{q}}_{{j}}}$
is the motion angle of
${{{B}}_{{j}}}$
.
${{{\theta }}_{{i}}}$
is the motor rotor’s angle.

Figure 1. Free-floating flexible-link and flexible-joints space manipulator.
According to Spong’s assumption [Reference Spong57], we regard the flexible joints
${{{O}}_{{i}}}$
as a linear spring between the motor rotor and the link and the spring’s stiffness coefficient is
$${k_{{\rm{\theta }}i}}$$
, as shown in Fig. 2. In this case, the rotor’s rotation angle
${{{\theta }}_{{i}}}$
will not always equal the link’s rotation angle
${{{q}}_{{i}}}$
. And, the flexible-joint error is:
${{{\sigma }}_{{i}}} = {{{\theta }}_{{i}}} - {{{q}}_{{i}}}$
.
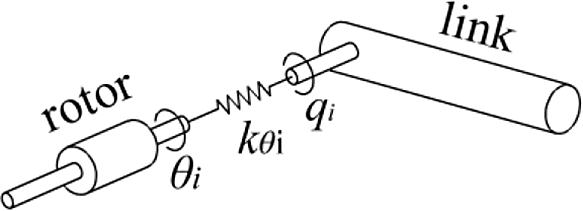
Figure 2. The simple model of flexible joint.
The flexible link
${{{B}}_2}$
is considered as an Euler–Bernoulli beam [Reference Krall58]. Neglecting the rotational inertia and shear deformation, based on the assumed mode method, the flexible link’s elastic deformation is:

where
${\varphi t _{{i}}}({{{x}}_2})$
is the
${{i}}$
th mode function,
${{{\delta }}_{{i}}}({{t}})$
is the
${{i}}$
th mode coordinate, and
${{n}}$
is the retention mode number. Considering that the lower order modes play a leading role in elastic vibration and deformation, the first two lower-order modes can meet the accuracy requirements and reduce the calculation [Reference Guo, Jin, Chang and Wang59,Reference Lv, Wei and Chen60]. So, we choose
${{n}} = 2$
, that is,
$\upsilon ({{{x}}_2},{{t}}) = {\varphi _1}({{{x}}_2}){{{\delta }}_1}({{t}}) + {\varphi _2}({{{x}}_2}){{{\delta }}_2}({{t}})$
.
According to the geometric position relationship

where
${{{l}}_0}$
is the distance between
${{{O}}_{c0}}$
and
${{{O}}_1}$
,
${{{d}}_1}$
is the distance between
${{{O}}_1}$
and
${{{O}}_{c1}}$
,
${{{l}}_1}$
is the length of
${{{B}}_1}$
.
${e_0} = {\left[ \begin{array}{c} {\sin ({{{q}}_0})} \\[4pt] {\cos ({{{q}}_0})} \end{array}\right]^{\rm T}}$
,
${e_1} = {\left[ {\begin{array}{c}{\sin ({{{q}}_0} + {{{q}}_1})}\\[4pt]{\cos ({{{q}}_0} + {{{q}}_1})}\end{array}} \right]^{\rm T}}$
,
${e_2} = {\left[ {\begin{array}{c}{\sin ({{{q}}_0} + {{{q}}_1} + {{{q}}_2})}\\[4pt]{\cos ({{{q}}_0} + {{{q}}_1} + {{{q}}_2})}\end{array}} \right]^{\rm T}}$
,
${e_3} = {\left[ \begin{array}{c} {\cos ({{{q}}_0} + {{{q}}_1} + {{{q}}_2})} \\[4pt] { - \sin ({{{q}}_0} + {{{q}}_1} + {{{q}}_2})} \end{array} \right]^{\rm T}}$
.
The system’s total center theorem of mass is:

where
${{{m}}_0}$
is the mass of
${{{B}}_0}$
,
${{{m}}_1}$
is the mass of
${{{B}}_1}$
,
${{\rho }}$
is the linear density of
${{{B}}_2}$
, and
${{{l}}_2}$
is the length of
${{{B}}_2}$
.
${{M}}$
is the total system’s mass,
${{M}} = {{{m}}_0} + {{{m}}_1} + {{\rho }}{{{l}}_2}$
. The mass of the motor is negligible.
The position vectors can be expressed as follows:

where
${{{R}}_{00}} = - ({{{m}}_1} + {{\rho }}{{{l}}_2}){{{l}}_0}/{{M}}$
,
${{{R}}_{01}} = - ({{{m}}_1}{{{d}}_1} + {{\rho }}{{{l}}_2}{{{l}}_1})/{{M}}$
,
${{{R}}_{02}} = - {{\rho l}}_2^2/(2{{M}})$
,
${{{R}}_{03}} = - {{\rho }}\int_0^{{{{l}}_2}} {{\varphi _1}({{{x}}_2})} d{{{x}}_2}/{{M}}$
,
${{{R}}_{04}} = - {{\rho }}\int_0^{{{{l}}_2}} {{\varphi _2}({{{x}}_2})} d{{{x}}_2}/{{M}}$
,
${{{R}}_{10}} = {{{R}}_{00}} + {{{l}}_0}$
,
${{{R}}_{11}} = {{{R}}_{01}} + {{{d}}_1}$
,
${{{R}}_{12}} = {{{R}}_{02}}$
,
${{{R}}_{13}} = {{{R}}_{03}}$
,
${{{R}}_{14}} = {{{R}}_{04}}$
,
${{{R}}_{20}} = {{{R}}_{00}} + {{{l}}_0}$
,
${{{R}}_{21}} = {{{R}}_{01}} + {{{l}}_1}$
,
${{{R}}_{22}} = {{{R}}_{02}} + {{{x}}_2}$
,
${{{R}}_{23}} = {{{R}}_{03}} + {\varphi _1}({{{x}}_2})$
,
${{{R}}_{24}} = {{{R}}_{04}} + {\varphi _2}({{{x}}_2})$
.
Differentiating Eq. (4), we have:

where
${\dot{{\boldsymbol{r}}}_{{i}}}$
,
${\dot{{\boldsymbol{r}}}_c}$
,
${{{\dot{\delta} }}_1}$
, and
${{{\dot{\delta} }}_2}$
are the first derivative of
${{\boldsymbol{r}}_{{i}}}$
,
${{\boldsymbol{r}}_c}$
,
${{{\delta }}_1}$
, and
${{{\delta }}_2}$
.
${\dot{{\boldsymbol{e}}}_0} = {{\dot{{q}}}_0}{\left[ {\begin{array}{c}{\cos ({{{q}}_0})}\\[4pt]{ - \sin ({{{q}}_0})}\end{array}} \right]^{\rm T}}$
,
${\dot{{\boldsymbol{e}}}_1} = ({{\dot{{q}}}_0} + {{\dot{{q}}}_1}){\left[ {\begin{array}{c}{\cos ({{{q}}_0} + {{{q}}_1})}\\[4pt]{ - \sin ({{{q}}_0} + {{{q}}_1})}\end{array}} \right]^{\rm T}}$
,
${\dot{{\boldsymbol{e}}}_2} = ({{\dot{{q}}}_0} + {{\dot{{q}}}_1} + {{\dot{{q}}}_2}){\left[ {\begin{array}{c}{\cos ({{{q}}_0} + {{{q}}_1} + {{{q}}_2})}\\[4pt]{ - \sin ({{{q}}_0} + {{{q}}_1} + {{{q}}_2})}\end{array}} \right]^{\rm T}}$
, and
${\dot{{\boldsymbol{e}}}_3} = ({{\dot{{q}}}_0} + {{\dot{{q}}}_1} + {{\dot{{q}}}_2}){\left[ {\begin{array}{c}{ - \sin ({{{q}}_0} + {{{q}}_1} + {{{q}}_2})}\\[4pt]{ - \cos ({{{q}}_0} + {{{q}}_1} + {{{q}}_2})}\end{array}} \right]^{\rm T}}$
.
Without loss of generality, the system satisfies the momentum conservation and the angular momentum conservation. Let the initial values of the momentum and the angular momentum be zero, the system’s momentum conservation equation and the angular momentum conservation equation can be expressed as:


where
${{{J}}_0}$
is the inertial moment of
${{{B}}_0}$
,
${{{J}}_1}$
is the inertial moment of
${{{B}}_1}$
, and
${{{J}}_{\rm{\theta } {{i}}}}$
is the inertial moment of the motor rotor.
${\omega _0}$
is the angular velocity of
${{{B}}_0}$
,
${{{\omega }}_0} = {{\dot{{q}}}_0}$
.
${\omega _1}$
is the angular velocity of
${{{B}}_1}$
,
${{{\omega }}_1} = ({{\dot{{q}}}_0} + {{\dot{{q}}}_1})$
.
${\omega _{\rm{\theta } {{i}}}}$
is the angular velocity of motor rotor,
${{{\omega }}_{\rm{\theta } {{i}}}} = {{{\dot{\theta} }}_{{i}}}$
.
The system’s kinetic energy
${{T}}$
contains the manipulator system’s kinetic energy
${{{T}}_r}$
and the motor rotors’ kinetic energy
${T_\rm{\theta } }$
:

where
${{{T}}_r} = {{{T}}_0} + {{{T}}_1} + {{{T}}_2}$
,
${{{T}}_\rm{\theta } } = {{{T}}_{\rm{\theta } 1}} + {{{T}}_{\rm{\theta } 2}}$
.
${{{T}}_0} = \frac{1}{2}{{{m}}_0}\dot{{\boldsymbol{r}}}_0^2 + \frac{1}{2}{{{J}}_0}{{\omega }}_0^2$
is
${{{B}}_0}$
’s kinetic energy,
${{{T}}_1} = \frac{1}{2}{{{m}}_1}\dot{{\boldsymbol{r}}}_1^2 + \frac{1}{2}{{{J}}_1}{{\omega }}_1^2$
is
${{{B}}_1}$
’s kinetic energy,
${{{T}}_2} = \frac{1}{2}{{\rho }}\int_0^{{{{l}}_2}} {\dot{{\boldsymbol{r}}}_2^2} {\rm d}{{\boldsymbol{x}}_2}$
is
${{{B}}_2}$
’s kinetic energy,
${{{T}}_{\rm{\theta } {{i}}}} = \frac{1}{2}{{{J}}_{\rm{\theta } {{i}}}}{{\omega }}_{\rm{\theta } {{i}}}^2$
is the motor rotor’s kinetic energy.
Neglecting the gravity in the space. The system’s potential energy
${{U}}$
contains the flexible link’s bending strain energy
${{{U}}_r}$
and the flexible joints’ elastic deformation potential energy
${{{U}}_\rm{\theta } }$
:

where
${{{U}}_r} = \frac{1}{2}{{EI}}{\int_0^{{{{l}}_2}} {\left( {\frac{{{\partial ^2}\upsilon ({{{x}}_2},{{t}})}}{{\partial {{x}}_2^2}}} \right)} ^2}{\rm d}{{{x}}_2}$
,
${{{U}}_\rm{\theta } } = \frac{1}{2}\sum\limits_{{{i}} = 1}^2 {{{{k}}_{\rm{\theta } {{i}}}}{{({{{\theta }}_{{i}}}{{ - }}{{{q}}_{{i}}})}^2}} $
,
${{EI}}$
is the bending stiffness of
${{{B}}_2}$
.
The system’s Lagrangian function is:
${{L}} = {{T}} - {{U}}$
. Choose
$${\boldsymbol{Q}} = {\left[ {\matrix{
{{\theta _1}\quad {\theta _2}\quad {q_0}\quad {q_1}\quad {q_2}\quad {\delta _1}\quad {\delta _2}} \cr
} } \right]^{\rm{T}}}$$
as the system’s generalized coordinate,
$${\boldsymbol{F}} = {\left[ {\matrix{
{{\tau _1}\quad {\tau _2}\quad 0\quad 0\quad 0\quad 0\quad 0} \cr
} } \right]^{\rm{T}}}$$
as the generalized force. Then, according to Lagrange’s second type equation
$\frac{\rm d}{{\rm d{{t}}}}\left( {\frac{{\partial {{L}}}}{{\partial \dot{{\boldsymbol{Q}}}}}} \right) - \frac{{\partial {{L}}}}{{\partial {{\boldsymbol{Q}}}}} = {\boldsymbol{F}}$
, the system’s dynamic equation has the following form


where
$${\boldsymbol{\theta }} = {[\matrix{
{{\theta _1}\quad {\theta _2}} \cr
} ]^{\rm{T}}}$$
,
$${{\boldsymbol{q}}_\theta } = {[\matrix{
{{q_1}\quad {q_2}} \cr
} ]^{\rm{T}}}$$
,
$${\boldsymbol{q}} = {[\matrix{
{{q_0}\quad {q_1}\quad {q_2}} \cr
} ]^{\rm{T}}}$$
,
$${\boldsymbol{\delta }} = {[\matrix{
{{\delta _1}\quad {\delta _2}} \cr
} ]^{\rm{T}}}$$
,
${{\boldsymbol{J}}_\rm{\theta } } = {\rm{diag}}({{{J}}_{\rm{\theta } 1}},{{{J}}_{\rm{\theta } 2}}) \in {{\boldsymbol{R}}^{2 \times 2}}$
is the diagonal and positive definite inertia matrix of the motor,
${{\boldsymbol{K}}_\rm{\theta } } = {\rm{diag}}({{{k}}_{\rm{\theta } 1}},{{{k}}_{\rm{\theta } 2}}) \in {{\boldsymbol{R}}^{2 \times 2}}$
is the simplified linear spring stiffness coefficient matrix of flexible joint,
${\boldsymbol{M}}({\boldsymbol{q}},\boldsymbol\delta ) \in {{\boldsymbol{R}}^{5 \times 5}}$
is the space manipulator’s symmetric positive definite inertia matrix,
${\boldsymbol{H}}({\boldsymbol{q}},\dot{{\boldsymbol{q}}},\boldsymbol\delta ,\dot{\boldsymbol\delta} )\left[ {\begin{array}{c}{\dot{{\boldsymbol{q}}}}\\[4pt]{\dot{\boldsymbol\delta} }\end{array}} \right] \in {{\boldsymbol{R}}^{5 \times 1}}$
is a column vector containing the Coriolis force and centrifugal force,
${{\boldsymbol{K}}_{
{\delta }} } = {\rm{diag}}({{{k}}_{
{\delta } 1}},{{{k}}_{
{\delta } 2}})$
is the flexible link’s stiffness coefficient matrix,
${{{k}}_{
{\delta } {{i}}}} = \int_0^{{{{l}}_2}} {{{EI}}{\varphi^{\prime\prime}_{{i}}}^{\rm T}} \varphi^{\prime\prime}_{{i}}{\rm d}{{{x}}_2}$
.
$${\boldsymbol{\tau }} = {[\matrix{
{{\tau _1}\quad {\tau _2}} \cr
} ]^{\rm{T}}} \in {{\boldsymbol{R}}^{2 \times 1}}$$
is the output torque of the motors, and
${\boldsymbol\tau _{\rm d}} \in {{\boldsymbol{R}}^{2 \times 1}}$
is the external interference torque.
It can be seen that Eq. (10a) is the dynamic equation of the motor and Eq. (10b) is the dynamic equation of the space manipulator.
3. Singular perturbation decomposition and control design
The free-floating flexible-link and flexible-joints space manipulator system is a rigid-flexible coupling system. The interaction between the rigid variables and the flexible variables will make the controller’s design difficult and affect the control quality. To reduce the interaction between variables, we use the singular perturbation method to decompose the complex system into a slow subsystem and a fast subsystem with independent time scales. The slow subsystem describes the system’s rigid movement. The fast subsystem describes the system’s flexible movement. Then, the appropriate controller is designed for each subsystem. The slow subsystem’s controller
${\boldsymbol\tau _{\rm s}}$
is designed to achieve the desired trajectory asymptotic tracking. The fast subsystem’s controller
${\boldsymbol\tau _{\rm f}}$
is designed to suppress the double vibration caused by the flexible joints and the flexible link [Reference Spong61]. So, we can write the system’s total controller as:
$\boldsymbol\tau = {\boldsymbol\tau _{\rm s}} + {\boldsymbol\tau _{\rm f}}$
.
First, we decomposed Eq. (10b) into the following form:

where
${{\boldsymbol{M}}_{11}} \in {{\boldsymbol{R}}^{1 \times 1}}$
,
${{\boldsymbol{M}}_{12}} \in {{\boldsymbol{R}}^{1 \times 2}}$
,
${{\boldsymbol{M}}_{13}} \in {{\boldsymbol{R}}^{1 \times 2}}$
,
${{\boldsymbol{M}}_{21}} \in {{\boldsymbol{R}}^{2 \times 1}}$
,
${{\boldsymbol{M}}_{22}} \in {{\boldsymbol{R}}^{2 \times 2}}$
,
${{\boldsymbol{M}}_{23}} \in {{\boldsymbol{R}}^{2 \times 2}}$
,
${{\boldsymbol{M}}_{31}} \in {{\boldsymbol{R}}^{2 \times 1}}$
,
${{\boldsymbol{M}}_{32}} \in {{\boldsymbol{R}}^{2 \times 2}}$
, and
${{\boldsymbol{M}}_{33}} \in {{\boldsymbol{R}}^{2 \times 2}}$
are the sub-matrices of
${\boldsymbol{M}}({\boldsymbol{q}},\boldsymbol\delta )$
.
${{\boldsymbol{N}}_1} \in {{\boldsymbol{R}}^{1 \times 1}}$
,
${{\boldsymbol{N}}_2} \in {{\boldsymbol{R}}^{2 \times 1}}$
,
${{\boldsymbol{N}}_3} \in {{\boldsymbol{R}}^{2 \times 1}}$
are the sub-matrices of
${\boldsymbol{H}}({\boldsymbol{q}},\dot{{\boldsymbol{q}}},\boldsymbol{\delta} ,\dot{\boldsymbol\delta} )\left[ {\begin{array}{c}{\dot{{\boldsymbol{q}}}}\\[4pt]{\dot{\boldsymbol\delta} }\end{array}} \right]$
.
From Eq. (11), we have

Substitute Eq. (12) into Eq. (11), we have

where
${{\boldsymbol{D}}_{11}} = - {{\boldsymbol{M}}_{21}}{\boldsymbol{M}}_{11}^{ - 1}{{{\boldsymbol{M}}}_{12}} + {{{\boldsymbol{M}}}_{22}}$
,
${{{\boldsymbol{D}}}_{12}} = - {{{\boldsymbol{M}}}_{21}}{{\boldsymbol{M}}}_{11}^{ - 1}{{{\boldsymbol{M}}}_{13}} + {{{\boldsymbol{M}}}_{23}}$
,
${{{\boldsymbol{D}}}_{21}} = - {{{\boldsymbol{M}}}_{31}}{{\boldsymbol{M}}}_{11}^{ - 1}{{{\boldsymbol{M}}}_{12}} + {{{\boldsymbol{M}}}_{32}}$
,
${{{\boldsymbol{D}}}_{22}} = - {{{\boldsymbol{M}}}_{31}}{{\boldsymbol{M}}}_{11}^{ - 1}{{{\boldsymbol{M}}}_{13}} + {{{\boldsymbol{M}}}_{33}}$
,
${{{\boldsymbol{C}}}_1} = - {{{\boldsymbol{M}}}_{21}}{{\boldsymbol{M}}}_{11}^{ - 1}{{{\boldsymbol{N}}}_1} + {{{\boldsymbol{N}}}_2}$
,
${{{\boldsymbol{C}}}_2} = - {{{\boldsymbol{M}}}_{31}}{{\boldsymbol{M}}}_{11}^{ - 1}{{{\boldsymbol{N}}}_1} + {{{\boldsymbol{N}}}_3}$
.
Because the matrix
$$\left[ {\matrix{
{{{\boldsymbol{D}}_{11}}} & {{{\boldsymbol{D}}_{12}}} \cr
{{{\boldsymbol{D}}_{21}}} & {{{\boldsymbol{D}}_{22}}} \cr
} } \right]$$
is symmetric and positive definite, it is reversible. Its inverse matrix can be expressed as:

Let the flexible-joint error vector
$${\boldsymbol{\sigma }} = {\boldsymbol{\theta }} - {{\boldsymbol{q}}_\theta } = {[\matrix{
{{\sigma _1}\quad {\sigma _2}} \cr
} ]^{\rm{T}}}$$
. We rewrite Eqs. (10) and (13) as following



Defining a singular perturbation factor:
${{{\varepsilon }}^2} = 1/\min \left\{ {{{{k}}_{
{\delta } 1}},{{{k}}_{
{\delta } 2}},{{{k}}_{\rm{\theta } 1}}, {{{k}}_{\rm{\theta } 2}}} \right\}$
, two variables:
${{\boldsymbol{z}}_{
{\delta }} } = \boldsymbol\delta /{{{\varepsilon }}^2}$
and
${{\boldsymbol{z}}_\rm{\theta } } = \boldsymbol\sigma /{{{\varepsilon }}^2}$
, two matrices:
${{\boldsymbol{K}}_{
{\delta } \varepsilon }} = {{{\varepsilon }}^2}{{\boldsymbol{K}}_{
{\delta }} }$
and
${{\boldsymbol{K}}_{\rm{\theta } \varepsilon }} = {{{\varepsilon }}^2}{{\boldsymbol{K}}_\rm{\theta } }$
. Then, the singular perturbation model of the system’s dynamic equation is established:



3.1. The slow subsystem
The slow subsystem only describes the system’s rigid movement. So here, we can ignore the influences of the flexible joints and the flexible link. Let
${\rm{\varepsilon }} = 0$
, then Eq. (16) can be rewritten as:



where
$\bar{{\boldsymbol{A}}}$
is the corresponding matrix or variable of
${\boldsymbol{A}}$
when
${\rm{\varepsilon }} = 0$
, that is, the corresponding matrix or variable calculated in the slowly varying time scale.
From Eq. (17a)

Substituting Eq. (18) into Eq. (17c), we can get:

Then, substituting Eqs. (18) and (19) into Eq. (17b), the slow subsystem’s dynamics equation can be obtained as:

where
${{\boldsymbol{D}}_{\rm s}} = {[{\bar{{\boldsymbol{G}}}_{11}} - {\bar{{\boldsymbol{G}}}_{12}}\bar{{\boldsymbol{G}}}_{22}^{ - 1}{\bar{{\boldsymbol{G}}}_{21}}]^{ - 1}} + {J_\rm{\theta } }$
,
${{\boldsymbol{C}}_{\rm s}} = {[{\bar{{\boldsymbol{G}}}_{11}} - {\bar{{\boldsymbol{G}}}_{12}}\bar{{\boldsymbol{G}}}_{22}^{ - 1}{\bar{{\boldsymbol{G}}}_{21}}]^{ - 1}}({\bar{{\boldsymbol{G}}}_{11}} - {\bar{{\boldsymbol{G}}}_{12}})\cdot{{\boldsymbol{C}}_1}$
.
Equation (20) can be rewritten as a quasi-linear form:

where
${{\boldsymbol{H}}_{\rm s}} \in {{\boldsymbol{R}}^{2 \times 2}}$
is not unique, but it can satisfy [Reference Slotin and Li62]

Considering the system’s uncertainty,

where
${\hat{{\boldsymbol{D}}}_{\rm s}}$
and
${\hat{{\boldsymbol{H}}}_{\rm s}}$
are the approximate matrices of
${{\boldsymbol{D}}_{\rm s}}$
and
${{\boldsymbol{H}}_{\rm s}}$
, respectively, and
$\Delta {{\boldsymbol{D}}_{\rm s}}$
and
$\Delta {{\boldsymbol{H}}_{\rm s}}$
are the system model estimation errors.
Assuming the system’s uncertain parameters are bounded,
$\Delta {{\boldsymbol{D}}_{\rm s}}$
and
$\Delta {{\boldsymbol{H}}_{\rm s}}$
are also bounded. There are positive constants
${{\rm{l}}_{\rm d}}$
and
${l_{\rm h}}$
,

And, assuming
${\boldsymbol\tau _{\rm d}}$
is bounded. So, there is a positive constant
${{{l}}_{\rm t}}$
that satisfies:

Defined
$${{\boldsymbol{q}}_{\rm{d}}} = {[\matrix{
{{q_{1{\rm{d}}}}\quad {q_{2{\rm{d}}}}} \cr
} ]^{\rm{T}}}$$
be the expected output vector of the slow subsystem, then the output error vector
${\boldsymbol{e}}$
between
${{\boldsymbol{q}}_{\rm d}}$
and the actual output vector
$${{\boldsymbol{q}}_\theta } = {[\matrix{
{{q_1}\quad {q_2}} \cr
} ]^{\rm{T}}}$$
is:
$${\boldsymbol{e}} = {{\boldsymbol{q}}_\theta } - {{\boldsymbol{q}}_{\rm{d}}} = {[\matrix{
{{e_1}\quad {e_2}} \cr
} ]^{\rm{T}}}$$
.
Selecting the following sliding surface

where
$\lambda $
is a positive constant diagonal matrix.
Derivating
${\boldsymbol{s}}$

Substitute Eq. (16a) into Eq. (12),

The slow subsystem’s controller is designed as follows:

(1)
${{\boldsymbol{u}}_1}$
is an equivalent controller,

(2)
${{\boldsymbol{u}}_2}$
is a robust controller. It is used to compensate for the system’s uncertain parameter and external disturbance.

where
${{\boldsymbol{K}}_{\rm s}} = {{{l}}_{\rm d}}\left\| {{{\lambda }}\dot{{\boldsymbol{e}}} - {{\ddot{{\boldsymbol{q}}}}_{\rm{\theta } {\rm d}}}} \right\| + {{{l}}_{\rm h}}\left\| {{{\dot{{\boldsymbol{q}}}}_\rm{\theta } }} \right\| \cdot \left\| {{\boldsymbol{s}} - {{\dot{{\boldsymbol{q}}}}_\rm{\theta } }} \right\| + {{{l}}_{\rm t}}$
.
$${\textbf{sat}}({{\boldsymbol{s}} \over {\boldsymbol{\Phi }}}) = {\left[ {\matrix{
{{\rm{sat}}({{{s_1}} \over {{\Phi _1}}})\quad {\rm{sat}}({{{s_2}} \over {{\Phi _2}}})} \cr
} } \right]^{\rm{T}}}$$
, it is a saturated function vector. It is used to reduce the chattering of sliding mode control itself, its elements are:

where
$$\Phi = {\left[ {\matrix{
{{{\boldsymbol{\Phi }}_1}\quad {\Phi _2}} \cr
} } \right]^{\rm{T}}}$$
,
${{\rm{\Phi }}_1}$
and
${{\rm{\Phi }}_2}$
are positive parameters,
${{{s}}_{{i}}}$
is the
${{i}}$
th element of
${\boldsymbol{s}}$
, and
${{\rm{\Phi }}_{{i}}}$
is the
${{i}}$
th element of
$\boldsymbol\Phi $
.
(3)
${{\boldsymbol{u}}_3}$
is a fuzzy controller. It is used to reduce the vibration of sliding mode control, improve the approach speed, and ensure the system’s stability.
${{\boldsymbol{u}}_3}$
is designed based on the results of the system stability analysis, as follows:
Defined a Lyapunov function:

Differentiating
${\boldsymbol{V}}$
, and combining Eqs. (22) and (28), then

Substitute Eqs. (23), (29), (30), and (31) into Eq. (34), we have

The system’s stability analysis has two cases:
Case 1: when
$\left| {{{{s}}_{{i}}}} \right| \gt {{{\Phi }}_{{i}}}$
,
$sat(\frac{{{{{s}}_{{i}}}}}{{{{\rm{\Phi }}_{{i}}}}}) = {{\rm{sgn}}} ({{{s}}_{{i}}})$
. Substitute (24) and (25) into Eq. (35), we have:

So when
${{\boldsymbol{s}}^{\rm T}}{{\boldsymbol{u}}_3} \lt 0$
,
$\dot{{\boldsymbol{V}}} \lt 0$
. Thus, the asymptotic stability of
${\boldsymbol{s}},{\boldsymbol{e}},\dot{{\boldsymbol{e}}}$
outside the boundary layer can be guaranteed.
Case 2: when
$\left| {{{{s}}_{{i}}}} \right| \le {{{\Phi }}_{{i}}}$
,
${\rm{sat}}(\frac{{{{{s}}_{{i}}}}}{{{{{\Phi }}_{{i}}}}}) = \begin{array}{c}{\frac{{{{{s}}_{{i}}}}}{{{{\rm{\Phi }}_{\rm{i}}}}}}\end{array}$
. Substitute (24) and (25) into Eq. (35), we have:

So when
${{\boldsymbol{s}}^{\rm T}}{{\boldsymbol{u}}_3} \le - {{\boldsymbol{K}}_{\rm s}}(\left\| {\boldsymbol{s}} \right\| - \frac{{{{\left\| {\boldsymbol{s}} \right\|}^2}}}{{\left\| \boldsymbol\Phi \right\|}})$
,
$\dot{{\boldsymbol{V}}} \le 0$
, and
$\mathop {\lim }\limits_{t \to 0} {\boldsymbol{s}} = 0$
.
In conclusion, when
${{\boldsymbol{s}}^{\rm T}}{{\boldsymbol{u}}_3} \lt 0$
and
${{\boldsymbol{s}}^{\rm T}}{{\boldsymbol{u}}_3} \le - {{\boldsymbol{K}}_{\rm s}}(\left\| {\boldsymbol{s}} \right\| - \frac{{{{\left\| {\boldsymbol{s}} \right\|}^2}}}{{\left\| \boldsymbol\Phi \right\|}})$
,
$\dot{{\boldsymbol{V}}} \le 0$
,
${\boldsymbol{s}}$
,
${\boldsymbol{e}}$
,
$\dot{{\boldsymbol{e}}}$
are asymptotically stable.
To satisfy the above conditions, a one-input one-output fuzzy controller is designed. The input variable is
${\boldsymbol{s}}$
, and the output variable is
${{\boldsymbol{u}}_3}$
. The membership function of the input variable
${\boldsymbol{s}}$
is shown in Fig. 3. The membership function of output variables
${{\boldsymbol{u}}_3}$
is shown in Fig. 4. Where
$\Phi $
is the design parameter defined in Eq. (32),
$\Omega $
is a new design parameter which can be selected by trial and experience. The fuzzy controller’s working principle is:
${{\boldsymbol{u}}_3}$
can be chosen appropriately according to
${\boldsymbol{s}}$
’s value to satisfy the requirements of system control. The fuzzy base rule is shown in Table I in which the following abbreviations have been used: NB: Negative Big; NM: Negative Medium; NS: Negative Small; ANZ: Approach Negative Zero; APZ: Approach Positive Zero; PS: Positive Small; PM: Positive Medium; PB: Positive Big. For example, when
${\boldsymbol{s}}$
is NB,
${{\boldsymbol{u}}_3}$
is PS; when
${\boldsymbol{s}}$
is NM,
${{\boldsymbol{u}}_3}$
is PM. Finally, we use the center of gravity method to solve the fuzzy problem.
Table I. The fuzzy rules.


Figure 3. Membership function of
${\boldsymbol{s}}$
.

Figure 4. Membership function of
${{\boldsymbol{u}}_3}$
.
3.2. The fast subsystem
The fast subsystem describes the system’s flexible movement. The flexible joints and the flexible link will not only affect the control but also produce vibration. And, their vibration levels are not the same. So, we further decompose the fast subsystem into two independent sub-sub systems: the flexible-joint fast subsystem and the flexible-link fast subsystem. The flexible-joint fast subsystem describes the system’s flexible movement caused by the flexible joints. And, the flexible-link fast subsystem describes the system’s flexible movement caused by the flexible link. The flexible-joint fast subsystem’s controller
${\tau _{\rm f1}}$
is designed to suppress the vibration caused by the flexible joints. The flexible-link fast subsystem’s controller
${\boldsymbol\tau _{\rm f2}}$
is used to suppress the vibration caused by the flexible-link actively. So, the total controller for the fast subsystem is:
${\boldsymbol\tau _{\rm f}} = {\boldsymbol\tau _{\rm f1}} + {\boldsymbol\tau _{\rm f2}}$
.
3.2.1. The flexible-joint fast subsystem
Now, only the influence of the flexible joints is considered. So, let
$\boldsymbol\delta = 0$
in Eq. (16), the dynamic equation of the rigid-link and flexible-joints system is obtained as:


where
${\boldsymbol\tau _{\rm k1}} = {\boldsymbol\tau _{\rm s}} + {\boldsymbol\tau _{\rm f1}} + {\boldsymbol\tau _{\rm d}}$
.
The feedback controller is designed as following

where
${{\boldsymbol{K}}_{\rm f}} = {{\boldsymbol{K}}_2}/{{\rm{\varepsilon }}^2}$
,
${{\boldsymbol{K}}_2}$
is a positive definite diagonal matrix.
The controller can adjust
${{\boldsymbol{K}}_{\rm f}}$
in time according to the difference of the link’s rotation angular velocity
${\dot{{\boldsymbol{q}}}_\rm{\theta } }$
and the motor rotor’s rotation angular velocity
$\dot{\boldsymbol\theta} $
. The stability of the flexible-joint fast subsystem is ensured. Combining with Eq. (38), the flexible-joint fast subsystem’s dynamic equation is:

3.2.2. The flexible-link fast subsystem
Now, only the influence of the flexible link is considered. So let
$\boldsymbol\theta = {{\boldsymbol{q}}_\rm{\theta } }$
,
$\dot{\boldsymbol\theta} = {\dot{{\boldsymbol{q}}}_\rm{\theta } }$
in Eq. (16), the dynamic equation of the flexible-link and rigid-joints system is obtained as:


where
${\boldsymbol\tau _{\rm k2}} = {\boldsymbol\tau _{\rm s}} + {\boldsymbol\tau _{\rm f2}} + {\boldsymbol\tau _{\rm d}}$
,
$${\boldsymbol{G}}_{11}^* = {\left( {\left[ {\matrix{
{1\quad 0} \cr
{0\quad 1} \cr
} } \right] + {{\boldsymbol{G}}_{11}}{J_\theta }} \right)^{ - 1}}{{\boldsymbol{G}}_{11}}$$
,
$${\boldsymbol{G}}_{12}^* = {\left( {\left[ {\matrix{
{1\quad 0} \cr
{0\quad 1} \cr
} } \right] + {{\boldsymbol{G}}_{11}}{J_\theta }} \right)^{ - 1}}{{\boldsymbol{G}}_{12}}$$
,
$${\boldsymbol{G}}_{21}^* = {{\boldsymbol{G}}_{21}} - {\left( {\left[ {\matrix{
{1\quad 0} \cr
{0\quad 1} \cr
} } \right] + {{\boldsymbol{G}}_{11}}{J_\theta }} \right)^{ - 1}}{{\boldsymbol{G}}_{21}}{J_\theta }{{\boldsymbol{G}}_{11}}$$
,
$${\boldsymbol{G}}_{22}^* = {{\boldsymbol{G}}_{22}} - {\left( {\left[ {\matrix{
{1\quad 0} \cr
{0\quad 1} \cr
} } \right] + {{\boldsymbol{G}}_{11}}{J_\theta }} \right)^{ - 1}}{{\boldsymbol{G}}_{21}}{J_\theta }{{\boldsymbol{G}}_{12}}$$
.
Definite a fast time variant:
${{\boldsymbol{t}}_{\rm f}} = {\boldsymbol{t}}/{\varepsilon ^2}$
, and its modifications:
${{\boldsymbol{z}}_{\rm f1}} = {{\boldsymbol{z}}_{
{\delta }} } - {\bar{{\boldsymbol{z}}}_{
{\delta }} }$
and
${{\boldsymbol{z}}_{\rm f2}} = {\varepsilon ^2}{\dot{{\boldsymbol{z}}}_{
{\delta }} }$
. In the fast subsystem, the slow variables can be regarded as constants, that is,
${\rm d}{\bar{{\boldsymbol{z}}}_{
{\delta }} }/{\rm d}{{{t}}_{\rm f}} = {\varepsilon ^2}{\dot{\bar{{\boldsymbol{z}}}}_{
{\delta }} } = 0$
. Let
${\rm{\varepsilon }} = 0$
, the dynamic equation of the flexible-link fast subsystem can be obtained as:

where
${{\boldsymbol{Z}}_{\rm f}} = \left[ {\begin{array}{c}{{{\boldsymbol{z}}_{\rm f1}}}\\[4pt]{{{\boldsymbol{z}}_{\rm f2}}}\end{array}} \right]$
,
$${{\boldsymbol{A}}_{\rm{f}}} = \left[ {\matrix{
0 & {\boldsymbol{I}} \cr
{ - \overline {\boldsymbol{G}} _{22}^*{{\boldsymbol{K}}_{\delta \varepsilon }}} & 0 \cr
} } \right]$$
,
${{\boldsymbol{B}}_{\rm f}} = \left[ {\begin{array}{c}0\\[4pt]{\bar{{\boldsymbol{G}}}_{21}^ * }\end{array}} \right]$
.
Because Eq. (42) is linear controlled, we can adjust the system state variable
${{\boldsymbol{Z}}_{\rm f}}$
using a linear-quadratic optimal controller. It can reach zero to realize the active suppression of the elastic vibration caused by the flexible link. Choosing the performance function of the optimal control:
${{\boldsymbol{J}}_{\rm f}} = \frac{1}{2}\int_0^\infty {({\boldsymbol{Z}}_{\rm f}^{\rm T}} {{\boldsymbol{Q}}_{\rm f}}{{\boldsymbol{Z}}_{\rm f}} + \boldsymbol\tau _{\rm f2}^{\rm T}{{\boldsymbol{R}}_{\rm f}}{\boldsymbol\tau _{\rm f2}}){\rm d}{{\boldsymbol{t}}_{\rm f}}$
, the controller can be designed as:

where
${{\boldsymbol{Q}}_{\rm f}}$
and
${{\boldsymbol{R}}_{\rm f}}$
are symmetric positive definite matrices;
${\boldsymbol{P}}$
is the only solution for the Ricatti equation [Reference Koskie, Couomarbatch and Gajic63]:
${\boldsymbol{P}}{{\boldsymbol{A}}_{f}} + {\boldsymbol{A}}_{f}^T{{\boldsymbol{P}}} - {\boldsymbol{P}}{{\boldsymbol{B}}_{f}}{\boldsymbol{R}}_{f}^{ - 1}{\boldsymbol{B}}_{f}^{T}{\boldsymbol{P}} + {{\boldsymbol{Q}}_{f}} = 0$
.
4. Simulation
We use the proposed hybrid controller to simulate the free-floating flexible-joints and flexible-link space manipulator system shown in Fig. 1. The actual values of the parameters in the system are:
${{{m}}_0} = 40{\rm{kg}}$
,
${{{m}}_1} = 2{\rm{kg}}$
,
${{\rho }} = 1{\rm{kg}}/{\rm m}$
,
${{{l}}_1} = 3{\rm{m}}$
,
${{{l}}_2} = 3{\rm{m}}$
,
${{EI}} = 300{\rm N} \cdot {{\rm m}^2}$
,
${{{J}}_0} = 34.17{\rm{kg}} \cdot {{\rm m}^2}$
,
${{{J}}_1} = 3{\rm{kg}} \cdot {{\rm m}^2}$
,
${{{J}}_{\rm{\theta } 1}} = {{{J}}_{\rm{\theta } 2}} = 0.5{\rm{kg}} \cdot {{\rm m}^2}$
,
${{{k}}_{\rm{\theta } 1}} = {{{k}}_{\rm{\theta } 2}} = 300{\rm N} \cdot {\rm m}/{\rm{rad}}$
. The flexible link is easy to deform, so
${{{l}}_2}$
is uncertain. In the simulation, its estimated value is:
${{{l}}_2} = 2.5{\rm m}$
. The fuzzy parameters are:
${{{\Phi }}_1} = {{{\Phi }}_2} = 1$
,
${{{\Omega }}_1} = {{{\Omega }}_2} = 10$
. The control parameters are:
$\lambda = diag(12,12)$
,
${{{l}}_{\rm d}} = 1$
,
${{{l}}_{\rm h}} = 1$
,
${{{l}}_t} = 2$
,
${{\boldsymbol{K}}_2} = {\rm{diag}}(100,100)$
,
${{\boldsymbol{Q}}_{ f}} = {\rm{diag}}(0.1,0.1)$
,
${{\boldsymbol{R}}_{ f}} = {\rm{diag}}(0.01,0.01)$
.
Simulation 1:
First, a simple simulation is taken. The desired trajectories are:
${{{q}}_{0\rm d}} = 0$
,
${{{q}}_{1\rm d}} = 0.1{\rm{rad}}$
,
${{{q}}_{2\rm d}} = 0$
. The initial states are:
$${\boldsymbol{q}}(0) = {\left[ {\matrix{
{0.05\quad 0\quad 0.1} \cr
} } \right]^{\rm{T}}}{\rm{rad}}$$
,
$${\boldsymbol{\theta }}(0) = {\left[ {\matrix{
{0\quad 0.1} \cr
} } \right]^{\rm{T}}}{\rm{rad}}$$
,
$${\boldsymbol{\delta }}\left( 0 \right) = {\left[ {\matrix{
{0\quad 0} \cr
} } \right]^{\rm{T}}}m$$
. The simulation time:
${{t}} = 10{\rm s}$
. None external interference signal.
The simulation results are shown in Figs. 5–8. Figure 5 is the space manipulator trajectory tracking error curve. Figure 6 is the curve of the flexible link’s mode coordinate. Figure 7 is the flexible link’s deformation curve. Figure 8 shows the flexible-joints angle errors. We can see that the system’s trajectory tracking errors converge to zero (the error is only 0.009 rad). The flexible-link’s vibration is suppressed, and its deformation is compensated. The flexible-joints angle errors are decreased. The control is effective.

Figure 5. The space manipulator trajectory tracking errors.

Figure 6. The flexible link’s mode coordinate.

Figure 7. The flexible link’s deformation.

Figure 8. The flexible-joints angle errors
$\sigma $
.

Figure 9. The space manipulator trajectory tracking errors.
But, the desired trajectories are simple, and the external interference is not considered in simulation 1. So, simulation 2 is taken.
Simulation 2:
The desired trajectories are:
${{\rm{q}}_{0{\rm d}}} = \frac{\pi }{4}\left[ {\frac{{\rm{t}}}{{10}} - \frac{1}{{2\pi }}\sin \left( {\frac{\pi }{5}{\rm{t}}} \right)} \right]$
,
${{\rm{q}}_{1{\rm d}}} = \frac{\pi }{2}\left[ {\frac{{\rm{t}}}{{10}} - \frac{1}{{2\pi }}\sin \left( {\frac{\pi }{5}{\rm{t}}} \right)} \right]$
,
${{\rm{q}}_{2{\rm d}}} = \frac{\pi }{2}\left[ {1 - \frac{{\rm{t}}}{{10}} + \frac{1}{{2\pi }}\sin \left( {\frac{\pi }{5}{\rm{t}}} \right)} \right]$
. The initial state is:
$${\boldsymbol{q}}(0) = {[\matrix{
{0\quad 0.1\quad 1.5} \cr
} ]^{\rm{T}}}{\rm{rad}}$$
,
$${\boldsymbol{\theta }}(0) = {[\matrix{
{0.1\quad 1.5} \cr
} ]^{\rm{T}}}{\rm{rad}}$$
,
$${\boldsymbol{\delta }}\left( 0 \right) = {[\matrix{
{0\quad 0} \cr
} ]^{\rm{T}}}m$$
. The simulation time:
${\rm{t}} = 10{\rm s}$
. The external interference signal is:
$${{\boldsymbol{\tau }}_{\rm{d}}} = {\left[ {\matrix{
{\sin ({\rm{t}})\quad \cos ({\rm{t}})} \cr
} } \right]^{\rm{T}}}{\rm{N}} \cdot {\rm{m}}$$
.
The simulation results are shown in Figs. 9–12. Figure 9 is the space manipulator trajectory tracking error curve. Figure 10 is the curve of the flexible link’s mode coordinate. Figure 11 is the flexible link’s deformation curve. Figure 12 shows the flexible-joints angle errors. The results show that the system can accurately track the desired trajectory (the error is only 0.015 rad). The flexible link’s deformation is compensated. The vibrations caused by the flexible joints and the flexible link can be suppressed.

Figure 10. The flexible link’s mode coordinate.

Figure 11. The flexible link’s deformation.

Figure 12. The flexible-joints angle errors
$\sigma $
.
The comparison experiments are also taken in simulation 2 to prove the effectiveness of the hybrid control:
Case 1: Turn off the fuzzy controller
${{\boldsymbol{u}}_3}$
. The simulation results are shown in Figs. 13 and 14. We can find that, when
${{\boldsymbol{u}}_3}$
is closed, the system’s tracking errors and the flexible-joints angle errors increase, the control precision decreases.

Figure 13. The space manipulator trajectory tracking errors when
${{\boldsymbol{u}}_3}$
is closed.

Figure 14. The flexible-joints angle errors
$\sigma $
when
${{\boldsymbol{u}}_3}$
is closed.
Case 2: Turn off the fast controller
${\boldsymbol\tau _{\rm f}}$
. The simulation results are shown in Figs. 15–18. We can find that, when
${\boldsymbol\tau _{\rm f}}$
is closed, the trajectory tracking errors and the flexible-joints angle errors became large in <1.2 s, the flexible-link’s vibration cannot be suppressed and its deformation cannot be compensated. That is, the system fails to track. So, the effectiveness of
${\boldsymbol\tau _{\rm f}}$
is proved.

Figure 15. The space manipulator trajectory tracking errors when
${\boldsymbol\tau _{\rm f}}$
is closed.

Figure 16. The flexible link’s mode coordinate when
${\boldsymbol\tau _{\rm f}}$
is closed.

Figure 17. The flexible link’s deformation when
${\boldsymbol\tau _{\rm f}}$
is closed.

Figure 18. The flexible-joints angle errors
$\sigma $
when
${\boldsymbol\tau _{\rm f}}$
is closed.
5. Conclusion
In this paper, the free-floating space manipulator system with flexible-joints, flexible-link, uncertain parameters, and external interference is studied. First, combining the assumed mode method, the system’s linear momentum conservation, angular momentum conservation, and Lagrange equation, the system’s dynamic equation is established. Considering that this is a rigid-flexible hybrid system, the system dynamics singular perturbation model is established according to the singular perturbation method. Then, a hybrid control is proposed, composed of the slow subsystem’s robust fuzzy sliding mode control, the flexible-joints fast subsystem’s speed difference feedback control, and the flexible-link fast subsystem’s linear-quadratic optimal control. The MATLAB simulations with different desired trajectories and external interference are taken. The simulation results proved that the hybrid control could control the system to track the desired trajectory accurately and suppress the vibration caused by the flexible joints and the flexible link. The controller has the advantages of real-time feedback, self-adaptation, and fewer calculations.
However, we also found that the error’s convergence speed is not fast enough, the vibration is evident at the initial stage of the response, and the results did not reach the optimal state. That may be related to the strong coupling and non-linearity of the system and the double flexibility. Improving and optimizing the control performance will be my main task in the future.
Acknowledgments
This research is supported by the National Natural Science Foundation of China (No. 51741502, 11372073, and 11072061).
Conflicts of Interest
The author(s) declare none.
Appendix:
$\boldsymbol{M}(\boldsymbol{q},\boldsymbol{\delta} )$
and
$\boldsymbol{H}(\boldsymbol{q},\dot{\boldsymbol{q}},\boldsymbol{\delta} ,\dot{\boldsymbol{\delta}} )$
in Dynamic Eq. (10)


where
