NOMENCLATURE
- ACARE
Advisory Council for Aviation Research and Innovation in Europe
- ALECSYS
Advanced Low Emission Combustion
- ALPS
Advanced Low Pressure System
- ANTLE
Affordable Near-Term Low Emissions
- CAEP
Committee on Aviation Environmental Protection
- CROR
Contra-Rotating Open Rotor
- EEFAE
Efficient and Environmentally Friendly Aero Engine (EFE)
- FP7
7th European Framework Program
- GTF
Geared Turbofan
- LPA
Large Passenger Aircraft
- LPT
Low Pressure Turbine
- NEWAC
New Aero Engine Core Concepts
- PACA
french Region “Provence – Alpes - Côte d'Azur″
- SAGE
Sustainable And Green Engines
- SRIA
Strategic Research and Innovation Agenda
- TRL
Technology Readiness Level
- UHBR
Ultra High Bypass Ratio
- VHBR
Very High Bypass Ratio
- WP
Work Package
1.0 INTRODUCTION
Rather than detailing both Clean Sky and Clean Sky 2 programmes according to their specific work breakdown structure, the choice has been made to present this vast research programme according to the various engine architectures which are of interest for the next-generation aircraft applications. Achievements in Clean Sky (2008–2017) and perspectives in the newly started Clean Sky 2 programme (2014–2024) are described, including propulsion systems for Small Air Transport and Eco Design Transverse Activities.
2.0 DEMONSTRATION PROGRAMMES BY ENGINE ARCHITECTURE
2.1 Open-rotor architectures (Safran Aircraft Engines)
All current advanced engine concepts which are candidates to be integrated on large transport aircraft are based on the principle of High, Ultrahigh Bypass Ratio (UHBR) or Geared (GTF) turbofans. After a short, intense feasibility phase conducted with two types of engines in the early 1980s, the approach to develop a Contra-Rotating Open Rotor (CROR) engine concept for the short/medium range class of aircraft is absolutely unique.
For short- and medium-range aircraft, the first GTF engines and the LEAP turbofan are now the most advanced and fuel-efficient state-of-the art solutions entering service. However, compared to the GTF and LEAP, the CROR concept is holding a potential of up to 15% further fuel burn reduction, a 30% reduction versus the well-known CFM56. To exploit this potential, Clean Sky 2 has to deliver a firm proof that the CROR engine concept can be produced, integrated and operated in an industrial environment with efforts competitive to other latest state-of-the-art concepts.
Clean Sky will deliver ground testing of a geared pusher Open Rotor engine within SAGE 2 project led by Safran Aircraft Engines (Fig. 1) followed by a flight test in Clean Sky 2 under the Large Passenger Aircraft platform (LPA WP 1.1.) in cooperation with Airbus.
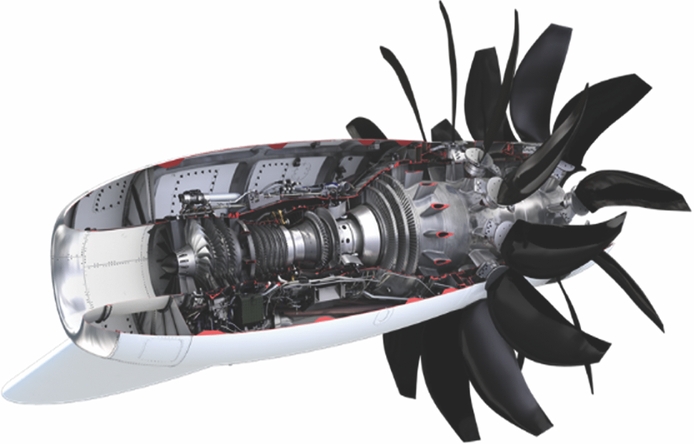
Figure 1. Contra-rotating open rotor (Safran Aircraft Engines).
The SAGE 2 project focuses on demonstrating the following technologies: composite propeller blades research activities including aero-acoustic optimisation, pitch control system, lightweight front and rear rotating frames including certification issues of rotating casing, controlling leakage at interfaces and reducing the weight, the contra-rotating reduction gearbox, the power turbine to reduce module weight and increase performance characteristics, lubrication and cooling systems, nacelle components and particularly rotating parts, control, protection and monitoring system and equipment, propeller blades electric de-icing system and equipment. The gas generator used in the SAGE 2 open rotor demonstrator is derived from a Safran Aircraft Engines M88 engine. The ground tests will start before summer 2017.
In Clean Sky 2, Safran Aircraft Engines will lead engine-related activities required to perform flight tests of a 2nd version of a geared Open Rotor demonstrator carrying on the Clean Sky SAGE 2 achievements. The current assumption is to use the Airbus A340-300 MSN001 test aircraft as flight test vehicle, with one full size CROR pusher engine attached to a representative pylon and engine mount installed at the port board side of the rear fuselage.
It must be noted that the overall roadmap for the future propulsion system of short/medium range aircraft will be subject to a number of reviews, both by the airframer and the engine manufacturer, with a decision of mid-2017.
As an in-kind contribution, Safran Aircraft Engines has invested in a new test bench for the Clean Sky SAGE 2 Ground Test, with support of the French Region PACA. This Open-Air Test Bench (Fig. 2) has been erected at Istres Flight Test Center and will be capable to test other advanced configurations of engines such as UHBR Turbofans.

Figure 2. Safran open air test bench, Istres, France.
2.2 UHBR turbofans – small and medium range aircraft (Safran Aircraft Engines)
For short/medium-range passenger aircraft, there is a need to open additional technology concept maturation avenues in order to fully explore the benefits and risks of Ultra High Bypass Ratio propulsion systems.
In Clean Sky 2, WP2, Safran Aircraft Engines leads the design, development and ground tests of a propulsion system demonstrator (Fig. 3) to validate the low-pressure modules and nacelle technology bricks necessary to enable an Ultra High Bypass Ratio engine. This includes considerations of the following technologies: advanced low-pressure-ratio fan/short air inlet adapted to Ultra High Bypass Ratio engines, low-weight structures; low-drag/low-noise ducts and nacelle, improved module technologies such as power gear box, low-pressure turbine, high-speed compressor booster, impact on the engine of innovative engine/airframe integration, optimisation according to aircraft mission and size.

Figure 3. Concept of the ultra high propulsive efficiency (UHPE) demonstrator for short/medium range applications (Safran Aircraft Engines).
The baseline configuration for the demonstrator is made of new low-pressure modules and nacelle parts integrated around an existing or adapted HP core in order to form the required ground demonstrator with a bypass ratio anticipated around 15. Impacts of innovative engine/airframe integration concepts chosen to improve propulsive efficiency will be taken into account.
Environmental gains should achieve up to 23% of CO2 emission reduction vs. 2000 aircraft, i.e. at least ACARE 2020 target assigned to engine. This goal is 9% better than the assumed 2014 reference status.
In addition to the Safran group subsidiaries (Safran Aircraft Engines, Safran Aero Boosters, Safran Transmission Systems, Safran Nacelles) participating to the Ultra High Propulsion Efficiency (UHPE) Demonstrator; this project brings together several partners: GKN Aerospace, GE-Deutschland and GE-Avio.
The engine architecture has been frozen mid-2016.
2.3 Large VHBR turbofan architectures – long range aircraft (Rolls-Royce)
The trend to Very High Bypass Ratio (VHBR) engines requires technology developments across a broad range of complex gas turbine systems, from fan inlet through the complete compression, combustion and turbine to exhaust.
The SAGE 3 project, led by Rolls-Royce, has demonstrated technologies applicable to large 3-shaft turbofan engines in the 60,000–95,000 lbs thrust class, with a focus on an Advanced Low-Pressure System (ALPS), externals and compressor structures technologies: lightweight composite fan system, including composite fan blades, composite fan case and all supporting hardware, lightweight integrated engine externals for fan-case and core-mounting dressings. The intake is developed in conjunction with the composite-fan case and optimised for the composite fan as an aerodynamic and structural system, including noise reduction technologies, lightweight new materials and construction techniques for low-pressure turbines.
Technologies for higher efficiency low-pressure turbines, through aerodynamic developments such as blade clocking and more advanced secondary cooling flow control, was developed by ITP – this includes materials and construction techniques for compressor inter-cases, focusing on topology optimisation, manufacturing techniques to enable thin sections and materials with higher temperature capability.
The ALPS engine has undergone a series of tests on the basis of a Rolls-Royce Trent 1000, for functional and structural capability of advanced dressings, for flutter and aerodynamic performance, for composite fan system flutter behaviour under cross-wind conditions and noise performance, and for the low-pressure turbine performance, thermal and structural behaviour. Flight tests of the engine have been successfully performed in October 2014 to demonstrate the composite fan blade in-flight operability.
Additional ground testing is planned to assess blade integrity and bird impact capability for the composite fan system as well as icing tests to determine ice shedding behaviour of blades and impact damage tolerances of new liners. This technological development demonstrated a 3% to 5% of CO2 reduction as a result of the introduction of those new technologies (−1% to 3% from the composite fan, −0.1% to 0.2% from advanced integrated externals and −1% to 2% from low-weight LPT), including a −2 EPNdB measured noise reduction from the composite fan system.
Besides this ongoing work on the engine architecture itself, the SAGE6 project has been established to house the Lean Burn programme and will deliver a Lean Burn Combustion System demonstrator engine for ground testing.
Lean Burn Combustion is a key technology acquisition for the European aerospace industry if it is to comply with future CAEP & ACARE emissions legislation, and for its products to remain competitive in the world marketplace. The aim of the SAGE 6 Lean Burn project is to demonstrate a Lean-Burn whole-engine system to a TRL6 maturity level, suitable for incorporation into civil aerospace applications in the 30,000 lb to 100,000+ lb thrust classes. In doing so, it is expected that the resulting technology will achieve compliance (with margin) to all planned future legislation.
Work to develop the technology for civil aerospace applications has, to date, used demonstrator programmes such as ANTLE/POA, E3E and EFE. All of these experiments have identified significant challenges beyond the combustor that require development of complementary systems to achieve an operable and certifiable product. The integrated system, which consists of technologies across the engine architecture (e.g. control systems, sensing and noise technologies) must be able to address many often conflicting requirements to provide a high-accuracy fuel supply to separate pilot and mains feed within the combustor. Significant technologies which are being developed during this programme consist of, but are not limited to, combustion, hydro-mechanical fuel control, control laws and associated sensing devices, whole-engine thermal management, acoustic attenuation, turbomachinery thermomechanical integration and system health monitoring and maintenance functions.
In Clean Sky 2, under WP5 and WP6, also led by Rolls-Royce, the technologies will be further advanced by introducing geared transmission between the fan and LP turbine. In terms of engine architecture, an even higher bypass-ratio in the range of 15will be achieved. Engine architectures incorporating a reduction gearbox should achieve another 5% fuel burn and CO2 emission reduction capability relative to equivalent direct-drive engines. Noise levels would also make a significant step towards to ACARE 2035 targets (−11 EPNdB per operation relative to a year 2000 benchmark: including engine, nacelle, aircraft technologies – airframe noise reduction, novel aircraft configurations – and ATM benefits).
In particular, research and demonstration of underlying capability is required in the following key areas: behaviour of fans at low speeds and fan pressure ratios, including fan stall margin and the effect of variable cold-nozzle geometries on the fan operability, intermediate-pressure compression system due to changes in air inlet conditions and pressure ratio requirements, aerodynamic and structural design of multi-stage Intermediate Pressure turbines, considering the structural effects of higher speeds and maximising turbine efficiency within a compact structure. Systems integration of novel accessory and reduction power gearboxes would also have to be developed and demonstrated. This includes the oil system and bearing technologies, integration of engine and nacelle structures to support the power gearbox and maximise the overall efficiency of the power plant structure, as well as associated control and electrical power system technology developments integrating the control of all system components.
In Clean Sky 2, Rolls-Royce will lead the design, development, building and testing of an engine to demonstrate these technologies at a scale suitable for large engines (Ultrafan™) (Fig. 4). Whole-engine design studies will define the detailed engine configuration, drawing on technology developments and demonstrations in WP5 to improve understanding of sub-system behaviours and allow system optimisation. Dependency on underlying technology development precludes an early engine definition but also allows the demonstrator to respond to changing requirements and for the benefits of each technology to be maximised within the overall system. A new core engine (Advance 3) with a redistributed work split between IP and HP spools is being developed as a new-core gas generator for the demonstrator, targeting a promising 20%+ increase in efficiency relative to Trent 700, considered as a year 2000 reference.
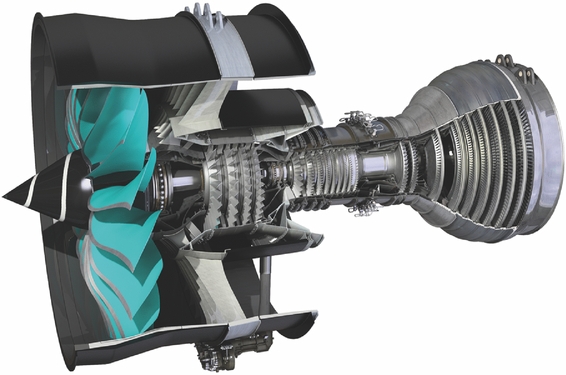
Figure 4. Ultra high bypass ratio engine (Rolls-Royce).
The engine development plan will require ground and flight testing, and it is envisaged that five engines will be built to satisfy these dual needs, with a period of ground testing (2019–2021) building confidence in the technology prior to flight tests currently planned beyond 2021. The flight test will be carried out in cooperation with Airbus. With a Bypass Ratio exceeding 15, the new Ultrafan engine concept should deliver a 25%+ efficiency increase versus Trent 700 for a planned EIS in 2025+.
2.4 Geared turbofans – small- and medium-range aircraft (MTU)
After successful technology developments, a first generation of geared fan engines has been selected to power new Regional Jets like the Bombardier C-Series but also enhanced Small- and Medium-Range Aircraft like the A320 neo. Today, aircraft fitted with Geared Turbofan engines (Fig. 5) are in service and prove double-digit savings in fuel consumption and superior low-noise characteristics.

Figure 5. Geared turbofan (MTU).
The SAGE 4 demonstrator programme is led by MTU Aero Engines to validate further advancements of the current geared fan technology. Together with more than 20 partners, the SAGE4 GTF demonstrator will provide significant contributions (>−15% versus reference year 2000) towards the ambitious targets of ACARE in 2020.
Components and modules with new numerous technologies have been further developed and validated through rig and component testing as required before being implemented into a 18,000 lbs thrust GTF donor engine: High efficient HP compressor technology building upon the NEWAC programme (Active Core work package) and national research programmes have been matured onto TRL6 level as well as high-speed, low-weight LP turbine and lightweight Exhaust Frame technologies derived from European research programmes such as CLEAN and VITAL or from national research programmes. These technologies have been recently demonstrated with the successful test campaign of the SAGE4 demonstrator in Q4 of 2015. All targets in terms of expected CO2 reduction were met at component level, i.e. −0.15% for the integrated drive system, −0.4% to −1.2% for the high efficiency compressor and −0.6% to −1.6% for the high-speed LPT.
Technologies for high efficient and advanced power gearbox systems are underway at Avio Aero and rig testing continues on a dedicated new test facility at the University of Pisa.
In Clean Sky 2, under WP4, MTU Aero Engines leads the design, development and testing of new rigs and an engine demonstrator to validate more key enablers to further reduce CO2 emissions (up to additional −10% versus the first generation GTFs, targeting −25% versus year 2000 reference) as well as engine weight and low noise levels.
The technologies, envisaged for demonstrator implementation address improvements of thermodynamic cycle efficiency by reducing parasitic energy flows (e.g. cooling and sealing air) and improving basic aerodynamic efficiency. Weight reduction through the introduction of advanced lightweight and temperature-resistant materials, lightweight structures through innovative design and advanced manufacturing processes are other key elements in WP4 technology development.
In particular, the interaction between LPC and HPC shall be studied and evaluated together with Deutsches Zentrum für Luft- und Raumfahrt (DLR) and GKN Aerospace in an integrated approach and will be tested first in a non-rotating Inter Case Duct (ICD) rig and later in a 2-shaft compressor rig to improve the aerodynamic design of this section of the compressor system
Additionally, development work will be performed together with GKN Aerospace on the exhaust system, to optimise interaction of the intermediate turbine duct with the LPT and the turbine exhaust casing, both from an aerodynamic and weight-saving point of view. In particular, the availability of innovative high-temperature low-density materials and adapted structural designs and manufacturing processes developed with support of CfP partner will be the key for these components to reduce weight and to save cooling air. Noise reduction efforts specifically addressed in LPT and exhaust system will complete WP4 technology development work.
The WP4 development plan reveals first rig testing in 2017 paving the way for a full 2-spool compressor rig test in 2020. The engine demonstrator test campaign to validate turbine and exhaust system technology is planned for 2019-2020. WP4 Compressor and Turbine technology development therefore fit well in the CS2 envelope and equally important will provide these technologies for implementation into the next generation of aircraft engines.
2.5 Turboshaft engines – helicopters (Safran Helicopter Engines)
The SAGE 5 project under Clean Sky shall provide Safran Helicopter Engines with the necessary technologies for the development of a new engine family equipping helicopter classes with a take-off weight from 3 tons (single-engine) to 6 tons (twin-engine).
The SAGE 5 project focuses on demonstrating the following technologies: high-efficiency compressor stages, small-size high-efficiency cooled HP turbine in order to improve performance and reduce dimensions of turboshaft engines and prepare a power growth capability, high-efficiency single-stage LP Turbine, materials and coating development and manufacturing techniques to enable static parts to cope with higher temperature, technologies for low-noise devices for a quiet exhaust, technology for inter-shaft architecture, technologies for control system through development of equipment aiming to reduce cost, weight/size or to enable higher temperature operation.
Additionally, technologies have been studied to develop a reliable and compact combustion chamber through development of size and weight decrease by studying a small-volume combustion chamber, reliability improvement and life-limit increase, optimisation of the combustion process and fuel injection system, technologies for low NOx combustion chamber and integration on turboshaft engine, study of the associated injectors and fuel system.
The first engine tests of the TECH 800 demonstrator (Fig. 6) have been performed in early February 2013, with subsequent runs until the end of 2015, demonstrating an effective 15% SFC reduction. Most of these technologies have been incorporated in the Safran Helicopter Engines's new engine in the 1,100 to 1,300 shp power class: the ARRANO, which had been selected in early 2015 as the exclusive engine for the Airbus Helicopters’ new twin-engine H160 helicopter.

Figure 6. TECH800 CAD model and engine demonstrator.
2.6 TurboProp engines – regional/SAT (Piaggio – GE Avio/Safran Helicopter Engines)
The gas-turbine technology has established its dominance in the aircraft propulsion applications due to a high power-to-weight ratio and reliability but its relatively high cost becomes very relevant when the power level decreases for small aircraft applications below 1,000 kW.
Recent advances in gas turbine technology focused on large engines with a big impact on improving aviation transport efficiency and greening but little effort has been made on small gas turbines. The small gas turbine engine is distinguished from large power engines not so much in terms of overall requirements (reliability, relative lower specific fuel consumption etc.), but rather in the severity of problems associated to achieve these requirements in small dimensions of various engine components. As a result, a compromise must be made on design architecture, materials selection, manufacturing processes, which are suitable to the particular needs of small turbine engines with reduced overall costs. It is clear that without improvements in small engine components design and material and manufacturing, this high-level target cannot be achieved.
In Clean Sky 2, within WP3, Safran Helicopter Engines will lead the design, development and ground testing of a new turboprop engine demonstrator in the 1,800–2,000 thermal HP class for business aviation and short range regional applications (Fig. 7).
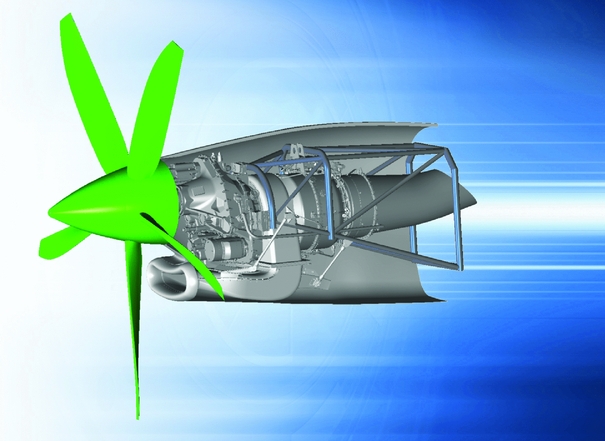
Figure 7. Concept of an advanced turboprop engine (Safran Helicopter Engines).
Safran Helicopter Engines proposes to design, develop and test a global propulsive system built around an adapted very modern existing turboshaft core engine called ARDIDEN3. The demonstration will address two technology challenges. The baseline core of ARDIDEN3 will be improved (compressor, combustion chamber for higher altitude operation, turbine and propulsive exhaust, specific control system) to better fit with the turboprop application. It will then be integrated with an innovative gear box, air inlet, propeller control system and propeller to be designed and developed specifically and ground tested. This concept of a fully optimised and integrated power plant system would deliver a −10 to −15% CO2 reduction from core engine improvements as well as an additional −5 to −8% reduction, thanks to power gearbox, nacelle (especially air intake) and propeller optimisation.
Under the lead of Piaggio Aero Industries (PAI) and GE Avio, in Clean Sky 2 ENGINE WP8, the consortium will address technical challenges to deliver the next generation turboprop engines in the lower power class (< 1,000 shp) for up to a 19-seat aircraft, proposing step-changes from current state-of-the-art and will deliver important improvements in engine technology, contributing to ACARE SRIA goals achievements.
The improvement of fuel efficiency and emissions, the extension of service life between overhauls and the reduction of the noise footprint will be the main drivers for the technology maturation plan and engine demonstration strategy. Specific attention is paid to technologies that are able to increase the competitiveness of the European industry in the small-turboprop gas-turbine engine sector, so far dominated by non-European companies.
This project will specifically deliver technologies sustaining the following high-level objectives: up to 15% of fuel-efficiency improvement versus 2014 reference engine, up to 10% of reduction of total operating costs versus 2014 reference engine, contribution to noise reduction including propeller of 10 db, and maintenance and strengthening of European competitiveness in Small Air Transport turboprop engines market.
Those technologies are focusing mainly on an advanced axi-radial compressor design, combustor technology studies, power turbine and exhaust improvements and propeller optimisation. The validation will be performed at rig level, and assessed globally by means of a virtual engine model. However, no engine demonstrator is planned within the frame of this project.
2.7 Small piston engines – small air transport (SAT) (Safran SMA)
The application of modern lightweight jet-fuel piston engines in aircraft operations brings important benefits in term of fuel burn and emissions. Compared to a year 2000 reference aircraft equipped with a small gas turbine, those engines may bring a 50% to 60% CO2 emission reduction. Compared to a year 2000 reference aircraft equipped with a piston engine, the fuel reduction is between 30% and 50%. In addition lead emissions are totally suppressed by the replacement of the aviation gas (Avgas) by the jet fuel.
The widespread presence of jet fuel (kerosene) over the world is also important especially in the regions where the aviation gas is not available or not really affordable.
The lightweight aircraft-optimised jet-fueled reciprocating engine more oriented towards a professional use is the step forward for the current piston engines. The platform of fuel-efficient piston engines (up to 400 HP) will bring the ecological benefit as well as the better reliability and cost-efficient service conditions for small aircraft having up to 12 seats for point-to-point transportation.
The work in Clean Sky 2 WP7 is led by Safran SMA and is focusing primarily on the increase of the power density of such engines, improving the core engine part design (material, design), both with technologies improvement and tests on a baseline (reference) four-cylinder engine. Then these technologies may be applied to a multi-cylinder architecture, e.g. a six cylinder (Fig. 8).

Figure 8. Safran SMA six-cylinder engine architecture.
An important part of this work concentrates on the specific design requirements for aircraft integration (system optimisation). The cooler's optimisation (efficiency/compactness) is a key part of the success.
Other important aspects will be treated, such as the turbocharger (altitude, long endurance), the propeller adaptation (torque pulse), and the Engine Control System (ECS). Those studies are currently planned up to a ground test demo on-wing towards the end of 2018, with obtaining of a permit-to-fly for an eventual subsequent flight test.
2.8 Eco-design
Aero-engine technologies are one of the key enablers for sustainable aviation and for achieving the goals defined in Europe's Flightpath 2050. Engines have a major influence on fuel consumption, emissions and noise in air travel. Fundamental engine technology developments to increase the engine performance, reduce fuel consumption, emissions and noise will be demonstrated in the ENGINES ITD work packages WP1 to WP8.
A dedicated WP 9 has been created and integrated into the ENGINES ITD to better understand and fully quantify the actual eco-benefit (or eco-penalties) of such technologies throughout the life cycle of the product as specifically materials, processes and resources employed for aero-engines are generally of very high ecologic and economic values.
Specific focus in WP9 is given to the following areas: additive manufacturing, recycling and re-use of composites and special metals and advanced production and manufacturing processes. The analysis in WP9 will enrich the Eco Design database with relevant information on materials, processes and resources for the above technology areas and will significantly contribute to the derivation of overall Eco Statements and Socio Economic Statements with regard to the global Clean Sky 2 Programme.
3.0 CONCLUSIONS
As already alluded to in the introduction of this paper, the Clean Sky 2 programme is clearly a continuation of the initial Clean Sky programme launched in 2008. Most of the engine concepts already addressed in Clean Sky are being further developed in Clean Sky 2 so as to achieve an effective TRL 6 validation of the technologies, in many cases, at least by ground tests or even up to flight tests.
Today, both programmes are clearly collecting the fruits of the long-lasting investments in lower TRL research through a long history of former European Framework Programmes, through national or regional funding schemes and of course also by the European Aeronautical Industry's own investments. Clean Sky (2008–2017/1.8 Bn€ budget) and Clean Sky 2 (2014–2024/4 Bn€ budget) are spanning well over a decade of applied research within the European aeronautical sector for all aircraft platforms. Regarding the aircraft engine area only, both programmes represent a research budget over 1 Bn€ over this timeframe. A number of successful demonstrations (both ground tests and flight tests) have already taken place following the Clean Sky programme and many more are still to come within Clean Sky 2.
However, beyond the financial aspect of investment in research and demonstration of Europe's future products, both programmes have achieved an exceptional involvement of all stakeholders of the Aeronautics Industry (more than 600 European entities), from large multi-Bn euro companies to small and medium enterprises, as well as universities and research centres, all contributing to promote Europe's competitiveness and secure its advanced technological position in the worldwide market.
Finally, from an environmental perspective, it is shown that all these developments, research and demonstration activities, are striving for the same objective of achieving the ambitious green targets set by ACARE. The environmental achievements of Clean Sky at Aircraft level are currently being assessed by the Technology Evaluator in Clean Sky and will be further pursued in Clean Sky 2.
Moreover, in Clean Sky 2, integration of Eco Design activities in the “ENGINES” Programme will allow the leverage of the environmental benefit of new technologies in the design, manufacturing and recycling of engine parts or materials.