In recent years, large global kaolin resources have attracted considerable attention as an alternative raw material to substitute for exhausted bauxite deposits (i.e. the principal aluminium ore worldwide). Kaolinite, which contains ~39% Al2O3 (Murray, Reference Murray2006), has been targeted for alumina production because of its abundance in the Earth's crust and because of its cost-effectiveness for recovering Al compared to other Al-bearing minerals (e.g. corundum, spinel, muscovite and alunite with respective Al2O3 contents of ~100%, 72%, 38% and 37%; Mikhailova et al., Reference Mikhailova, Konopleva, Yakovenchuk, Ivanyuk, Menshikov and Pakhomovsky2007; Biagioni & Pasero, Reference Biagioni and Pasero2014; Vdovets, Reference Vdovets2020; Li et al., Reference Li, Li, Chen, Liu, Huang and Zhou2021). In addition, kaolinite has the greatest Al2O3 content among all of the more abundant clay minerals (e.g. montmorillonite and illite with Al2O3 contents of ~19% and 17%, respectively; Battaglia, Reference Battaglia2004; Uddin, Reference Uddin2008). Moreover, kaolinite exhibits an intrinsically lower hardness (leading to cost-effective and energy-efficient grindability for producing ultrafine powders dominated by <2 μm size fractions) and a relatively low temperature of thermal decomposition (457–711°C) compared to non-clay Al-silicates (orthoclase, plagioclase, nepheline, leucite, kyanite and pyrope-garnet; Scorzelli et al., Reference Scorzelli, Bertolino, Luz, Duttine, Silva and Munayco2008; Aldabsheh et al., Reference Aldabsheh, Khoury, Wastiels and Rahier2015; ElDeeb & Brichkin, Reference ElDeeb and Brichkin2018; Erdemoğlu et al., Reference Erdemoğlu, Birinci and Uysal2018; Nzeukou Nzeugang et al., Reference Nzeukou Nzeugang, Ouahabi, Aziwo, Mache, Mefire Mounton and Fagel2018; Brichkin et al., Reference Brichkin, Kurtenkov, ElDeeb and Bormotov2019; ElDeeb et al., Reference ElDeeb, Brichkin, Kurtenkov and Bormotov2019; Pak et al., Reference Pak, Kirov, Nalivaiko, Ozherelkov and Gromov2019; Tantawy & Alomari, Reference Tantawy and Alomari2019; Sule & Sigalas, Reference Sule and Sigalas2020; Küster et al., Reference Küster, Kaufhold, Limam, Jatlaoui, Ba and Mohamed2021).
Generally, two processes have been proposed for Al2O3 extraction from clays and low-grade aluminium ores: the first is an acid process that uses sulfuric acid, hydrochloric acid or nitric acid to selectively dissolve the Al2O3, usually following calcination of the clay (Al-Zahrani & Abdul-Majid, Reference Al-Zahrani and Abdul-Majid2009; Ajemba & Onukwuli, Reference Ajemba and Onukwuli2012; Olaremu, Reference Olaremu2015; Toama et al., Reference Toama, Al-Ajeel and Jumaah2018); the second is an alkali process that uses water or a dilute alkali to selectively dissolve the Al2O3 from a sintered mixture of lime and clay or lime, soda and clay (Al-Ajeel et al., Reference Al-Ajeel, Abdullah, Muslim, Abdulkhader, Al-Halbosy and Al-Jumely2014; Guo et al., Reference Guo, Yan, Cui, Cheng and Lou2014; Li et al., Reference Li, Hui, Wang, Bao and Sun2014b; Zhang et al., Reference Zhang, Ou, Qiang, Niu and Komarneni2015a, Reference Zhang, Pan, Yu and Zhai2015b). The acidic leaching methods have disadvantages including difficult leaching conditions (i.e. leaching time, temperature and acid concentration, especially in low-grade aluminium ores) when compared with the alkaline leaching methods, in addition to the corrosion problems encountered by the leaching equipment due to acidic leaching. In addition, the amount of Al2O3 produced by acidic leaching is less than that produced by alkaline leaching due to the lower selectivity of acidic leaching agents. Therefore, complex purification techniques have been proposed to overcome the disadvantages of the acidic leaching process (Olaremu, Reference Olaremu2015; Valeev et al., Reference Valeev, Pak, Mikhailova, Gol'Dberg, Zheleznyi, Dorofievich and Williams2016).
Lime sintering has been considered to be the most appropriate and promising sintering method for Al2O3 extraction from kaolin among the combined pyro-hydrometallurgical processes, including the Bayer, soda-lime-sintering and lime-sintering methods. In the lime-sintering process, the kaolin fraction is proportionally mixed with limestone and the charge is then sintered at the optimum temperature (1360°C). During the sintering stage, the calcite component is decomposed completely into lime while the kaolinite is dehydroxylated to metakaolinite. These very chemically reactive phases form the leachable calcium aluminate compounds (12CaO.7Al2O3) and the dicalcium silicate compound (2CaO.SiO2; C2S), a non-leachable residual impurity. The Al2O3 content is then extracted efficiently from these calcium aluminate compounds via a hydrometallurgical leaching process using sodium carbonate solutions followed by washing with hot distilled water and by filtration, which yields a white sludge. The white sludge has the appropriate chemical and physical composition to make it suitable for the production of Portland cement (Chou & Burnet, Reference Chou and Burnet1981; Ptáček et al., Reference Ptáček, Opravil, Šoukal, Havlica and Holešinský2013; Al-Ajeel et al., Reference Al-Ajeel, Abdullah, Muslim, Abdulkhader, Al-Halbosy and Al-Jumely2014; Zhang et al., Reference Zhang, Pan, Yu and Zhai2015b; Sizyakov, Reference Sizyakov2016; Tian et al., Reference Tian, Pan, Yu and Tu2016b; Stange et al., Reference Stange, Lenting and Geisler2017; Azof et al., Reference Azof, Yang, Panias, Kolbeinsen and Safarian2019; ElDeeb et al., Reference ElDeeb, Brichkin, Kurtenkov and Bormotov2019, Reference ElDeeb, Brichkin, Bertau, Savinova and Kurtenkov2020a).
The lime-sintering process is the most cost-effective, time-efficient and energy-efficient method for alumina extraction from kaolin at 1360°C when compared with the other pyro-hydrometallurgical methods (i.e. the Bayer and the soda-lime-sintering methods; ElDeeb et al., Reference ElDeeb, Brichkin, Kurtenkov and Bormotov2019, Reference ElDeeb, Brichkin, Bertau, Savinova and Kurtenkov2020a). The advantages of the lime-sintering process result from the transformation of β-C2S into its γ-polymorph counterpart during the cooling stage. The resulting sinter self-decomposes into an ultrafine powder with a larger specific surface area that does not require pre-leach grinding and shows good leaching performance with minimal reagent consumption (Al-Ajeel et al., Reference Al-Ajeel, Abdullah, Muslim, Abdulkhader, Al-Halbosy and Al-Jumely2014; ElDeeb et al., Reference ElDeeb, Brichkin, Kurtenkov and Bormotov2019, Reference ElDeeb, Brichkin, Bertau, Savinova and Kurtenkov2020a; Pak et al., Reference Pak, Kirov, Nalivaiko, Ozherelkov and Gromov2019). Moreover, the resulting white sludge usually has a low Na2O content when compared with the resultant sludges produced by the soda-lime-sintering and Bayer methods and does not require intensive washing (Smith, Reference Smith2009; Kaußen & Friedrich, Reference Kaußen and Friedrich2018). The addition of soda ash (Na2CO3) in the case of the soda-lime-sintering method produces the sodium aluminate phase (Na2O.Al2O3) which prevents self-decomposition and hence represents an additional cost in the pre-leach grinding process (Bai et al., Reference Bai, Teng, Wang, Qin, Xu and Li2010; Guo et al., Reference Guo, Yan, Cui, Cheng and Lou2014; Tian et al., Reference Tian, Pan, Yu, Han, Tu, Bi and Williams2016a; Yan et al., Reference Yan, Guo, Li, Li, Cheng and Li2017; Toama et al., Reference Toama, Al-Ajeel and Jumaah2018). From an environmental viewpoint, the carbon dioxide (CO2) emissions from the sintering process are normally exploited as a by-product in the carbonization process for alumina precipitation from the alumina-rich solution (Gao et al., Reference Gao, Liang, Gou, Wei, Shen and Cheng2020).
Amorphization of the crystalline Al-bearing silicate phases into easily leachable amorphous phases is the most important process that controls Al2O3 extractability and recovery from the targeted non-bauxitic raw materials. It is mainly based on the ore grade and impurities in addition to the mineralogical and chemical composition and structural characteristics of the ore. The amorphization can be achieved via one or more synergetic combinations of the four common technological activation and treatment processes (which are mainly energy-efficient and cost-effective), including the thermal, mechanical, mechanochemical and thermochemical methods (Gasparini et al., Reference Gasparini, Tarantino, Ghigna, Riccardi, Cedillo-González, Siligardi and Zema2013; Cao et al., Reference Cao, Cao, Dong, Zhang and Sun2016). The treatment of kaolins is achieved via thermal activation during the sintering process at a controlled temperature. Dehydroxylation is the main mechanism in thermal activation, which results in the complete decomposition of the kaolinite structure into a quasi-amorphous material that is easily dissolved in dilute acidic and alkaline solutions, thereby increasing the leaching efficiency and Al2O3 recovery (Li et al., Reference Li, Zeng, Luo, Liu, Jiang and Qiu2014a; Xu et al., Reference Xu, Lao, Wu, Zhang, Xu and Li2015; Zhou et al., Reference Zhou, Liu, Fang and Lam2015; Birinci et al., Reference Birinci, Uysal, Erdemoğlu, Porgalı and Barry2017; D'Elia et al., Reference D'Elia, Pinto, Eramo, Giannossa, Ventruti and Laviano2018; Erdemoğlu et al., Reference Erdemoğlu, Birinci and Uysal2018; Yuan et al., Reference Yuan, Han, Li, Gao and Yu2018). Mechanical treatment with high-energy ball milling increases the specific surface area and structural disorder, decreases the apparent density and leads to amorphization of the kaolinite crystal structure. Hence, partial mechanical treatment also reduces the temperature of decomposition by increasing the structural disorder, thereby increasing the rate of phase transformation reactions during the sintering processes and increasing of leaching selectivity and efficiency (Tang et al., Reference Tang, Su, Li and Wei2010; Erdemoğlu & Baláž, Reference Erdemoğlu and Baláž2012; Allegretta et al., Reference Allegretta, Pinto and Eramo2016; Guo et al., Reference Guo, Yan, Cui and Cheng2016).
Recently, ElDeeb et al. (Reference ElDeeb, Brichkin, Kurtenkov and Bormotov2019, Reference ElDeeb, Brichkin, Bertau, Savinova and Kurtenkov2020a) applied the self-disintegration process by sintering kaolin with lime (lime-sintering process) at 1360°C, which is cost- and energy-effective and time-efficient, and therefore it is not necessary to grind the resulting sinter before leaching. The addition of fluxing agents such as charcoal to the kaolin-limestone mixtures in the sintering process would increase cost-effectiveness and energy-efficiency by reducing the temperature limit of the phase transformation (i.e. β-C2S to γ-phases). Moreover, the addition of charcoal would significantly improve the surface properties of the self-disintegrated sinter powders and particles and hence would increase leaching and maximize the alumina percentage recovery (APR; Qiu et al., Reference Qiu, Jiang, Li, Fan and Huang2004; Sizyakov et al., Reference Sizyakov, Dubovikov and Nikolaeva2013a, Reference Sizyakov, Dubovikov, Nikolaeva and Kalashnikova2013b; Dubovikov et al., Reference Dubovikov, Brichkin, Ris and Sundurov2018; Sizyakov & Brichkin, Reference Sizyakov and Brichkin2018; Li et al., Reference Li, Wang, Zhou, Qi, Liu and Peng2019). Previous work showed that other compounds such as MgO, Al2O3, Fe2O3, BaO, B2O3, Na2O, K2O, P2O5, MnO2 and Cr2O3, present either as chemical impurities or as fluxing additives to kaolin, were unfavourable because they stabilized the β-C2S phase and hence prevented self-disintegration (Wang et al., Reference Wang, Sun, Guo and Zhang2011; Yu et al., Reference Yu, Pan, Wang, Zhang, Sun and Bi2012, Reference Yu, Pan, Liu, Wang and Bi2014, Reference Yu, Pan, Dong and Wu2019; Guo et al., Reference Guo, Yan, Cui, Cheng and Lou2014; Yan et al., Reference Yan, Guo, Li, Li, Cheng and Li2017; Bazhirov et al., Reference Bazhirov, Dauletiyarov, Bazhirov, Serikbayev and Bazhirova2020).
The use of Na2O and FeO as fluxing agents to enhance Al2O3 extraction from the sintered kaolin and calcium carbonate produced solid solutions rich in C12A7 but inhibited the transformation of β-2CaO.SiO2 to γ-2CaO.SiO2 and hence the self-disintegration process (Wang et al., Reference Wang, Sun, Guo and Zhang2011, Reference Wang, Chu, Hao, Rong and Sun2017; Yu et al., Reference Yu, Pan, Wang, Zhang, Sun and Bi2012, Reference Yu, Pan, Liu, Wang and Bi2014). Yu et al. (Reference Yu, Pan, Dong and Wu2019) indicated that the self-disintegration of the sinters deteriorated with increasing phosphorous (P) content. In addition, the leaching rate of Al2O3 from the calcium aluminate sinters (and hence the APR) decreased with increasing P content by >0.5% as a result of the reduced self-disintegration. Therefore, the addition of 1.5–4.0 wt.% charcoal was considered to be the ideal amount of this fluxing agent because it initiated the self-disintegration process at a lower sintering temperature (1260°С) and increased cost-effectiveness as the resulting sinters did not require any pre-leach grinding. The chemical purity of the initial feed components had a significant effect on the self-disintegration process. As the chemical impurities were traces in the bulk composition of the precursor raw materials (kaolin and limestone; ElDeeb et al., Reference ElDeeb, Brichkin, Bertau, Savinova and Kurtenkov2020a), they did not have any undesirable effects on the efficiency of the self-disintegration process.
The functionality of charcoal as a fluxing agent for the thermochemical activation of the limestone–kaolin mixture to increase the recovery of the extracted alumina has yet to be studied. The addition of charcoal for this purpose is considered cost-effective, energy-effective and time-efficient. Therefore, the present study aims to examine, for the first time, the effects of thermochemical activation using charcoal as a fluxing additive on the microstructural changes, phase transformations, self-disintegration, leaching and hence Al2O3 recovery from the sintered limestone–kaolin mixture in Al2O3 extraction using the lime-sintering process.
Materials and methods
Raw materials
A high-grade white kaolin raw material collected from the Irkutsk mining site (Ivanov et al., Reference Ivanov, Pak, Nalivayko, Kirov and Bozhko2019) and a white limestone with some faint reddish tints obtained from the Pikalevo region, Russia (Sizyakov et al., Reference Sizyakov, Bazhin and Sizyakova2016) were used in the present study. The chemical and mineralogical compositions and the thermal characteristics of the raw kaolin and limestone samples were studied in detail in our previous works (ElDeeb et al., Reference ElDeeb, Brichkin, Kurtenkov and Bormotov2019, Reference ElDeeb, Brichkin, Bertau, Savinova and Kurtenkov2020a). The kaolin is composed of 31.9% Al2O3, 52.2% SiO2, 1.4% Fe2O3, 0.6% TiO2, 0.15% Na2O and 0.15% K2O corresponding to 81% kaolinite, 17% quartz and 2% Fe-Ti minerals (Awad et al., Reference Awad, López-Galindo, Sánchez-Espejo, Sainz-Díaz, El-Rahmany and Viseras2018b). The limestone is composed of 53.3% CaO (i.e. 95% calcite). A high-grade commercial charcoal composed of 86% fixed carbon and 8% volatiles and ash was purchased from Kyiv Company for Reagents (RIAP), Russia. The sodium carbonate (Na2CO3 of analytical grade) used in the leaching process was purchased from Vekton Company, Russia.
Sample preparation and sintering
The kaolin and limestone samples were crushed, pulverized and sieved to <74 μm. The limestone-kaolin mixture samples were prepared based on stoichiometric molar ratios using the bulk oxide contents: CaO/SiO2 = 2.0, CaO/Al2O3 = 1.8 and CaO/Fe2O3 = 1.0. The optimum proportional masses of the mixed kaolin and limestone powder fractions were 100.0 and 265.8 g, respectively, because these proportions yielded efficient leaching of aluminate phases and the maximum APR in our previous study (ElDeeb et al., Reference ElDeeb, Brichkin, Bertau, Savinova and Kurtenkov2020a).
To study the effects of the addition of charcoal, seven batch samples of kaolin-limestone-charcoal powder mixtures were formulated with charcoal contents of 0, 0.5, 1.0, 1.5, 2.0, 3.0 and 4.0 wt.%. The formulated components of each sample were mixed thoroughly using a reversing drum mixer in which the entire drum rotated around its axis at a rotation speed of 150 rpm. The materials were charged and discharged through a charge chute at one end of the drum with the addition of steel balls, which aided in the mixing process, and then the drum was rotated at the predetermined speed for 4 h. Then the mixtures were moulded into cylindrical briquettes (30 mm in diameter and 30 mm in height) using a Laptuls hydraulic press at 5 MPa pressure to ensure homogeneous sintering of the final resulting sinters (ElDeeb et al., Reference ElDeeb, Brichkin, Kurtenkov and Bormotov2019).
To determine the optimum effective charcoal content in terms of the sintering and leaching characteristics, the seven formulated briquettes were sintered in a closed system in a PVK-1.6-5 high-temperature chamber furnace (TEPLOPRIBOR) with a heating rate of 10°С min–1 up to the highest temperature of 1360°С. The largest amount of charcoal added was 4% because the addition of more than 4% had a negative effect on the APR. This may be attributed to the release of excessive heat for large charcoal contents, which leads to the formation of an undesirable stable mullite phase (Al2O3.SiO2), from which Al2O3 is only extracted with difficulty. To examine the effects of the optimum charcoal content (i.e. 1.5%, which produced the greatest APR) at various sintering temperatures, six replicated briquettes with 1.5 wt.% charcoal contents were heated to various final sintering temperatures of 1260°C, 1280°C, 1300°C, 1320°C, 1340°C and 1360°С.
For all of the sintered briquettes, the soaking time was 1 h. Subsequently, the sinters were annealed in the furnace by cooling them to room temperature at a rate of 10°С min–1 to achieve the self-disintegration process (Pontikes et al., Reference Pontikes, Jones, Geysen and Blanpain2010; ElDeeb et al., Reference ElDeeb, Brichkin, Bertau, Savinova and Kurtenkov2020a). Chromatic changes, which were considered as a proxy, were determined on the surfaces of all of the briquettes to monitor sintering homogeneity.
Alumina-leaching process
All of the sintered briquettes were subjected to leaching with sodium carbonate solutions. The leaching process takes place according to the dissociation reaction mechanisms shown in Equations 1 and 2.


The leaching process was carried out in parallel mode in a HEL Auto-Mate II reactor system equipped with a mechanical stirrer. The liquid solution in the reactor was maintained at atmospheric pressure conditions by connecting the reflux condensers to the reaction volume to return the condensate. Stirring was carried out using a stirrer with a magnetic drive in the working zone of each reactor. The speed of rotation of the mixer varied from 250 to 1500 rpm. Temperature control was achieved using sensors installed in the reaction medium and in the jacket of each reactor. To maintain the desired temperature, each thermostatic cell was equipped with an independent heating element, and cooling was achieved by supplying a coolant via circulating thermostat. The operating temperature range of the system was 20–160°C ± 0.1°С. Following the procedure described by ElDeeb et al. (Reference ElDeeb, Brichkin, Bertau, Savinova and Kurtenkov2020a), each self-disintegrated sinter powder was stirred for 15 min in a fresh Na2CO3 solution with a concentration of 120 g L–1 (1:5 solid:liquid ratio) at 70°C and 600 rpm, which yielded a suspended slurry. The pulp was filtered with a vacuum pump, producing a sludge that was washed with hot distilled water and dried at 110°C. Based on the changes in the chemical compositions of the precursor sinters and their resulting sludges, as observed from the X-ray fluorescence (XRF) data, the APR was calculated according to Equation 3:

Three replicate measurements/experiments were conducted for each condition and the average was taken with the calculated standard deviation (SD) of ±2% (Tables 1 & 2).
Table 1. Effects of the variable amounts of charcoal added on the APR of the kaolin-limestone-charcoal mixtures sintered at 1360°C.

Table 2. Effects of the variable sintering temperatures on the APR with the addition of 1.5% charcoal.

Characterization methods
To investigate the thermal changes during the decomposition of the kaolin-limestone and kaolin-limestone-charcoal mixtures, thermogravimetric analysis (TGA) and differential scanning calorimetry (DSC) were performed with a simultaneous DSC-TGA instrument (SDT Q600, TA Instruments, USA) in the range 25–1300°C, with a heating rate of 20°C min–1, under vacuum and using a platinum crucible. The mineralogical changes in the sinters and sludges were detected using X-ray diffraction (XRD) with a Bruker D8 focus X-ray diffractometer, with Cu-Kα radiation (40 kV, 30 mA, λ = 1.5406 Å) in the range 10–60°2θ, using a scanning step of 0.008°2θ and a counting time of 10 s step–1. The chemical changes in the sinters and sludges were determined using XRF with a sequential XRF spectrometer (XRF-1800, 40 kV, 90 mA, Re anode, Shimadzu, USA). Microcompositional and microstructural changes in the transformed phases were investigated using scanning electron microscopy (SEM; Tescan TS 5130MM) with a microscope equipped with an energy-dispersive X-ray (EDX) detector (active crystal area = 50 mm2; Oxford Instruments, UK) and an INCA Energy microanalysis system and YAG crystal as the back-scattered electron detector. Particle-size analyses were performed on the powders of the sinters and sludges using laser diffraction with a domestic Microsizer 201C analyser (InTechSA Ltd, Russia) in the size range of 0.2–600 μm.
Results and discussion
Effects of charcoal addition on thermal behaviour
Based on the TGA/DSC curves of the kaolin-limestone mixture (Fig. 1a), as well as on their previously examined thermal characteristics during the phase transformations of the precursor materials in this sintered mixture (Drits et al., Reference Drits, Sakharov, Dorzhieva, Zviagina and Lindgreen2019; Húlan et al., Reference Húlan, Štubňa, Shishkin, Ozolins, Csáki, Bačík and Fridrichová2019; Karbalaei Saleh et al., Reference Karbalaei Saleh, Abdollahi, Noaparast and Fallah Nosratabad2019; Chalouati et al., Reference Chalouati, Bennour, Mannai and Srasra2020; ElDeeb et al., Reference ElDeeb, Brichkin, Bertau, Savinova and Kurtenkov2020a), three main significant regions of the well-defined weight losses on the TGA curve were considered as the initial (or datum) state for monitoring the thermal changes (i.e. before the addition of charcoal). The AB region occurs at temperatures <200°C, the BC region occurs at 450–650°С and the CD region occurs within the 650–850°C range. On the DSC curve, the first endothermic peak at 111.2°C (corresponding to the AB region) is attributed to the loss of adsorbed water. The second endothermic peak at 507.5°С (corresponding to the BC region with weight loss of 3.27 wt.%) is attributed to the dehydroxylation of kaolinite and its transformation into the highly reactive metakaolinite (Al2Si2O7) phase, which facilitated Al2O3 extraction in the leaching stage. The third endothermic peak at 844.4°C (corresponding to the CD region with weight loss of 29.69 wt.%) is due to the complete decomposition of calcite in the limestone fraction to the reactive lime (CaO) phase. The sharp exothermic peak at 975.5°С corresponds to the transformation of metakaolinite into the Al–Si spinel phase (and/or a mixture of γ-alumina, amorphous silica and mullite).

Fig. 1. TGA and DSC curves of limestone-kaolin mixtures with various amounts of charcoal: (a) 0%, (b) 1% and (c) 4%. The regions of well-defined weight losses on the TGA curve were as follows: the AB region appeared at temperatures <200°C; the BC region emerged at temperatures >450°С; and the CD region existed over the range 650–850°C.
The TGA and DSC curves (Fig. 1b,c) indicate the thermal changes accompanied by the additions of charcoal to the kaolin-limestone mixture of 1% and 4%, respectively. After the addition of charcoal to the mixtures, the temperatures of the phase transformations decreased. At 1% charcoal content (Fig. 1b), the DSC endothermic peak of the kaolinite dehydroxylation enthalpy appeared at 494.9°С and that of the complete limestone decomposition in the mixture appeared at 821.2°C. The sharp DSC exothermic peak at 969.6°С indicates the transformation of metakaolinite to the Al-Si spinel (and/or a mixture of γ-alumina, amorphous silica and mullite). At 1% charcoal content (Fig. 1c), the dehydroxylation temperature of kaolinite decreased from 507.5°C to 494.8°C, the temperature limit of the complete limestone decomposition fell from 844.4°C to 811.0°C and the temperature of the transformation of metakaolinite to Al-Si spinel decreased from 975.5°C to 967.3°C. Increasing the charcoal content from 1% to 4% did not lead to significant changes in the thermal behaviour.
Thermodynamically, the thermal changes accompanied by the phase transformations are mainly controlled by the partial pressure of both the water vapour (adsorbed and hydroxyl water in kaolinite) and the CO2 emitted (from the complete decomposition of calcite). Hence, the excessive pressure may reduce the transformation temperatures with increasing amounts of charcoal, as indicated in Equations 4–7 (Zhou et al., Reference Zhou, Liu, Yan, Fang and Wang2012; Yuan et al., Reference Yuan, Han, Li, Gao and Yu2018; ElDeeb et al., Reference ElDeeb, Brichkin, Povarov and Kurtenkov2020b).




In addition, a sharp DSC exothermic peak appeared at 1144.9°С (Fig. 1c), corresponding to the transformation of Al-Si spinel into the dicalcium silicate phase (2CaO.SiO2) according to Equation 8.

Increasing the charcoal content facilitated the formation of the dicalcium silicate phase (2CaO.SiO2) at a lower temperature (<1200°C). Hence, the added charcoal acted as a fluxing agent and a thermal activator (as indicated by the TGA and DSC analyses) because it accelerated both the dehydroxylation of kaolinite and the decomposition of calcium carbonate and hence accelerated the reaction between the resulting lime and metakaolinite to produce the desired leachable calcium aluminate phase (C12A7).
Effects of charcoal addition on the phase transformation and microstructure
The phase transformation changes of the sintered kaolin-limestone mixtures at the highest optimum temperature, 1360°C and with variable charcoal contents as indicated by the XRD traces (ElDeeb et al., Reference ElDeeb, Brichkin, Bertau, Savinova and Kurtenkov2020a) are shown in Fig. 2. In all of the traces, the γ-C2S phase was identified by the peaks at 29.63 and 47.53°2θ (Jadhav & Debnath, Reference Jadhav and Debnath2011). In the charcoal-free sample, the crystalline calcium aluminate phase (Ca12Al14O33) was identified from the peaks at 14.70, 22.50 and 23.22°2θ (Zhang et al., Reference Zhang, Ou, Qiang, Niu and Komarneni2015a) and the crystalline aluminosilicate phase (Al2SiO5) was identified from the peaks at 12.40°2θ, 19.50°2θ and 26.66°2θ (ElDeeb et al., Reference ElDeeb, Brichkin, Povarov and Kurtenkov2020b). In samples with added charcoal (1–4%), under the same sintering conditions, the aluminosilicate and calcium aluminate phases disappeared as they transformed into amorphous phases (Fig. 2). The resulting amorphous calcium aluminate phase is a highly desirable and effective component causing significant Al2O3 leachability and therefore improved APR (ElDeeb et al., Reference ElDeeb, Brichkin, Bertau, Savinova and Kurtenkov2020a). In addition, the predominance of a crystalline dicalcium silicate phase increased the efficiency of the self-integration process in all of the resulting charcoal-activated sinters. Hence, the targeted thermochemical amorphization by the addition of charcoal yielded greater chemical reactivity and more efficient leachability in the dilute alkaline solutions than sintering without the addition of charcoal (Liew et al., Reference Liew, Kamarudin, Mustafa Al Bakri, Luqman, Khairul Nizar, Ruzaidi and Heah2012; Zhou et al., Reference Zhou, Liu, Yan, Fang and Wang2012; Li et al., Reference Li, Hui, Wang, Bao and Sun2014b; Xu et al., Reference Xu, Lao, Wu, Zhang, Xu and Li2015; D'Elia et al., Reference D'Elia, Pinto, Eramo, Giannossa, Ventruti and Laviano2018; Yuan et al., Reference Yuan, Han, Li, Gao and Yu2018; ElDeeb et al., Reference ElDeeb, Brichkin, Kurtenkov and Bormotov2019, Reference ElDeeb, Brichkin, Bertau, Savinova and Kurtenkov2020a, Reference ElDeeb, Brichkin, Povarov and Kurtenkov2020b). Moreover, the addition of charcoal had a significant effect on the surface properties and degree of disorder of the sintered components, which facilitated their transformations into the final amorphous material (Yuan et al., Reference Yuan, Han, Li, Gao and Yu2018).

Fig. 2. XRD traces showing phase transformations in the sintered limestone-kaolin mixtures with variable amounts of charcoal (0–4%) at the optimum temperature of 1360°C.
The abundance of the resulting crystalline calcium silicates (and hence the extent of their self-disintegration) increased with increasing sintering temperature; hence, the frequency of the separate finer particles in the resulting loose calcium aluminate fraction increased significantly (ElDeeb et al., Reference ElDeeb, Brichkin, Bertau, Savinova and Kurtenkov2020a). Figure 3 shows the general microtextural and micromorphological changes in the resulting sinters in the temperature range 1260–1360°C with the addition of the optimum 1.5% charcoal content. Normally, the sizes of the self-disintegrated particles decrease with increasing sintering temperature (ElDeeb et al., Reference ElDeeb, Brichkin, Bertau, Savinova and Kurtenkov2020a); hence, the resulting sinters under the high-temperature limits of 1340°C and 1360°C consisted of finer calcium aluminate particles that aggregated as a groundmass matrix (mainly particle sizes <10 μm; Fig. 3c,d) than those produced under lower temperatures of 1260°C and 1300°C (with particle sizes >50 μm and up to 1 mm; Fig. 3a,b).

Fig. 3. Back-scattered electron images of the sinters produced at (a) 1260°C, (b) 1300°C, (c) 1340°C and (d) 1360°C with the addition of 1.5% charcoal.
Moreover, under a relatively low temperature (1260°C), with the addition of 1.5% charcoal, a small amount of non-reactive relict crystals composed of the precursor kaolinite and calcite components as well as secondary SiO2 and Al2O3 remained in the sinter (Fig. 4a). As the temperature increased to 1360°C, the abundance of these relicts decreased significantly (Fig. 4b) due to kaolinite dehydroxylation and limestone decomposition and their transformation into the highly reactive metakaolinite and lime phases. Then, the highly self-disintegrated crystalline calcium silicate and the easily leachable amorphous calcium aluminate phases were formed, which were effective at increasing the magnitude of the APR. Therefore, a high sintering temperature in the presence of charcoal led to a combination of favourable phase changes with desirable micrometric characteristics in the resulting sinter that effectively increased the APR.

Fig. 4. Back-scattered electron images showing the microstructural characteristics of the sinters produced at (a) 1260°C and (b) 1360°C with the addition of 1.5% charcoal. 1 = calcium aluminates; 2 = calcium silicates; 3 = relicts of kaolin/SiO2; 4 = free CaO; 5 = structurally non-free CaO.
Figure 5 shows the distributions of Si and Al atoms within a typical multiphase particle in the resulting sinter at 1360°C with the addition of 1.5% charcoal. The calcium aluminate phase was mainly concentrated in the inner zone of the particle surrounded by finer aggregates of the calcium silicate and aluminosilicate phases. After leaching of the highest-temperature sinter (1360°C with 1.5% charcoal), the calcium aluminate phase was concentrated mainly in the inner zones (i.e. the core) of the resulting multiphase sludge particles. In some particles, the calcium aluminate phase was surrounded by the non-leachable silicate and aluminosilicate phases that existed as finer aggregates in the peripheral zones (i.e. the crust; Fig. 6). Moreover, in some other particles, the aluminate phase (i.e. the large, light grey areas) was covered by dense carbonate masses (i.e. the dark grey rim) that precipitated during the leaching process (Fig. 6b,c). The diffused crystalline calcium silicate crust that covered the sludge particles probably acted as a barrier, affecting the complete dissociation of the Al2O3 (i.e. 100% APR) from the aluminate phases in the sludge during leaching (ElDeeb et al., Reference ElDeeb, Brichkin, Bertau, Savinova and Kurtenkov2020a).

Fig. 5. (a) Back-scattered electron image showing a typical multiphase particle of the sinter produced at 1360°C with 1.5% added charcoal. 1 = calcium aluminate phases; 2 = calcium silicate and aluminosilicate phases. (b) Elemental modal map showing the distributions of Al and Si on a typical multiphase particle of the sinter produced at 1360°C.
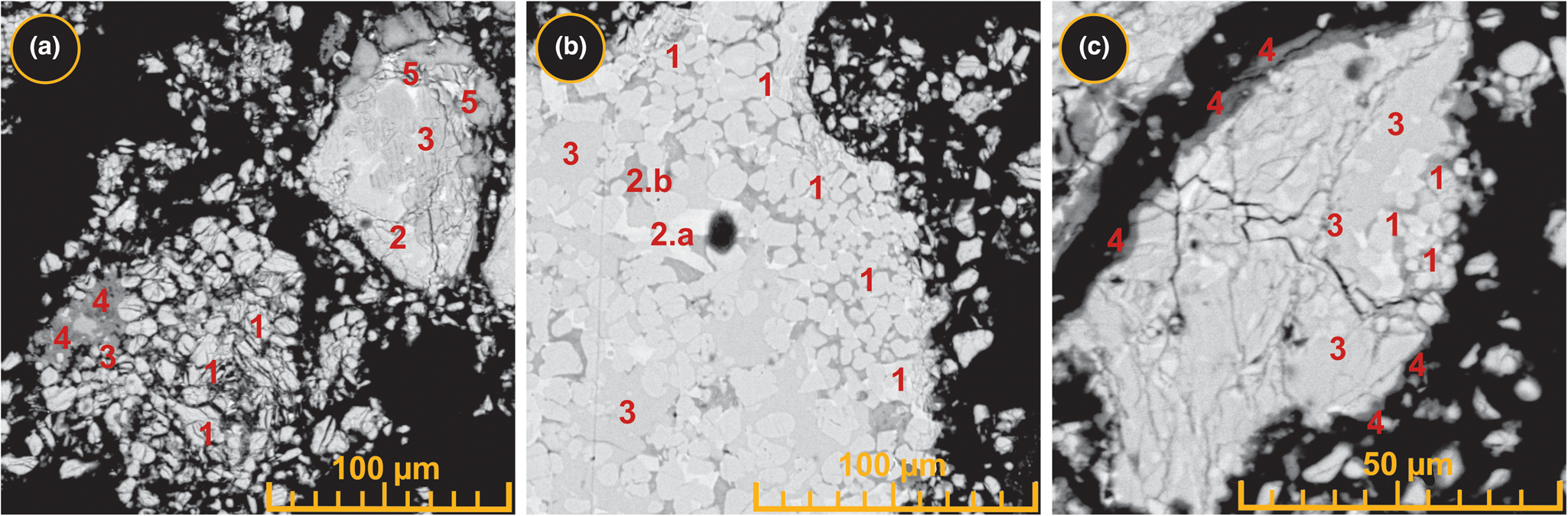
Fig. 6. Back-scattered electron images showing the microstructural characteristics of the sludge resulting from the leaching process of the sinter produced at 1360°C with the addition of 1.5% charcoal. (a) Morphology of leached self-disintegrated particles in the sludge sample. (b) The distribution of calcium silicates within the microtexture of the leached sludge particles. (c) Calcium carbonate deposition on the outer peripheries of the deformed (cracked) sludge particles after leaching. 1 = calcium silicates; 2.a = aluminosilicate type I, 2.b = aluminosilicate type II; 3 = calcium aluminates; 4 = calcium carbonate; 5 = calcium oxide.
In the microstructure, the transformed amorphous and crystalline multiphase components in both the sinter (produced at 1360°C with 1.5% charcoal) and its related sludge can be distinguished from their average EDX microchemical compositions (Table 3). The transformed components in the resulting charcoal-activated sinter at 1360°C (Figs 2, 4b & 5) were distinguished into five phases: the calcium aluminate type (I), the calcium aluminate type (II), the aluminosilicate type (I), the aluminosilicate type (II) and the dicalcium silicate. Despite their absence from the XRD traces (Fig. 2), the two types of amorphous calcium aluminates (I and II) were confirmed by the greatest average Al contents of 17.7–24.2% with relatively high Ca contents of 36.3–43.9% and the smallest average Si contents of 0.3–1.4%. In addition, they contained Na ≤0.2%, K ≤0.3%, Mg contents ≤0.4% and Fe ≤1.2% on average. The amorphous aluminosilicate phases (I and II) showed average Al contents of 12.5–18.1%, Si contents of 2.3–14.3% and lower average Ca contents (28.0–30.0%) than the amorphous calcium aluminates. Moreover, they had the greatest average Mg contents (1.4–9.6%), average Fe contents up to 1.5% and Na and K contents up to 0.8%. The crystalline C2S phase had the smallest Al contents among all the five phases, with an average of 0.5%, but it exhibited the greatest average Ca and Si contents of 46.8% and 15.6%, respectively. In addition, it had the smallest average contents of both Mg and Fe that did not exceed 0.1% and was free of alkali metals (Na and K). However, the chemical composition of the sludge was similar to its precursor sinter, which also reflected the same multiphase components of the amorphous aluminosilicate and calcium aluminate phases as well as the crystalline C2S phase (Table 3).
Table 3. Elemental composition from the EDX analysis (n = 10) of the sinter produced at 1360°C with 1.5% added charcoal and its sludge produced by the leaching process.

The small SiO2 contents (≤2%) of the leachable calcium aluminate phases in the sinter reflect the high sintering quality that led to greater alumina leachability from the sludge during the hydrometallurgical processing (Mejía De Gutiérrez et al., Reference Mejía De Gutiérrez, Torres, Vizcayno and Castello2008; Azof et al., Reference Azof, Yang, Panias, Kolbeinsen and Safarian2019, Reference Azof, Vafeias, Panias and Safarian2020). In the studied sinters, the leachable calcium aluminate phases I and II had small SiO2 contents (≤1.5%; Table 3); hence, the residual calcium aluminates in the resulting sludge had small Al contents (18.1%; Table 3). The small Al contents in the resulting sludge indicate an increased extent of Al dissociation, resulting in a high APR. In addition, the Al-containing phases did not completely release the total Al2O3 content during the leaching process because of the significant Si contents (>2%) in the aluminosilicates (i.e. up to 14.3%; Table 3).
Effects of charcoal thermochemical activation on self-disintegration efficiency
The particle-size characteristics of the sinter are key factors in the leaching process during Al2O3 extraction from the sintered kaolin-limestone mixture. The finer the particle size of the sinter powder, the greater the leaching rate of Al2O3 and hence the greater the resulting APR (ElDeeb et al., Reference ElDeeb, Brichkin, Bertau, Savinova and Kurtenkov2020a). Particle self-disintegration via the sintering of kaolin-limestone mixtures at <1360°C was the most important process for the intrinsic size reduction in the resulting sinter powders, and hence it is considered to be a cost-effective and energy-efficient factor to help avoid pre-leach grinding. The self-disintegration process normally takes place due to the formation of the crystalline β-C2S (2CaO⋅SiO2) under high temperatures and then its transformation into the γ phase (Fig. 2) during the cooling of the sintered mixture according to Equations 9 & 10 (ElDeeb et al., Reference ElDeeb, Brichkin, Bertau, Savinova and Kurtenkov2020a).


The self-disintegration process of sintered kaolin-limestone mixture without addition of charcoal was initiated at high temperatures of 1300–1400°С (ElDeeb et al., Reference ElDeeb, Brichkin, Kurtenkov and Bormotov2019, Reference ElDeeb, Brichkin, Bertau, Savinova and Kurtenkov2020a). Charcoal was seen to be a thermal activator even in small amounts (0.5%) as self-disintegration was effectively initiated at 1260°С. With the addition of charcoal at the optimum content of 1.5%, the resulting sinters showed a significant size reduction with increasing sintering temperature from 1260 to 1360°C (Fig. 7a,b & Table 4). The finest particle sizes were observed in the sinter powder produced at 1340°C (median D 50 = 9.7 μm), while the lowest sintering temperature of 1260°С produced a powder with of D 50 = 31 μm. The amounts of the finest fractions in the self-disintegrated particles (<1 μm) of the sinters showed a strong positive correlation with sintering temperature (R 2 = 0.93; Table 4). The <1 μm fractions increased from 0.49% (sintering at the lowest temperature of 1260°C) to 0.63% (sinters produced at the highest temperature of 1360°C). The sinter produced at 1340°C showed a unimodal distribution, while the particle-size distributions of the remaining sinters were bimodal (Fig. 7a). The specific parameters of the particle-size homogeneity (span = (D 90 – D 10)/D 50), the uniformity coefficient (C u = D 60/D 10) and the gradation curvature coefficient (C c = D 302/(D 60D 10)) were calculated (Table 4) (Awad et al., Reference Awad, López-Galindo, Sánchez-Espejo, El-Rahmany and Viseras2018a, Reference Awad, López-Galindo, Medarević, Đuriš, El-Rahmany, Ibrić and Viseras2020). There was no significant correlation between sintering temperature and the particle-size homogeneity of any of the sinters, as the size span values ranged from 2.40 (in the sinter produced under 1260°С) to 4.39 (in the sinter produced under 1300°С), with an average value of 3.33. Sintering temperature showed a strong positive correlation (R 2 = 0.93) with the curvature coefficient (C c) and a significant negative correlation (R 2 = –0.75) with the uniformity coefficient (C u). The C c values being >1 indicated that the sinters produced at 1320–1360°С consisted of well-graded particles, while the sinters produced at temperatures of ≤1300°С consisted of poorly graded particles with C c values of <1 (Awad et al., Reference Awad, López-Galindo, Sánchez-Espejo, El-Rahmany and Viseras2018a). Despite the finer particle size of the precursor sinter produced at 1340°С, the resulting related sludge had a larger particle size with D 50 = 17 μm (Fig. 7c,d). This can be attributed to the precipitation of CaCO3 onto the surfaces of the residual non-leachable components. The secondary agglomeration of the fine CaCO3 particles was the most plausible mechanism to explain the particle-size enlargement when compared to the coarser CaCO3 particles that formed via primary crystal growth (Azof & Safarian, Reference Azof and Safarian2020; Azof et al., Reference Azof, Yang, Panias, Kolbeinsen and Safarian2019, Reference Azof, Vafeias, Panias and Safarian2020; ElDeeb et al., Reference ElDeeb, Brichkin, Bertau, Savinova and Kurtenkov2020a).

Fig. 7. Effects of sintering temperature within the range 1260–1360°C on the particle-size distribution with the addition of 1.5% charcoal: (a) frequency curves and (b) cumulative curves of the sinters; (c) frequency curves and (d) cumulative curves of the related sludges obtained after the leaching process.
Table 4. Particle-size distributions (n = 3) of the sintered kaolin-limestone mixtures under variable temperatures within the range 1260–1360°C with the addition of 1.5% charcoal (SD = ±2).

Using 1360°С as the optimum sintering temperature, charcoal contents of 0.5–4.0% (Fig. 8 & Table 5) showed significant stability in terms of the improved self-disintegration efficiency of the resulting sinters compared to sintering at 1360°С with 1.5% charcoal (Table 5). This is indicated by the median D 50 values that ranged between 8.9 μm (1% charcoal content) and 10.6 μm (0.5% charcoal content), with an average of 10 μm. The fine fractions (<1 μm) ranged between 0.55% and 0.80% (1% charcoal content), with an average of 0.59%. In addition, the size span values ranged between 2.1 and 3.8, with an average of 2.9, and the C c values ranged between 1.2 and 1.4, with an average of 1.3 (Table 5).

Fig. 8. Effects of added charcoal percentage (0.5–4.0%) on the particle-size distribution at a fixed sintering at 1360°C: (a) frequency curves and (b) cumulative curves of the sinters; (c) frequency curves and (d) cumulative curves of the related sludges obtained after the leaching process.
Table 5. Particle-size distributions (n = 3) of the sintered kaolin-limestone mixtures under variable amounts of additional charcoal (0–4%) and a sintering temperature of 1360°C (SD = ±2).

Effects of charcoal thermochemical activation on APR
As the optimum sintering temperature to produce the greatest APR was 1360°C (ElDeeb et al., Reference ElDeeb, Brichkin, Kurtenkov and Bormotov2019, Reference ElDeeb, Brichkin, Bertau, Savinova and Kurtenkov2020a), the effects of the varied amounts of added charcoal in the kaolin-limestone mixture on the APR were examined at that temperature. By increasing the amount of charcoal added from 0.5% to the optimum 1.5%, the APR increased gradually from 77.7% to 87.4% (Fig. 9). With further addition of charcoal, up to 4%, the APR gradually decreased from 87.4% to 75.6%. This is attributed to the release of excessive heat by the larger amounts of charcoal, which led to the formation of mullite, from which Al2O3 is leached with difficulty.
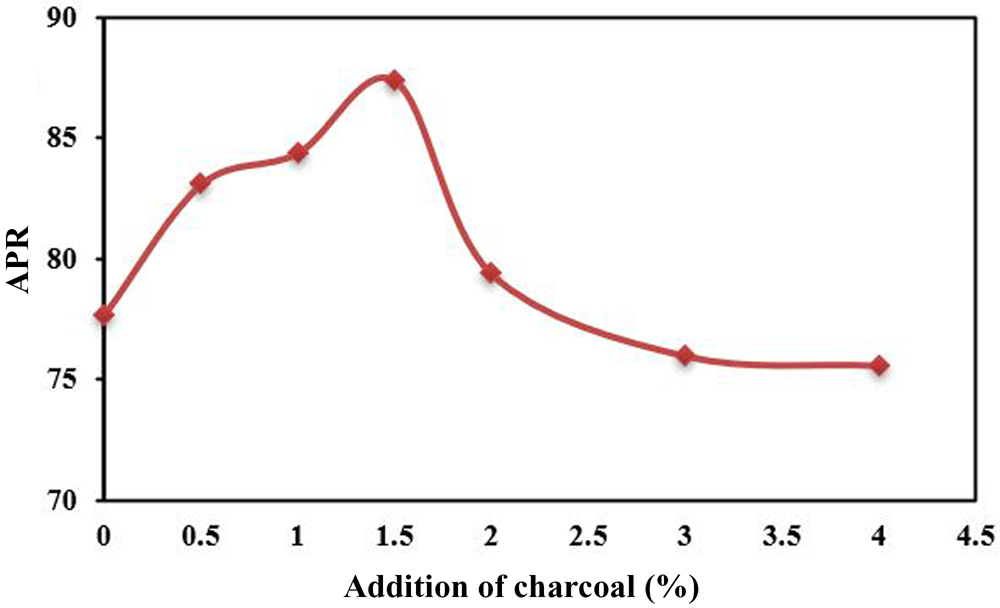
Fig. 9. Effects of the variable amounts of charcoal added (0–4%) on the APR of kaolin-limestone-charcoal mixtures sintered at 1360°C.
Sintering temperature was the main factor controlling the phase transformations and microstructural changes that drove the self-disintegration process and hence significantly increased the APR (ElDeeb et al., Reference ElDeeb, Brichkin, Kurtenkov and Bormotov2019, Reference ElDeeb, Brichkin, Povarov and Kurtenkov2020b). At the same optimum amount of charcoal added, 1.5%, the resulting APR values were strongly correlated with sintering temperature (R 2 = 0.94), as the APR values increased gradually from 44.4% for sintering at 1260°С to 87.4% for sintering at 1360°С (Fig. 10a). As sintering temperature had a significant effect on the particle-size distribution (Fig. 7 & Table 4), the resulting APR showed a strong positive correlation (R 2 = 0.96) with the curvature coefficient, C c (Fig. 10b). The APR showed a positive correlation (R 2 = 0.83) with the fine fraction (<1 μm) contents (Fig. 10c) and a negative correlation (R 2 = –0.79) with the uniformity coefficient, C u (Fig. 10d). Thus, a sintering temperature of 1360°С and the addition of 1.5% charcoal were the optimum conditions for the formation of highly leachable amorphous calcium aluminate (C12A7) according to Equations 11 & 12. In addition, crystalline C2S was the most efficient self-disintegration controlling phase in the resulting sinters, as is indicated by the increase in the particle fine fraction contents and the influence on the particle-size gradation. Sintering at a lower temperature (1260°С) was insufficient for complete formation of the C12A7 and C2S phases.



Fig. 10. Effects of the variable sintering temperatures (1260–1360°C) and the size-distribution parameter on the APR with the addition of 1.5% charcoal: (a) the effect of sintering temperature on the APR; (b) correlation between the APR and size-curvature coefficient, C c; (c) correlation between the APR and fine fraction (<1 μm); and (d) correlation between the APR and size uniformity coefficient, C u.
In the case of sintering at 1360°C without added charcoal, the precursor components reacted and transformed completely into the leachable calcium aluminate phase (C12A7). The additional heat generated under these conditions facilitated the crystallization of the calcium aluminate phase (ElDeeb et al., Reference ElDeeb, Brichkin, Kurtenkov and Bormotov2019, Reference ElDeeb, Brichkin, Povarov and Kurtenkov2020b, Reference ElDeeb, Brichkin, Sizyakov, Kurtenkov and Litvinenko2020c, Reference ElDeeb, Brichkin, Kurtenkov and Bormotov2021). The addition of charcoal up to 1.5% increased total heat during the transformation due to the combustion of charcoal in this closed system (as is indicated by the significant thermal changes on the DSC curves; Fig. 1). These conditions caused amorphization of the calcium aluminate phase (cf. Figs 2 & 5), yielding fine self-disintegrated particles and surface properties, which led to enhanced leachability and greater Al2O3 production. However, the decreasing APR with charcoal contents >1.5% is attributed to the release of an excessive heat, producing mullite, from which alumina is extracted with difficulty (Qiao et al., Reference Qiao, Si and Yu2008; ElDeeb et al., Reference ElDeeb, Brichkin, Povarov and Kurtenkov2020b).
Therefore, the charcoal content of 1.5% was optimal for sintering at 1360°C to produce the greatest APR. The main advantages of using charcoal instead of other inorganic fluxing materials are the chemical inertness of carbon (i.e. it does not react with the lime and metakaolinite) and the complete loss of the added charcoal mass on ignition. Other known fluxing agents are highly reactive materials (even when added in trace amounts) with the transformed aluminosilicate and lime phases, leading to undesirable intermediate products that decrease alumina leachability and reduce the APR (Pontikes et al., Reference Pontikes, Jones, Geysen and Blanpain2010; Wang et al., Reference Wang, Sun, Guo and Zhang2011, Reference Wang, Chu, Hao, Rong and Sun2017; Yu et al., Reference Yu, Pan, Wang, Zhang, Sun and Bi2012, Reference Yu, Pan, Liu, Wang and Bi2014, Reference Yu, Pan, Dong and Wu2019). The recommended flow diagram for the pyro-hydrometallurgical processing of kaolin ore to produce alumina using the lime-sintering process with the addition of charcoal is shown in Fig. 11.
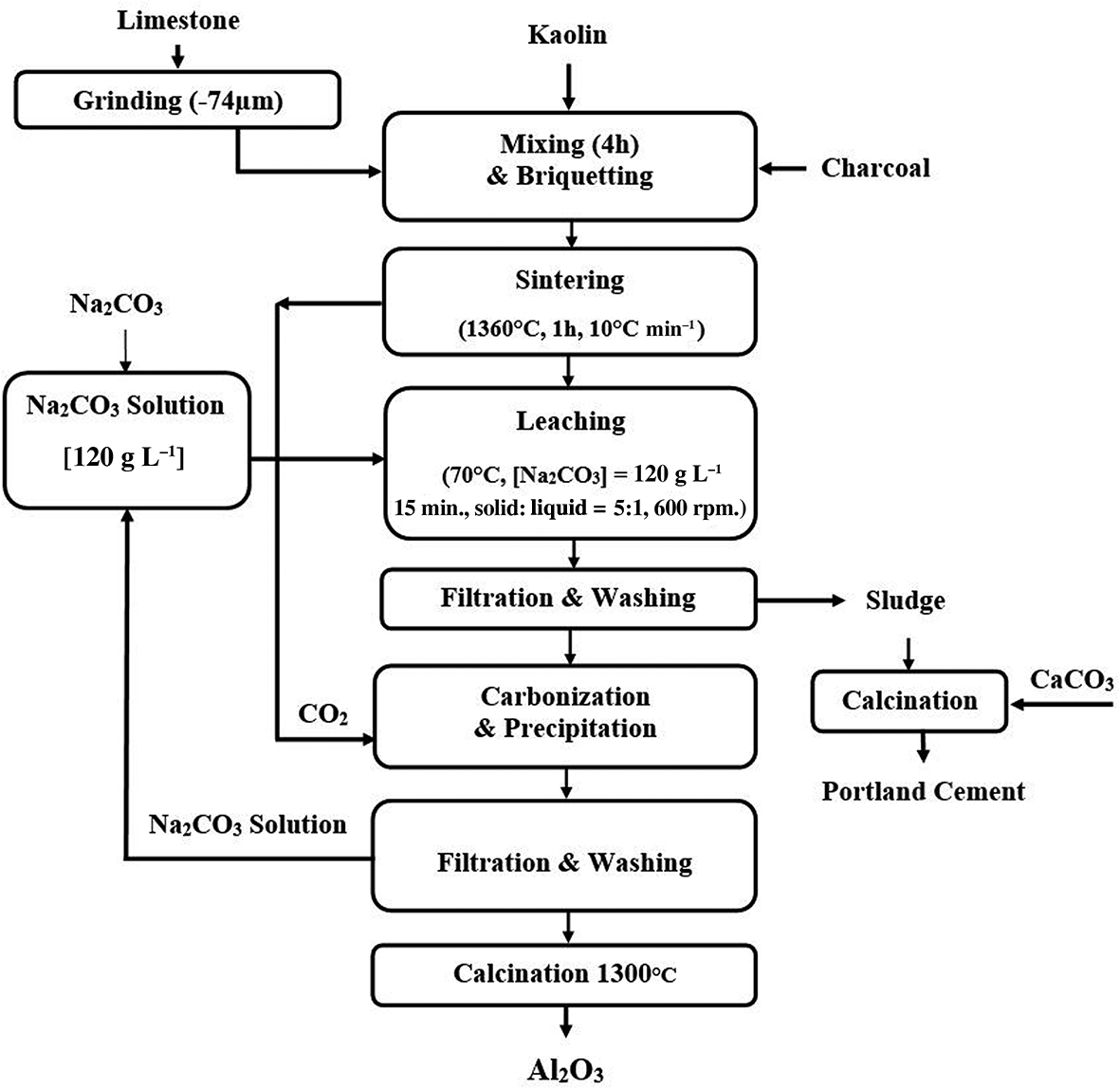
Fig. 11. The proposed flow diagram for the pyro-hydrometallurgical processing of kaolin ore using the lime-sintering process for Al2O3 extraction.
Summary and conclusions
Thermochemical activation of kaolin-limestone feeds (e.g. low-grade, non-bauxitic, hydrous, aluminium silicate-rich raw geomaterials) via the addition of charcoal is an important process for increasing the APR during pyro-hydrometallurgical processing via the lime-sintering process. The present study determined the optimum conditions for this charcoal-based activation and explained the related phase-transformation mechanisms that control the cost-effectiveness and energy efficiency of Al2O3 production and of increasing the APR. The study investigated the thermal activation effects of the charcoal on the efficiency of Al2O3 extraction from a processed kaolin in the sintering temperature range of 1260–1360°C. The charcoal added to the kaolin-limestone mixture was 0.5–4.0 wt.%. In comparison to relevant previous work by the same authors, the addition of 1.5% charcoal for sintering at 1360°C yielded the maximum APR of 87.4% under the same leaching conditions. Sintering at 1360°C and the addition of ≤1.5% charcoal were the optimum conditions for amorphization of the resulting highly leachable calcium aluminate phase. In addition, the high self-disintegration efficiency explained the high Al2O3 leachability of the resulting sinters and therefore the increased APR. Sintering at higher temperatures (˃1360°C) and/or with the addition of greater charcoal contents (˃4%) produced excessive heat and yielded mullite, from which alumina is leached with difficulty, thereby significantly decreasing the APR. Unlike other inorganic fluxing and activation agents, charcoal is a promising activator for Al2O3 production from low-grade raw geomaterials due to its effectiveness at increasing the APR and the stability of its self-disintegration process at lower sintering temperatures, even with the smallest addition of charcoal.
Supplementary material
To view supplementary material for this article, please visit https://doi.org/10.1180/clm.2022.7.
Financial support
The work was carried out with the financial support of the Russian Science Foundation under Agreement No. 18-19-00577 of 28 April 2021 of a grant for fundamental scientific research and exploratory scientific research.