Introduction
The interaction of lasers with solid materials has been and continues to be an important topic in many areas of research (von der Linde and Sokolowski-Tinten, Reference von der Linde and Sokolowski-Tinten2000; Gamaly et al., Reference Gamaly, Rode, Luther-Davies and Tikhonchuk2002; Nedialkov et al., Reference Nedialkov, Imamov, Atanasov, Heusel, Breitling, Ruf, Hügel, Dausinger and Berger2004; Burakov et al., Reference Burakov, Bulgakova, Stoian, Rosenfeld and Hertel2005; Ion, Reference Ion2005; Brown and Arnold, Reference Brown, Arnold, Sugioka, Meunier and Piqué2010; Bäuerle, Reference Bäuerle2011; Shaheen and Fryer, Reference Shaheen and Fryer2012; Balling and Schou, Reference Balling and Schou2013; Ganeev, Reference Ganeev2014; Stafe et al., Reference Stafe, Marcu, Puscas, Ertl, Lüth and Mills2014; Shaheen et al., Reference Shaheen, Gagnon and Fryer2015a, Reference Shaheen, Gagnon and Fryer2016). Understanding the nature of these interactions is essential for selecting and matching a laser beam of specific properties to a particular application in order to achieve the desired outcomes. A comprehensive study of laser interactions with solids is not easy because laser–solid interactions involve many processes and many interfering parameters. In addition to the direct laser–solid interactions, plasma formation and expansion, as well as its subsequent interactions with the incident laser beam, increase the complexity of these processes (Bäuerle, Reference Bäuerle2011; Stafe et al., Reference Stafe, Marcu, Puscas, Ertl, Lüth and Mills2014; Shaheen et al., Reference Shaheen, Gagnon and Fryer2015b). A large number of parameters should be considered when investigating the interaction of lasers with different solid materials. Laser properties, such as fluence, pulse width, repetition rate, beam profile, number of laser pulses, and wavelength, are important parameters of a laser beam that controls the interaction processes (Hashida et al., Reference Hashida, Semerok, Gobert, Petite, Izawa and Wagner2002; Le Harzic et al., Reference Le Harzic, Breitling, Weikert, Sommer, Fohl, Valette, Donnet, Audouard and Dausinger2005; Bashir et al., Reference Bashir, Rafique, Nathala and Husinsky2013; Jelani et al., Reference Jelani, Bashir, Rehman, Ahamad, Yousaf, Akram, Afzal, Chaudhry, Mahmood, Hayat and Ahmad2013; Akram et al., Reference Akram, Bashir, Hayat, Mahmood, Ahmad and Khaleeq-U-Rahaman2014; Shaheen et al., Reference Shaheen, Gagnon and Fryer2019). Add to this the physicochemical properties of the target material, such as thermal and electrical conductivity, reflectivity, absorption, and dielectric constant. The environment (vacuum or gas, gas type, and properties) in which laser–solid interactions take place is also important and cannot be neglected (Amoruso et al., Reference Amoruso, Ausanio, Barone, Bruzzese, Gragnaniello, Vitiello and Wang2005; Ali et al., Reference Ali, Bashir, Akram and Mahmood2013; Krstulović et al., Reference Krstulović, Shannon, Stefanuik and Fanara2013; Shaheen et al., Reference Shaheen, Gagnon and Fryer2013a, Reference Shaheen, Gagnon and Fryer2014; Dawood et al., Reference Dawood, Bashir, Akram, Hayat, Ahmed, Iqbal and Kazmi2015).
Numerous diagnostic techniques have been applied to study the interactions of lasers with solids (Bäuerle, Reference Bäuerle2011; Balling and Schou, Reference Balling and Schou2013; Stafe et al., Reference Stafe, Marcu, Puscas, Ertl, Lüth and Mills2014). While many techniques have been developed for in situ real-time analysis, the most precise methods for investigating structural changes are those carried out after ablation is complete. Scanning electron microscopy is an important offline diagnostic technique, which can provide useful information about the ablation process. Surface morphology of the ablated structures and the shape of the ablated particles have been widely studied by scanning electron microscopy (Wilder-Smith et al., Reference Wilder-Smith, Lin, Nguyen, Liaw, Arrastia, Lee and Berns1997; Kumar et al., Reference Kumar, George, Singh, Joshi and Nampoori2011; Shaheen et al., Reference Shaheen, Gagnon and Fryer2016). A scanning electron microscope (SEM) provides two common imaging modes: secondary electrons (SE) and backscattered electrons (BSE), depending on the origin of electrons that are used to image the sample. In SE images, the electrons are ejected from the valence band or the conduction band in the sample (Williams and Carter, Reference Williams and Carter2009). These electrons are not associated with a specific atom and therefore they do not give information about the chemical composition of the target material. SE are weak, can only escape from a layer within approximately 2 nm from the sample surface, and consequently can only be used to produce images of the target surface. BSE are more energetic than SE because they originate from the incident electron beam after being reflected or backscattered by the atoms in the interaction volume of the sample. The intensity of the BSE depends on the atomic number of the target material and therefore BSE can be used to detect changes in contrast between areas of different chemical composition (Williams and Carter, Reference Williams and Carter2009).
Sapphire has many important applications in optical systems and semiconductor devices (Cui et al., Reference Cui, Wang, Zhang, Han, Kuang, Tian and Sun2014). It is a relatively hard transparent material that is difficult to process using chemical or mechanical means due to its high chemical stability and hardness (Ashkenasi et al., Reference Ashkenasi, Rosenfeld, Varel, Wahmer and Campbell1997; Horisawa et al., Reference Horisawa, Emura and Yasunaga2004; Qi et al., Reference Qi, Nishii, Yasui, Aoki and Namba2010; Shaheen et al., Reference Shaheen, Gagnon and Fryer2015b). Direct ablation of sapphire or other transparent brittle materials with nanosecond infrared lasers is difficult and cannot produce precise, well-defined micrometer-sized craters because these lasers have relatively low photon energy and poor absorption by highly transparent materials. Application of lasers of high intensity (e.g., ultra-short pulse width lasers) or high photon energy [e.g., ultraviolet (UV) lasers] can improve the absorption and ablation quality of transparent materials (Zhou and Wu, Reference Zhou and Wu2010). Brass alloys are strong, corrosion resistant, conductive, and machinable. They are used in many important applications such as water pipes, heat exchangers, electrical wires, and marine engines. The physical properties of brass are fundamentally different from those of sapphire. This greatly affects the absorption of laser energy, the way of energy dissipation, and the mechanisms of material removal.
In this study, we make use of scanning electron microscopy to explore the nature of picosecond laser interactions with sapphire and brass by investigating the evolution of the surface morphology of craters produced at different laser operating conditions. The investigated laser has a pulse width (110 ps) intermediate between the most commonly used nanosecond and the most expensive femtosecond laser systems which are used in laser ablation applications.
Experimental
Laser ablation experiments were conducted at the University of Windsor, Windsor, Ontario, Canada using a femtosecond laser system that has been previously described in Shaheen et al. (Reference Shaheen, Gagnon and Fryer2013b). All ablation experiments were performed in air under atmospheric pressure. The femtosecond laser system (Quantronix® Integra-C) was designed to emit two laser beams at a wavelength of 785 nm and a repetition rate of 1–1000 Hz. One of the beams is a femtosecond beam with a pulse width of 130 fs, and the other beam is a picosecond beam with a pulse width of 110 ps. Both beams can be used simultaneously, however, in this study the picosecond beam was used exclusively. The energy of the two laser beams can be varied from a few microjoules per pulse to a maximum of 2 mJ per pulse using a built-in half-wave plate and a polarizer. The laser energy was measured using an Ophir Nova II laser power/energy meter and a pyroelectric head PE-10 V2. A Newport® electronic shutter and digital exposure control were used to control the number of laser pulses to create craters using a pre-defined number of pulses. An Olympus® BX51 optical microscope equipped with a Prior Scientific® 3D stage (controlled by a Prior ProScan™ H31 controller) and a CCD camera was used to observe the ablation process, and to specify the ablation point and focus position of the laser beam. Crater morphology was characterized using a FEI Quanta® 200 FEG SEM. Sapphire, in the form of circular wafers of 3 mm thickness and 9.5 mm diameter, with random orientation (Esco Optics, New Jersey, USA) and brass [SRM 1107 naval brass B from National Institute of Standard and Technology (NIST), Gaithersburg, USA] were used as target materials for ablation by picosecond laser pulses. Sapphire and brass were selected in this study because they represent two different types of materials (i.e., dielectrics and conductors) which have different electrical, thermal, and optical properties. The ablation depth of craters were measured using an Olympus® BX51 optical microscope.
Results and discussion
Sapphire
Figure 1 shows the surface morphology of craters produced on sapphire at a repetition rate of 100 Hz and fluence of 2.3, 6.6, and 10.6 J/cm2, using 20, 50, 100, and 200 laser pulses. The laser beam was focused on the target surface using a 10× magnification microscope objective lens (Olympus UMPlanFL, 0.3 numerical apertures). Under these experimental conditions, the smallest crater diameter (8 µm) was obtained at fluence of 2.3 J/cm2. The craters were almost circular in shape and showed deposition of very fine particles on the surrounding sample surface. The crater depth and the amount of deposited materials were found to increase with increasing the laser fluence and number of laser pulses. At low fluence, cracks and fractures were not observed on the surface around the craters. Small surface cracks were observed at fluence of 6.6 J/cm2 when the number of laser pulses exceeded 100. Melting and ejection of molten droplets were also observed at fluence of 6.6 and 106 J/cm2 when the number of pulses exceeded 100 and 50 pulses, respectively. Cracks were observed on the sample surface at a lower number of laser pulses at laser fluence of 10.6 J/cm2. This is illustrated in Figure 2, where high magnification images of craters produced at a fluence of 10.6 J/cm2using 40 and 100 laser pulses are shown.
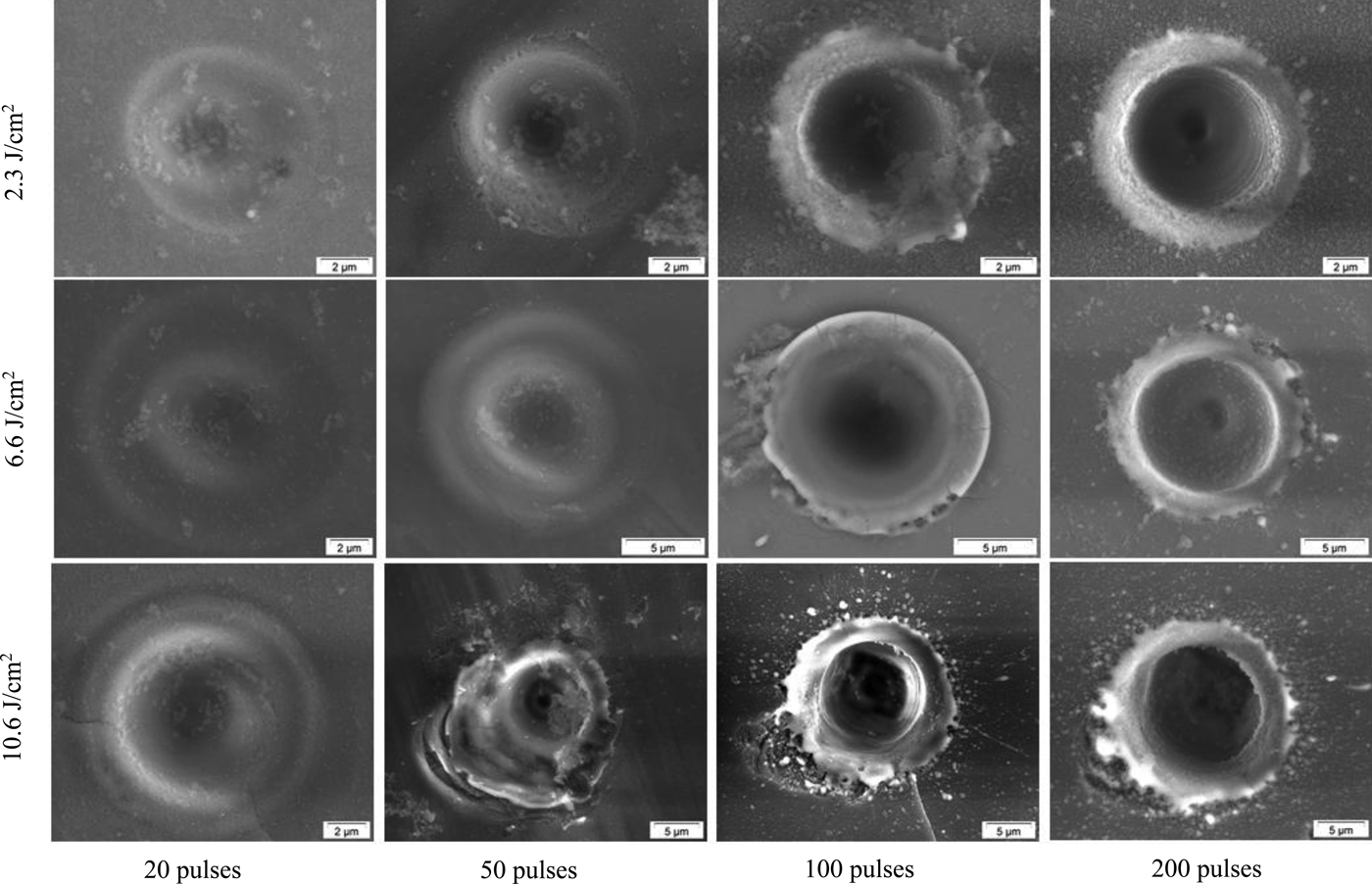
Fig. 1. Craters produced on sapphire at different laser fluence and number of laser pulses in air. Repetition rate was fixed to 100 Hz.

Fig. 2. A close-up image of craters produced on sapphire using 40 (a) and 100 (b) laser pulses at fluence of 10.6 J/cm2.
A distinct change in crater morphology was observed when ablation was conducted at higher fluence. Figure 3 shows the surface morphology of two carters produced at a fluence of 53 J/cm2 using 20 and 100 laser pulses at a fixed repetition rate of 100 Hz. Most of the laser energy was consumed in exfoliating the surface at the interaction area. The crater produced by 20 laser pulses was poorly shaped and showed a shallow, irregular surface structure. At 100 laser pulses, a small crater was produced at the center of the exfoliated structure. At higher fluence, ablation efficiency was low due to the dissipation of laser energy in heating and fracturing the irradiated area.
It is worth mentioning that the optics used in a given experiment is a very important factor that affects ablation rate and crater morphology. Different ablation rates and crater morphology can be obtained by using different objective lenses to focus the laser beam on the target surface. Figure 4 shows SE images of craters produced on sapphire in air using a different microscope objective lens (Newport M-10x, 0.25 numerical aperture). The craters were produced at a fixed repetition rate of 100 Hz using 20 (Fig. 4a), 50 (Fig. 4b), 100 (Fig. 4c), and 500 (Fig. 4d) laser pulses at a fluence of 79.5 J/cm2. The shape of the craters was found to vary with the number of laser pulses and fluence. Increasing the number of pulses gradually reduced the fractured area at the crater edge due to the gradual increase in the crater diameter (Fig. 4d). A single laser pulse was not able to induce ablation due to the poor absorption of sapphire to the incident laser wavelength. Application of multiple laser pulses to the same spot causes modification of the properties of sapphire at the irradiation area (Lenzner et al., Reference Lenzner, Krüger, Kautek and Krausz1999). The modification and roughening of the surface by successive laser pulses enhance absorption to the incident radiation due to the formation of defects (color centers) and the generation of electronic states within the forbidden energy gap (Stuart et al., Reference Stuart, Feit, Herman, Rubenchik, Shore and Perry1996; Lenzner et al., Reference Lenzner, Krüger, Kautek and Krausz1999; Bäuerle, Reference Bäuerle2011). The need for a certain number of laser pulses (incident at the same spot) to initiate ablation at a constant fluence is known as incubation (Hülsenberg et al., Reference Hülsenberg, Harnisch and Bismarck2008; Wu et al., Reference Wu, Yu, Cheng, Liao, Feng and Wang2011). Increasing the fluence reduces the number of laser pulses required to initiate ablation.

Fig. 4. Craters produced on sapphire in air using a 110 ps laser beam at a repetition rate of 100 Hz. The craters were produced using 20 (a), 50 (b), 100 (c), and 500 (d) laser pulses at fluence of 79.5 J/cm2.
The surface morphology of the craters produced on sapphire using multiple picosecond laser pulses varied with location of the crater on the surface (i.e., craters produced under similar conditions were not reproducible). This can be attributed to the basic processes required to initiate ablation in transparent materials. Material removal or ablation starts with absorption of laser energy by free electrons (i.e., seed electrons) that are available in the interaction volume, and the subsequent transfer of energy to the lattice of the target material. The absorption mechanism of non-UV wavelengths depends on the type of the target material and on the laser intensity (Liu et al., Reference Liu, Du and Mourou1997). Linear absorption is the principal absorption mechanism of opaque materials when using low-intensity, long pulse-widths lasers (Liu et al., Reference Liu, Du and Mourou1997). In transparent materials, due to the lack of free electrons, non-linear absorption must occur to create ablation. The presence of seed electrons is essential to start ablation in transparent materials using low-intensity and low photon energy lasers. A free electron, upon absorbing the laser energy, can gain enough kinetic energy to liberate a bound electron upon collision (impact ionization) leading to generation of two free electrons. The two free electrons can gain enough energy to liberate another two bound electrons leading to generation of four free electrons. The process of free electron generation continues and leads to an avalanche, where the free electron density grows exponentially to reach the critical plasma density (Liu et al., Reference Liu, Du and Mourou1997). At this moment, the interaction volume that was initially transparent becomes an absorbing volume (Liu et al., Reference Liu, Du and Mourou1997). In transparent materials, seed electrons are rare and are randomly distributed over the target material. Therefore, ablation of transparent material using long-wavelength and long-pulse-width lasers is stochastic and not reproducible. It was reported that non-linear processes dominate laser–matter interaction when the laser pulse width is <10 ps (Ben-Yakar and Byer, Reference Ben-Yakar and Byer2004; Bäuerle, Reference Bäuerle2011; Stafe et al., Reference Stafe, Marcu, Puscas, Ertl, Lüth and Mills2014). The laser pulse width (110 ps) used in this study was 11 times higher than this reported limit, which makes it closer to the behavior of nanosecond lasers. This explains the observed variation in the crater morphology with location on the target surface.
Figure 5 shows the dependence of ablation crater depth on the number of laser pulses at fluence of 66 and 106 J/cm2 at a repetition rate of 100 Hz. Ablation rate (ablation depth/pulse) was calculated from the slopes of the curves in Figure 5, and was found to be 90 and 260 nm/pulse for the laser fluence of 66 and 106 J/cm2, respectively. It was not possible to estimate ablation rates on sapphire at low fluence using light microscopy due to the limited spatial resolution of the light microscope and the low ablation rate.

Fig. 5. Ablation depth of craters produced by picosecond laser pulses on sapphire as a function of number of laser pulses at fluence of 66 and 106 J/cm2. Repetition rate was fixed to 100 Hz.
A closer inspection of crater and surface morphology can reveal important information about the ablation mechanisms of transparent materials. The irregular shapes of the craters, and the development of cracks, and surface fractures observed around the craters produced on sapphire (Figs 1–4) can be attributed to the mechanical stress generated by the rapid thermal expansion of the target material (Perez and Lewis, Reference Perez and Lewis2002; Hu et al., Reference Hu, Wang and Zhai2011). The energy deposition of the laser pulses into the focus volume generate thermoelastic stresses that are important in determining the characteristics of material melting, generation of defects, and ejection of material (Miotello and Ossi, Reference Miotello and Ossi2010). The interaction of the laser-generated compressive stresses with the free surface of the irradiated target can generate strong tensile stresses that cause mechanical fracture, separation, and ejection of the surface layer of the brittle material (Miotello and Ossi, Reference Miotello and Ossi2010). It is clear from Figures 3 and 4 that fracture and exfoliation of sapphire are important during ablation with picosecond laser pulses at high fluence (Vilar et al., Reference Vilar, Sharma, Almeida, Cangueiro and Oliveira2014). In addition to cracks and surface fractures, a few spherical particles were observed around the craters (Figs 1 and 2). These particles are re-solidified from molten material ejected from the ablated site. The presence of such spherical particles around the craters indicates that material removal has some sort of thermal nature.
Two ablation mechanisms appeared to exist at the same time when investigating the SEM images of the ablated sapphire. Thermal ablation took place predominately at the center of the crater, while fracture and exfoliation occurred at and around the crater circumference. More information can be obtained from the BSE images of the craters shown in Figure 6. The relative contribution of both mechanisms to material removal depends on fluence and number of laser pulses. Cracks and fractures of the surface were formed during the first few laser pulses. Increasing the laser fluence and number of pulses increased melting at the crater center and exfoliation at the crater edges. The fractured area around the crater decreased gradually with increasing the number of pulses due to the growth of crater volume.

Fig. 6. Backscattered electron (BSE) images of craters produced on sapphire using 50 and 100 laser pulses at fluence of 39.8 J/cm2 (a–b) and 79.5 J/cm2 (c–d), respectively.
The morphology of the craters produced on sapphire using picosecond laser pulses is different from that reported in a previous study using the same experimental setup but with femtosecond (130 fs) laser pulses (Shaheen et al., Reference Shaheen, Gagnon and Fryer2015b). In case of femtosecond laser ablation, craters were more reproducible and easier to create using lower fluence. Cracks and surface fractures were less observed. This behavior is related to the dominance of non-linear absorption processes in femtosecond laser ablation due to the high intensity of the ultra-short laser pulses (Stuart et al., Reference Stuart, Feit, Herman, Rubenchik, Shore and Perry1996). The high intensity creates electrons in a process known as multi-photon ionization. This process provides seed electrons to initiate another non-linear process called avalanche ionization, which causes the electron density to reach the critical density required for material breakdown (Stuart et al., Reference Stuart, Feit, Herman, Rubenchik, Shore and Perry1996). Because the ablation mechanism in femtosecond laser pulses does not depend on the presence of seed electrons, which are rare and randomly distributed in transparent materials, the ablation process is deterministic with a well-defined ablation threshold and reproducible crater morphology.
Brass
Figure 7 shows SEM images of craters produced on brass using a variable number of laser pulses at a repetition rate of 20 Hz and fluence of 2.7, 13.3, and 79.5 J/cm2. Melting and formation of liquid droplets at and around the craters were characteristics of the ablation process. This is related to the conversion of the absorbed laser energy into heat at the interaction volume. Application of a single laser pulse at low fluence (2.7 J/cm2) led to modification of the central portion of the irradiated area and caused changes in contrast of the annular surface area surrounding it. The inhomogeneous behavior observed across the interaction area may be attributed to the variation of energy distribution across the laser beam, which has a Gaussian energy distribution. The laser energy is maximum at the beam center and the effect of the central portion of the beam is stronger than the lower energy outer edges. Increasing the number of pulses and laser fluence accumulates the effects and enhances the role of the outer area of the beam in inducing surface damage due to the accumulation of plastic deformation in the outer regions of the irradiated area (Mannion et al., Reference Mannion, Magee, Coyne, O'Connor and Glynn2004). The crater volume was found to increase with increasing the number of pulses and the fluence due to the increased amount of material removed from the interaction volume. The accumulation and re-solidification of the molten material at the crater circumference led to the formation of craters with high rims. Figure 8 shows a high magnification SEM image of a portion of the crater rim and the particles deposited around it.

Fig. 7. SEM images of craters produced on brass in air at different fluence and number of pulses.

Fig. 8. A close-up image of a crater edge (a) and the particles deposited around it (b). The crater was produced on the brass at a fluence of 39.8 J/cm2 and a repetition rate of 20 Hz.
Figure 9 shows the variation in ablation rate with fluence at a repetition rate of 20 Hz. Ablation rate was found to increase from 0.2 µm/pulse at fluence of 2.7 J/cm2 to 1.6 µm/pulse at fluence of 79.5 J/cm2. The increase in ablation rate was not linear because the rate of ablation decreased with increasing laser fluence due to the increased loss of the incident laser energy resulting from the interaction with the laser-induced plume, which causes absorption, reflection, and scattering of the incident laser beam. This prevents a portion of the laser energy from reaching the bottom of the crater resulting in a reduction in ablation rate. The behavior of picosecond laser interaction with brass under the conditions reported in this study (pulse with = 110 ps) is similar to that observed in nanosecond laser ablation (Shaheen and Fryer, Reference Shaheen and Fryer2012). Melting, ejection, and re-solidification of molten material and formation of craters with high edges are common in both types of laser. For laser pulses longer than the energy relaxation time (several picoseconds in metals), the energy is transferred from the laser pulse to the lattice by phonon–lattice coupling (Semerok et al., Reference Semerok, Chaleard, Detalle, Lacour, Mauchien, Meynadier, Nouvellon, Salle, Palianov, Perdrix and Petite1999; Shah et al., Reference Shah, Tawney, Richardson and Richardson2004). This provides a sufficient time for heating to take place during the laser pulse. At such conditions, thermal processes are the dominant mechanisms of material removal.

Fig. 9. Dependence of ablation rate of brass on laser fluence. Repetition rate was fixed to 20 Hz.
Conclusions
A SEM was used as a diagnostic tool to investigate the surface morphologies and mechanisms of material removal from brass and sapphire upon interaction with a 110 ps pulse-width laser beam in air at atmospheric pressure. The surface morphology was found to depend on laser fluence, number of laser pulses, and the type of target material. Exfoliation and fracture of the surface were characteristics of sapphire ablation at high fluence. Melting and ejection of molten material were also observed around the craters produced on sapphire. This morphology behavior can be attributed to the accumulation of heat during successive laser pulses and the rapid expansion of the irradiated volume, which generates internal stresses that propagate through the material causing cracks, exfoliation, and melting of sapphire. Craters produced on sapphire were not reproducible and showed morphology that varies with location on the surface. Thermal processes were dominant in picosecond laser ablation of brass, as evidenced from the SEM images of the craters where melting, ejection, and re-solidification of molten material were characteristics of the ablation process. Ablation rate of sapphire was lower than that of brass due to differences in the dissipation of laser energy in heating and fracturing of the irradiated volume. The ablation rate of brass was found to increase with fluence. The increase in ablation rate was not linear because the rate of ablation decreased with increasing laser fluence due to the increased loss of the incident laser energy caused by the interaction with the laser-generated plume.
Author ORCIDs
Mohamed E. Shaheen, 0000-0002-2906-2147.
Acknowledgments
NSERC Discovery Grants to JEG and BJF and CFI/MRI Leading Edge Funds. The authors would like to thank Sharon Lackie for her help during SEM measurements.