The combination of natural mineral matrices and chemical compounds often leads to products with interesting and unique properties (Gomez-Romero & Sanchez, Reference Gómez-Romero and Sanchez2004; Ruiz-Hitzky & Van Meerbek, Reference Ruiz-Hitzky, Van Meerbek, Bergaya, Theng and Lagaly2006). From a physicochemical point of view, this process permits the formation of bi- or multi-functional materials, combining the chemical and physical properties of the two end-members (Alexandre & Dubois, Reference Alexandre and Dubois2000; Pinnavaia & Beall, Reference Pinnavaia and Beall2000; Ray & Okamoto, Reference Ray and Okamoto2003; Carrado, Reference Carrado, Auerbach, Carrado and Dutta2004). This combination often leads to the modification of the physicochemical properties of the support mineral, such as the specific surface area, adsorption, hydrophobicity, etc. Functional chemical species may be immobilized and stabilized on suitable substrates or layers. Among the nanohybrid materials, clay–photocatalyst composites are promising due, in particular, to the broad availability of natural clay minerals and their ability to incorporate a large variety of functional molecules on their surfaces (Tunney & Detellier, Reference Tunney and Detellier1996; Elbokl & Detellier, Reference Elbokl and Detellier2006, Reference Elbokl and Detellier2009; Fernandez-Saavedra et al., Reference Fernandez-Saavedra, Darder, Gomez-Aviles, Aranda and Ruiz-Hitzky2008; Letaief et al., Reference Letaief, Aranda, Fernandez-Saavedra, Margeson, Detellier and Ruiz-Hitzky2008; Defontaine et al., Reference Defontaine, Barichard, Letaief, Feng, Matsuura and Detellier2010).
Kaolin and diatomite are widely available geological materials that have been used for decades in their natural forms domestically and for environmental remediation issues. They are also applied in agriculture as natural insecticides, food protectants, cosmetics and paints (Fields et al., Reference Fields, Allen, Korunic, McLaughlin and Stathers2002; Faulde et al., Reference Faulde, Tisch and Scharninghausen2006; Ferraz et al., Reference Ferraz, Coroado, Silva, Gomes and Rocha2011; Leiviskä et al., Reference Leiviskä, Gehör, Eijärvi, Sarpola and Tanskanen2012). Due to strong interactions between the tetrahedral and the octahedral sheets through H-bonds and dipolar interactions in kaolinite, the main mineral of kaolins, direct intercalation of functional compounds into the kaolinite interlayer is rarely reported. Natural diatomite has a weak adsorption capacity because of its macrostructure. However, the SiO2 materials and clay minerals may be chemically activated to modify and enhance their adsorption capacity via increases in porosity and surface activity tuning for improved adsorbent–adsorbate interactions (Mokaya et al., Reference Mokaya, Jones, Davies and Whittle1993; Vicente Rodriguez et al., Reference Vicente Rodriguez, Suarez Barrios, Lopez Gonzalez and Banares Munoz1994; Komadel, Reference Komadel, Misaelides, Macasek, Pinnavaia and Collela1999; Ozcan & Ozcan, Reference Ozcan and Ozcan2004; Bergaya et al., Reference Bergaya, Theng and Lagaly2006; Plachá et al., Reference Plachá, Martynková and Rümmeli2008, Reference Plachá, Rosenbergová, Slabotínsky, Kutláková, Studentová and Martynková2014). TiO2 is widely used for its photocatalytic properties, being more active in the ultraviolet region. Though it is considered a non-toxic material (Warheit et al., Reference Warheit, Hoke, Finlay, Maria Donner, Reed and Sayes2007; Jiang et al., Reference Jiang, Mashayekhi and Xing2009), the possibility of it being biohazardous has still not been ruled out completely (Li et al., Reference Li, Zhu, Zhu, Xue, Sun, Yao and Wang2008). Therefore, direct utilization and discharge of TiO2 nanoparticles (NPs) and other photocatalysts into the environment should be discouraged. The most affordable and easiest way to achieve this is to anchor and secure TiO2 NP photocatalysts on the surface of a suitable substrate (Wang et al., Reference Wang, Du and Xu2009; Vimonses et al., Reference Vimonses, Chong and Jin2010). Aluminosilicates are cheap and abundant materials with unique physicochemical properties that characterize an excellent substrate for anchoring metal oxide NPs (Szabó et al., Reference Szabó, Németh and Dékány2003; Wang et al., Reference Wang, Du and Xu2009; Vimonses et al., Reference Vimonses, Chong and Jin2010). Recently, kaolin and diatomite were intercalated with Ag-TiO2 NPs, and the prepared photocatalyst nanocomposites exhibited enhanced functionalities for degradation and adsorption of pollutants (Cu2+ and Co2+) from high-concentration (100–1000 mg/L) aqueous solutions (Chong et al., Reference Chong, Tneu, Poh, Jin and Aryal2014; Ajenifuja et al., Reference Ajenifuja, Ajao and Ajayi2017a, Reference Ajenifuja, Ajao and Ajayi2017b). The use and control of mineral–photocatalyst NPs is easier than that of pure photocatalyst NPs, because their ceramic nature gives the nanocomposite its required physical integrity when in contact with pollutants (Burg et al., Reference Burg, Bak, Nowotny, Sheppard, Sorrell and Vance2007; Hathway & Jenks, Reference Hathway and Jenks2008; Wang et al., Reference Wang, Du and Xu2009). More information on the physical and chemical characterizations of photocatalyst–silica or aluminosilicate mineral ceramic nanocomposites is still necessary. In this study, kaolin and diatomite were modified with photocatalytic AgNP-TiO2 NPs via the sol–gel process and subsequent high-temperature sintering. Microstructural and thermal characterization of the ceramic nanocomposites were carried out, while porosimetry was performed to study the surface adsorptive properties.
MATERIALS AND METHODS
Materials
Diatomite silica and kaolin were obtained from the Nasarawa and Ekiti States of Nigeria, respectively. The samples were dried at 105°C for 2 h, and then cooled to room temperature for further treatment. Analytical-grade nitric acid (30% HNO3) was selected for acid leaching and activation. Analytical-grade silver nitrate (AgNO3), sodium carbonate (Na2CO3) and titanium dioxide (TiO2) were used to prepare Ag-TiO2 photocatalyst NPs via intercalation into the materials’ microstructures.
Chemical modification
Acid-treated kaolin (denoted as KLN) and diatomite (denoted as ZEO) were prepared from their raw materials. Acid treatment removed the fine impurities and carbonaceous materials, increasing the number of active sites on the crystallite surfaces and opening more pores in the microstructure for intercalation of photocatalyst Ag-TiO2 NPs (Fig. 1). Using the sol–gel technique, dispersions of modified Ag-TiO2 NPs (STOX) were prepared according to Ajenifuja et al. (Reference Ajenifuja, Ajao and Ajayi2017a, Reference Ajenifuja, Ajao and Ajayi2017b). For intercalation, 25 g of activated kaolin or diatomite were added slowly into the continuously stirred Ag-TiO2 colloidal solution (~10 g in 100 mL ethanol), and the slurry was stirred and mildly heated for 2 h on a hot plate. The intercalated Ag-TiO2-kaolin and Ag-TiO2-diatomite photocatalyst nanocomposites (denoted as STOX-K and STOX-Z, respectively) were recovered from the colloidal suspension via centrifugation and subsequent drying. Colour change from off-white to purplish-white was observed before sintering. The ceramic powders were further sintered at temperatures ranging between 900°C and 1000°C for 12 h for thermal fusion and densification of the constituents, and the final products were designated as STOX-KS and STOX-ZS, respectively.

Fig. 1. SEM images showing the morphology of the NPs of Ag-TiO2 (STOX) at (a) low and (b) high magnifications.
Physical and chemical characterization
The specific surface areas of KLN and ZEO, photocatalyst nanocomposite materials (STOX-K and STOX-Z) and sintered samples (STOX-KS and STOX-ZS) were obtained by nitrogen adsorption–desorption isotherms at 77.350°K and an ambient temperature of 22.0°C using a BET analyser (TriStar II 3020 version 2.00). Thermal characterization was performed with DSC (NETZSCH 404 PC). The surface and microstructural changes in the samples were studied with SEM (ZEISS DSM-940A) on carbon-coated samples. Elemental characterization of the samples before and after intercalation of the photocatalyst was performed by EDX. The elemental compositions of the acid-treated and intercalated minerals are listed in Table 1.
Table 1. EDX analysis of activated and intercalated natural materials. C is present due to the carbon coating of the samples.

RESULTS AND DISCUSSION
Microstructural analysis
The sol–gel-prepared Ag-TiO2 consists of evenly distributed networks of NPs of uniform size (Fig. 1). Each particle is an aggregate of smaller Ag-TiO2 particles (Fig. 1b). The micrographs of kaolin-based samples (KLN, STOX-K and STOX-KS) display changes in the microstructure after modification (Fig. 2). Dispersed crystallites of the Ag-TiO2-kaolin nanocomposite with well-defined grain surfaces are observed in the sintered STOX-KS sample, while the acid-treated sample KLN is largely composed of particle aggregates interspersed with compact masses of particles or grains. The unsintered intercalated nanocomposite STOX-K is microstructurally identical to KLN with larger aggregations of particles. Figure 3 shows the SEM images of diatomite-based ceramic photocatalysts. The Ag-TiO2 NPs are dispersed within the pores and channels, while some NPs attach to pores and mineral surfaces in sample STOX-Z. Comparing the sintered and unsintered diatomite photocatalyst nanocomposites, the original pore structure evolves into a zeolite-like homogeneous crystal structure (Fig. 3c). The notable morphological changes between ZEO and STOX-ZS ceramic particles indicate that the chemical and thermal processes successively decomposed the original structure of the diatomaceous material, forming a microstructure with various textural characteristics. Due to the heating, TiO2 NPs are now interspersed into and on the surface of the pores. The micrographs of sintered photocatalyst–mineral nanocomposites even show aggregation of particles of well-defined surface microstructures (Figs 2c, 3c). With increasing sintering temperature, the SiO2 catalyst is better crystallized and the number of defect sites is reduced, thereby enhancing photocatalytic activity (Wang et al., Reference Wang, Du and Xu2009).

Fig. 2. SEM images of the modified kaolin materials. (a) KLN sample showing aggregated lumpy and rod-like microstructures. (b) STOX-K sample intercalated with Ag-TiO2 prepared by the sol–gel technique. (c) STOX-KS with refined particulate surface morphology.

Fig. 3. SEM images of the modified kaolin materials. (a) Natural pores of the ZEO sample after treatment with HNO3. (b) STOX- Z sample intercalated with Ag-TiO2 prepared by the sol–gel technique. (c) Sintered intercalated sample STOX-ZS.
Physisorption hysteresis analysis
The N2-adsorption isotherm analysis is based on the International Union of Pure and Applied Chemistry (IUPAC) classification (Sing et al., Reference Sing, Everett, Haul, Moscou, Pierotti, Rouquerol and Siemieniewska1985). The isotherms of the treated materials and modified nanocomposite samples are shown in Figs 4 and 5 for samples KLN and ZEO, respectively. The original and modified materials display type III isotherms and H3 hysteresis loops. This indicates the presence of mesopores in the materials and an unrestricted multilayer formation, because the lateral interactions between adsorbed molecules are strong in comparison to interactions between the adsorbent and adsorbate. The H3 hysteresis loops are often caused by adsorption of non-polar gases on loose assemblages of plate-like particles, forming slit-pores. The shape of the hysteresis loops shows the non-rigid nature of the treated mineral (KLN/ZEO) and nanocomposite (STOX-K/STOX-Z) microstructures (Figs 4, 5). In addition, the sintered nanocomposites have distinct hysteresis loops (Figs 4, 5).

Fig. 4. Nitrogen adsorption/desorption isotherms for samples KLN, STOX-K and STOX-KS. STP = standard temperature and pressure.
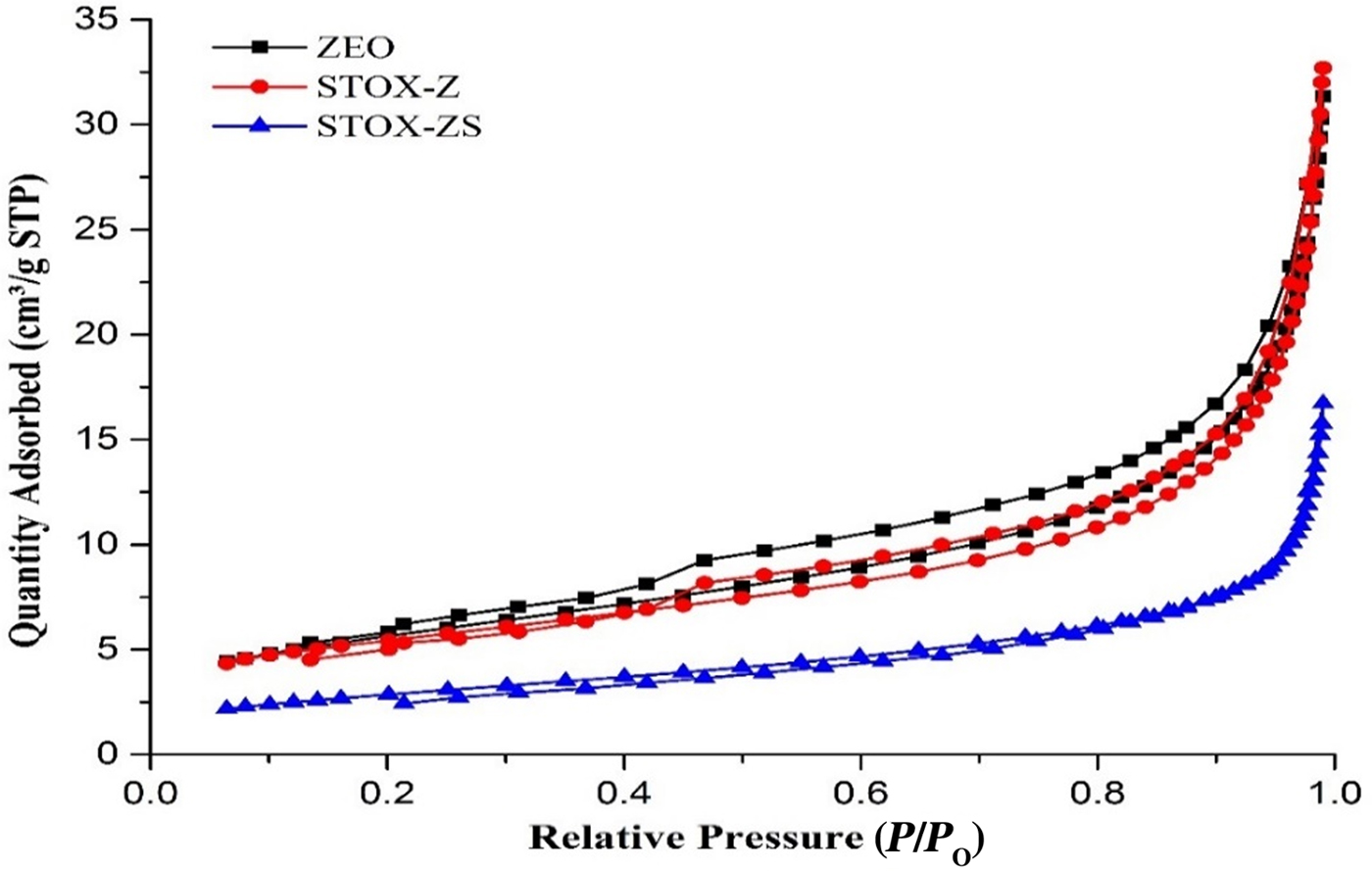
Fig. 5. Nitrogen adsorption/desorption isotherms for samples ZEO, STOX-Z and STOX-ZS. STP = standard temperature and pressure.
The isotherm for the acid-treated kaolin sample (KLN) exhibits real hysteresis between adsorption and desorption branches, with the gap decreasing slightly in the Ag-TiO2-intercalated sample STOX-K. In the sintered nanocomposite (STOX-KS), the hysteresis loop decreases further, with closure point at P/P 0 ~ 0.8, suggesting a greater number of macropores in grain boundaries in sintered photocatalyst nanocomposites. It follows that the adsorption type changes from chemical (chemisorption) to physical (physisorption). Before intercalation, the acid treatment improved the pore, surface and particle-size distributions of the materials (Samyn et al., Reference Samyn, Schoukens and Stanssens2015). Moreover, adsorption is irreversible in chemisorption, while it is reversible in physisorption, with adsorption and desorption processes following a common path (Rouquerol et al., Reference Rouquerol, Rouquerol and Sing1999). Reversible sorption is desirable in the recovery or recycling of the adsorbents for later use. Samples KLN and STOX-K display type II isotherms at lower P/P 0 values, with monolayer adsorption in the mesopores. Because the shape of the isotherm is partly dependent on the texture of the porous materials, chemical and thermal treatments induced microstructural changes in the materials.
The Ag-TiO2-diatomite photocatalyst nanocomposite samples (Fig. 5) display hysteresis loops and isotherms that are comparable to those of the kaolin samples (type H3 and type III, respectively), except for the smaller hysteresis between adsorption and desorption branches. The steep increase in N2 gas adsorption at intermediate relative pressures (P/P 0 = 0.3–0.6) for the ZEO and STOX-Z samples may be attributed to the presence of mesopores of uniform size (Li et al., Reference Li, Wu, Cui, Lu, Zhang and Yan2013). The increase in adsorption at high P/P 0 values corresponds to the activities of the macropores formed by agglomeration of the inherent mesoporous particles. In addition, the almost horizontal isotherm of the sintered STOX-KS sample at low relative pressure suggests the presence of narrow-slit pores in the micropore regions and multilayer formation with strong interaction between the adsorbed molecules (Kruk & Jaroniec, Reference Kruk and Jaroniec2001).
After intercalation and sintering, the adsorption–desorption isotherm of ZEO became totally reversible, indicating changes in the adsorbate–adsorbent interactions of the photocatalyst nanocomposites with the adherence of Ag-TiO2 NPs on their surface. Generally, the specific surface area decreased mainly due to inter- and intra-particle densification, which increased average grain size (Burg et al., Reference Burg, Bak, Nowotny, Sheppard, Sorrell and Vance2007; Bakhsh et al., Reference Bakhsh, Khalid and Hakeem2014), and the pore size increased from the annihilation of micropores within the microstructure after intercalation and sintering (Table 2). In all of the samples, the first few multilayers of the adsorbate gas seem to form before transition to the relatively high-pressure region, where hysteresis characteristics depend on the chemical treatments and intercalation of the photocatalysts.
Table 2. Specific surface area and porosity parameters for kaolin clay adsorbents.

Previous experimental studies (Ajenifuja et al., Reference Ajenifuja, Ajao and Ajayi2017a, Reference Ajenifuja, Ajao and Ajayi2017b) showed that the sintered nanocomposites exhibited greater degradation capacities and adsorption capacities for concentrated Cu2+ and Co2+ aqueous solutions (100–1000 mg/L). This is in agreement with previous studies on the effects of sintering temperature on the performance of photocatalyst–silica composites on the degradation of pollutants in aqueous suspensions (Du et al., Reference Du, Xu and Wang2008; Wang et al., Reference Wang, Du and Xu2009). With increasing sintering temperature, the crystallization of the catalyst–silica is enhanced and the number of defect sites is reduced (Hoffmann et al., Reference Hoffmann, Martin, Choi and Bahnemann1995; Carp et al., Reference Carp, Huisman and Reller2004). In addition, the intercalation of photocatalyst NPs in silica and aluminosilicate microstructures involves dispersion on the surface of these phases and retards grain growth within the NPs during sintering, which may diminish their activity due to the reduced specific surface area (Caratto et al., Reference Caratto, Aliakbarian, Casazza, Setti, Bernini, Perego and Ferretti2013). Therefore, photocatalyst crystallites supported on SiO2 substrates have smaller average particle sizes than those of the unsupported photocatalysts.
Surface and porosimetry analysis
Pure catalyst NPs might display lower degradation efficiencies due to self-aggregation (Caratto et al., Reference Caratto, Aliakbarian, Casazza, Setti, Bernini, Perego and Ferretti2013). However, intercalation of NPs into platelets and attachment on porous scaffolds or substrates affects their porosity while simultaneously enhancing the inherent surface properties of the composite. The physical parameters of the treated and nanocomposite samples are shown in Table 2. The acid-treated samples KLN and ZEO have relatively high specific surface areas (S BET = 20.24 and 19.58 m2/g, respectively) compared to the sintered intercalated samples. The specific surface area of natural diatomite is ~3.81 ± 0.1 m2/g (Tsai et al., Reference Tsai, Lai and Hsien2006); hence, acid treatment opened more pores and reduced the grain size of mineral particles. After intercalation and sintering, and due to the anchoring of the catalyst NPs on the silica substrates, the specific surface area of the nanocomposite material decreases remarkably, especially after sintering (S BET = 5.45 and 10.15 m2/g for the STOX-KS and ZTOX-ZS, respectively). This might be attributed to the increase in crystallite size due to grain growth and photocatalyst NP precipitation on silica particles during sintering. Grain growth occurs when recovery and recrystallization are complete within the material. Because treated aluminosilicate boundaries are areas of high energy, they make excellent sites for the nucleation of photocatalyst NPs and other secondary phases. After sintering, remarkable reduction in the surface area was observed as a result of a reduction in the actual number of grains per volume of the nanocomposite (Hubbard, Reference Hubbard2002; Ratke & Voorhees, Reference Ratke and Voorhees2002).
Another effect of sintering on homogeneous or composite materials is densification, which reduces total porosity. Although the pore size of photocatalyst–diatomite nanocomposites reduced slightly after sintering, the pore size of photocatalyst–kaolin composites increased significantly. This difference is attributed to the various microstructural properties of the materials. Diatomites are inherently microporous materials with well-defined channels and pores, but kaolins are mainly porous at the grain boundaries and within the kaolinite platelets. The photocatalyst NPs in sample STOX-ZS are distributed evenly on the surface and in the pore channels of the diatomite microstructure, thereby reducing the pore diameter (Fig. 3c). The larger pores observed on the sintered kaolin nanocomposite are mainly located at grain boundaries and between the kaolinite layers. Because the treated kaolin was heated to >1050°C during sintering, the adjacent spinel phase might have nucleated and transformed into mullite and cristobalite (Tomura et al., Reference Tomura, Shibasaki, Mizuta and Kitamura1985; Deer et al., Reference Deer, Howie and Zussman1994; Bellotto et al., Reference Bellotto, Gualtieri, Artioli and Clark1995; Huertas et al., Reference Huertas, Fiore, Huertas and Linares1999). In spite of the increase in the pore size for sintered kaolin nanocomposites, the pore volume was relatively low, which is probably due to the densification and grain growth induced by sintering. Modification of photocatalyst NPs anchored on suitable mineral substrates rather than the use of pure NPs has been well established in previous studies (Kay et al., Reference Kay, Cesar and Grätzel2006; Wang et al., Reference Wang, Du and Xu2009). It reduces costs significantly, because the materials are naturally available and abundant and there is no subsequent effect on the environment.
Thermal analysis
The DSC curves of photocatalyst TiO2 (TOX) and STOX NPs are shown in Fig. 6. Both TiO2-based samples exhibited initial endothermic reactions at 93.4°C and 94.3°C, respectively, which might be attributed to the release of adsorbed water. Further heating led to dual endothermic events at 804.2°C and 866.0°C (STOX) and 819.1°C and 883.7°C (TOX). The endothermic events are attributed to a successive phase transition and recrystallization of the TiO2 NPs. The left-shift of the dual endothermic events for STOX might be attributed to the influence of Ag-NPs on the TiO2 NPs. Metastable anatase and brookite TiO2 phases usually convert irreversibly to the stable rutile phase upon heating to >600–800°C (Greenwood & Earnshaw, Reference Greenwood and Earnshaw1984). The broad exothermic peak at 1154°C in pure TOX samples is attributed to phase recrystallization by solid-state reaction encouraged by oxidation and grain growth by Ostwald ripening. Moreover, at 1175.3°C, an endothermic peak was observed for STOX samples, in contrast to the exothermic reaction observed in TOX samples at that temperature. This could be ascribed to the phase transformation due to melting of the doping silver NPs in the TiO2 matrix.

Fig. 6. DSC thermograms showing thermal transformations of samples TOX and STOX.
The DSC curves obtained for the acid-treated mineral particles exhibit both exothermic and endothermic events, and transformations are shown in Figs 6–8. Owing to the open-frame structure in geological minerals, water molecules are often trapped in their frameworks. The various thermal behaviours of the acid-treated diatomite (ZEO) and photocatalyst nanocomposite sample (STOX-Z) are depicted in Fig. 8. Endothermic and exothermic transformations are observed for the Ag-TiO2-diatomite nanocomposite at 762.3°C and 1153.9°C, respectively. An exothermic event attributed to recrystallization is also detected in sample ZEO at 1172.7°C. The events at low temperatures (103.6°C and 110.6°C) are ascribed to the removal or desorption of adsorbed water. Recrystallization of TiO2 NPs in the Si-rich microstructure into rutile is indicated by the endothermic peak at 762.3°C. For the acid-treated kaolin (KLN) and intercalated nanocomposite (STOX-K), low-temperature endothermic peaks were also observed at 131.9°C and 121.8°C, closely followed by a set of related endothermic peaks at 294.3°C and 301.4°C (Fig. 7). The endothermic peaks in Fig. 7 are shifted to lower temperatures in the photocatalyst nanocomposite due to photocatalyst intercalation. The intense, well-defined endotherms observed between 500°C and 600°C for both materials are attributed to the dehydroxylation of kaolinite to form disordered metakaolin (Bellotto et al., Reference Bellotto, Gualtieri, Artioli and Clark1995). The thermal reaction observed in sample STOX-Z is also exhibited by STOX-K at 824.7°C. Finally, the sharp exothermic events at ~1004.2°C and ~1006.2°C for STOX-K and STOX-KS, respectively, signify nucleation of secondary phases and recrystallization of spinel phases into mullite and cristobalite.

Fig. 7. DSC thermograms showing thermal transformations of samples KLN and STOX-K.

Fig. 8. DSC thermograms showing thermal transformations of samples ZEO and STOX-Z.
CONCLUSION
Photocatalyst nanocomposite materials were prepared from Ag-TiO2 NPs and locally available kaolin and diatomite. Intercalation and relatively high-temperature sintering processes induced remarkable changes into the physical and chemical properties of the original materials. The changes indicated that kaolin and diatomite are suitable as photocatalyst composite and support materials for Ag-TiO2 NPs. The treated and nanocomposite samples showed multilayer N2 adsorption at low relative pressure (<0.4), while sintered samples are active at high P/P 0 (>0.6). Adsorption and desorption processes followed common paths in the BET analysis of the sintered nanocomposite samples, as was indicated by the reversible isotherms and a change from chemisorption to physisorption with sintering. Physisorption processes are highly desirable for material recovery after the degradation and removal of pollutants. Additionally, high-hysteresis closure points (P/P 0 ~ 0.8) indicate rigid pore structures and stable microstructural surfaces after sintering. Recrystallization of the material–photocatalyst nanocomposite by sintering improved the surface adhesion of the photocatalyst on the minerals.
ACKNOWLEDGEMENTS
The support of The World Academy of Science (TWAS) in collaboration with the National Research Foundation (NRF) towards this research is hereby acknowledged.