To prevent these Defects, as well as to shorten the labour and lessen the Expense of so many successive operations as the silk passes through to the state in which we receive it, the most eligible improvement would be to have it wound of at once from the Cocoons into skeins of such duality and Dimensions as may fit it for the European Markets after the manner of China and Italian Raw Silk. Footnote 1
Bengal raw silk attracted the interest of the European trading companies since the seventeenth century. However, this trade was hindered by the low quality of the silk that did not find widespread use by the European silk weaving industry. In the 1770s, driven by the demand for raw silk in Britain, the EEIC decided to draw on knowledge transfer and implement the Piedmontese system for the reeling of silk in Bengal. Footnote 2 The central focus of the project was to improve the quality of raw silk. The aim of the company was to produce what it called “Bengal Italian raw silk”: Bengal made raw silk of the same quality as the highly sought after Italian silk that would have allowed a reduction in the importation of raw silk from Italy. Footnote 3 This article considers the transfer of the Piedmontese silk technology to Bengal and asks why the transfer was only partially successful. It highlights the role played by the organization of production and management for the success of technology transfers.
Part One outlines the argument of the article. Part Two examines the position of Bengal raw silk on the British market. Part Three studies the process of the transfer of the Piedmontese technologies to Bengal. Part Four analyzes the role of centralization in the success of the transfer. Part Five considers the effectiveness of the new reeling system in Bengal. Part Six outlines the problems with the quality of the silk and the role of incentives. Part Seven concludes.
Knowledge Transfer, Organization of Production, and Transaction Costs
This article addresses two questions: Why do firms centralize, and what determines the success and failure of technology transfers? The benefits of centralization of production in economic history literature are most often discussed in connection with the emergence of the factory system. The argument of this article is that transaction costs associated with transfers of technology are incentives for centralization of production. Centralization allows for the transmission of knowledge of new production processes more easily and with less cost since labor force is spatially concentrated. Centralization should also help to mitigate agency costs, which can seriously jeopardize the effectiveness of the technology transfer. However, as centralization without appropriate attention to governance and management does not inevitably reduce agency problems, management and governance needs special attention.
Literature discusses centralization of production and vertical integration either as a separate topic or in relation to technological innovations. Von Tunzelmann studied the interrelationship between the technological and organizational change and pointed to the fact that the choice of technology—labor savings versus capital savings, focused on quality or quantity of production—depends on the context of economic and social factors. Footnote 4 According to Pollard, in some industries, technological innovations preceded whereas in others it was organizational innovations. Footnote 5 Beniger argued that innovations of systems of organization and the innovations of technologies are self-enforcing. Footnote 6 Alternatively, economic historians such as Landes argued that technological changes are key to changes in the organization of production. Landes, for instance, argued that technology, not organization, was the key for early industrialization. Footnote 7
Several authors, on the other hand, identified centralization as the key factor for the emergence of the factory system. Among the most prominent proponents of the benefits of centralization has been Marglin, who argued that it gave capitalists power over organization of labor and production. Footnote 8 Conversely, Williamson has considered hierarchical systems of organization of labor as the most efficient because this system limits transaction costs. Footnote 9 Williamson, similar to Coase before him, holds economization on transaction costs as the key factor decisive for vertical integration. Coase and Williamson argued that when the costs of using price as the mechanism for organizing a transaction become too high, it is substituted with a different mode. Footnote 10 Williamson compared different modes of organization of labor—such as a putting-out system, collective ownership, inside contracting, continuous and periodic contracting, and hierarchical organization—and found hierarchy to be the most efficient mode, as it entails the lowest transaction costs. Footnote 11 Although different manufacturing activities have similar transaction costs, certain conditions (i.e., technology) can make modes other than hierarchy advantageous. Footnote 12 Therefore, only when the costs of using price and systems of contracts as the mechanisms for organizing a transaction become too high is there an incentive “to remove the transactions from the market and organize them internally.” Footnote 13
Neither Marglin, Coase, nor Williamson considered technology to be the key for vertical integration and centralization. Nevertheless, Williamson considered the choices of technology and organization of production to be dependent on each other, and argued that “technological changes may render some organising modes intolerable.” Footnote 14 This shows that despite the low transaction costs, vertical integration might not always be the most efficient solution. Berg has taken a similar view; she showed that in late eighteenth-century and early nineteenth-century Britain, other systems of organizing production—such as small-scale factories or flexible organization—successfully operated alongside vertically integrated large-scale factories. Berg directed attention to the fact that these alternative systems posited advantages for the entrepreneurs, especially flexibility and the ability to respond to regional conditions and economic cycles. Footnote 15 Moreover, in places like Birmingham or Yorkshire, small-scale producers still benefited from concentration of skilled labor and could thus take advantage of specialization and division of labor. Footnote 16
Different views on centralization and the emergence of firms were presented by the agency theory, which studied these issues from the point of agency problems. Agency theory showed that the centralized form of organization is apt to reduce agency costs. Agency problems emerge when the interests of principals and agents are in conflict or when it is “difficult or expensive for the principal to verify what the agent is doing.” Footnote 17 Alchian and Demsetz built their theory of emergence of firms on the proposition that team production brings net increases in productivity but that shirking decreases this productivity. Teams, therefore, need a monitor who specializes in management of a team and can change or terminate the contract of the shirking team member. Footnote 18 Alchian and Demsetz introduced into the discussion of emergence of firms factors such as “team production, team organisation, difficulty in metering outputs, and the problem of shirking.” Footnote 19 Jensen and Meckling focused on agency costs that arise from the contractual relations between principals and managers. They argued that the separation of ownership and control in modern enterprises, and the fact that decision making is in part delegated to managers, means that managers may not always act in the best interest of stockholders. Therefore, managers need to be monitored and presented with incentives. Footnote 20 Jensen and Meckling also focused on the relation between knowledge, control, and organizational structure. They studied the role of knowledge in decision making in organizations in which control problems cannot be solved by alienability of these rights. Their research showed that efficiency increases if decision rights are allocated to individuals with decision-relevant knowledge. However, since individuals are self-interested, firms need organizational control systems to deal with agency problems. Footnote 21
I want to take these arguments about centralization further and point to the fact that different manufacturing activities can have different transaction costs—for instance, because they have different requirements on quality control, the quality of the product is difficult to discern, they offer scope for embezzlement, etc.—and thus create incentives for specific types of organization of production. Moreover, the cost of transmitting knowledge of new production processes, machinery, and skills posit transmission costs. Mokyr defined these costs as similar, yet not equal, to transaction costs. I suggest that these costs equate with the costs of transmitting knowledge, and these costs, according to Jensen and Meckling, “depends on factors such as the nature of the knowledge, the organisational environment, and technology.” Footnote 22 The more specific the knowledge is, the higher the costs. Footnote 23 Jensen and Meckling in their article focused on the transfer of knowledge needed for efficient decision making, whereas this article concentrates on transfers of knowledge of manufacturing technology. In such cases, the nature of knowledge and technology makes certain organizational forms more effective for knowledge transfer.
Different systems of organization of labor posit different transaction costs on transfers of technology. This is because the transmission of knowledge of a new technology has its costs, and these transmission costs can be either mitigated or increased by a system of organization of labor. Mokyr has argued that high costs of moving information were key to the emergence of centralized factories. Mokyr argued that the centralization of production was propelled by the development of technology and by the growth in the pool of knowledge. Technological progress made concentration of workers in centralized factories necessary because the newly emerging production processes “required a level of competence that was beyond the capability of the individual household.” Footnote 24 As instructing, supervising, and coordinating workers at home would be too costly, making once best-practice techniques too complex, firms became the mechanisms of knowledge transmission. Hence, Mokyr argued that it was the relative costs of moving information on the best-practice techniques, not the costs of moving workers into factories, which facilitated the factory system. Footnote 25
Under efficient systems of management and control, centralization also mitigates principal–agent costs. Paying attention to systems of organizational control is essential because principal–agent problems reduce the effectiveness of knowledge transfer. Factors such as geographical distance, ineffective communication technology, and complexity of the technology and manufacturing processes increase negative impact of principal–agent problems on technology transfer. These factors were amply present in the case of the transfer of Piedmontese technology to Bengal.
In general, geographical distance and ineffective communication technology were factors that gave rise to information asymmetries that generated agency problems in early modern trading companies. In the literature on early modern European trading companies, principal–agent problems are usually associated with private trade, which is said to cause misalignment of incentives. It has been argued that private trade was the major source of conflict between principals and overseas agents by Chaudhuri in the case of the East India Company, and by Davies and Wilson for the Royal African Company. Footnote 26 Similar views were taken by MacKay for the Hudson Bay Company and by Willan for the Russian Company. Footnote 27 Adams and Hejeebu, on the other hand, focused on the role of private trade in motivating and managing overseas agents and in expanding the long distance trade. Hejeebu found that the English East India Company used access to private trade as a tool for motivating its agents to fulfill orders from London. Footnote 28 The EEIC allowed its overseas agents to engage in intra-Asian private trade, and since this trade represented an important source of wealth—and satisfactory performance was necessary for keeping access to this trade—the agents had an incentive to follow orders from Europe. Footnote 29
The case presented here differs from the way in which principal–agent problems are treated in literature on the trading companies. By focusing on manufacturing, this article points to a different type of agency problem. There already were principal–agent problems in the phase of production, which affected enforcement of quality and the adoption of best practices; in this way, the problems impaired the quality of the goods exported to Europe.
Bengal Raw Silk on the British Market and the Push for Technology Transfer
Silk industry was one of Britain’s seven most important export sectors until the nineteenth century. Footnote 30 The climatic conditions of the British Isles would not allow the cultivation of mulberry trees and the silkworm-rearing necessary for the production of raw silk. The British silk industry was therefore totally dependent on imports of raw silk. In the eighteenth century, most of the raw silk used in England was procured from Italy, the Mediterranean, Turkey, China, and India. The British silk industry is often equated with Spitalfields silk weaving. In spite of the fame that the Spitalfields production attained between 1730 and 1760, and the scholarly attention it has received over the past two generations, the majority of the British silk production was of lower quality in comparison to other world producers and was mostly focused on small items rather than high-quality cloth, Footnote 31 as the British silk industry produced mostly smaller wares and haberdashery. The typology of the wares produced underpinned the demand for raw silk on the British market. Whereas broad weaving necessitated silk thread of the highest quality (in most cases, the threads needed to be thrown into organzine before they could be used), most of the British silk-weaving industry only needed medium-quality raw silk. Footnote 32 The silk used was neither too fine nor too coarse and had to be easily workable; that is, without the need to re-reel it prior to utilization.
In the early eighteenth century, most of the lower-quality raw silk was procured from Turkey, Spain, and Portugal, and it was used in the production of smaller wares. The best-quality raw silk was imported from Italy, from where Britain also imported thrown silk. Only Italian raw or thrown silk was used in broad weaving. Footnote 33 High-quality Chinese silk was also imported as it was appreciated for its whiteness. It was used principally in the production of hosiery and gloves. Footnote 34 Bengal raw silk, by contrast, was considered the lowest quality to be found on the market, and its use prior to the 1770s was limited. Footnote 35 Bengal raw silk was repeatedly described as inadequate quality material by the British silk manufacturers and weavers, and was criticized for its coarseness and its inequality, meaning its only appropriate use was in the production of haberdashery. Footnote 36
Without quality improvement, the company-imported silk could not gain higher market shares because its use remained limited, even in the production of haberdashery. Haberdashery necessitated silk of a certain standard of quality as to be ready to be used without the need to be reworked prior to throwing and weaving. Footnote 37 Despite that the consumption of silk textiles had already spread beyond the elites by the late Middle Ages, and that had silk started to be consumed by wider social strata, the quality of the silk thread still played a key role. Footnote 38 The quality was regulated by the market demand rather than a state-imposed institutional framework or by guilds. Footnote 39 Silk thread necessary for dress accessories such as bonnets, hats, gloves, belts, stockings, and shoes—items of common use also among the less wealthy social strata—did not need to be made of such high-quality thread as broad weaving. Footnote 40 Despite the specialization of the eighteenth-century British silk industry in the production of smaller wares rather than on the highest quality broad silks, the company’s focus on increasing the quality of the Bengal thread was well reasoned.
The key problem was the production methods adopted in Bengal, which were lagging behind other silk-producing regions. Since the 1750s, the EEIC tried to implement changes to the reeling methods (the process of production of silk thread from silk cocoon). The company attempted to rectify the inequality of color, fineness, and length in skeins; for this purpose, the EEIC had the silk re-reeled before sending it to Europe. However, this measure was not sufficient, so in 1757 the company sent to Bengal Richard Wilder, a silk specialist. Footnote 41 In the 1750s and 1760s, Wilder and his successor, Joseph Pouchon, attempted to implement several changes to reeling technologies, such as knotting of silk. Footnote 42 The changes were supposed to rectify the inequality of threads and make the thread more round. Footnote 43 Even though these changes represented miniscule alterations to the techniques of silk reeling, they were opposed by reelers and were never implemented beyond the stage of experimentation, because it was impossible to effectively enforce them under a putting-out system. Footnote 44
Transfer of the Piedmontese System of Reeling to Bengal
In 1769, aware of the dissatisfaction of the British silk manufactures with the quality of the Bengal raw silk, the EEIC decided to introduce Piedmontese reeling technologies, specifically the system of reeling practiced in Novi. Footnote 45 By choosing the Piedmontese system, the company opted for a complex system of production with a system of organization dissimilar to Bengal.
In the silk industry, factory-type organization of production was adopted sooner than in other industries in response to the introduction of complex reeling technologies. Footnote 46 The emergence of silk filatures in seventeenth-century Italy was associated with technological innovation, quality enforcement through discipline, prevention of embezzlement, and increased dexterity in production. It was not related to the use of water or steam power, the increase in specialization, or scale of production. The profitability of the centralized system of production in the seventeenth-century and eighteenth-century silk industry was underpinned by specific factors: requirements for quality and the need to keep labor costs down. These factors made the centralized system indispensable for the production of high-quality silk. The Piedmontese system of silk reeling—the process of making silk thread from cocoons—relied both on technology and the system of organization of production to produce high-quality silk thread. Figures 1 and 2 depict the technical and organizational innovations of the Piedmontese system. The invention of the Piedmontese reeling machine would not have been equal to the task of producing high-quality silk threads if the system of organization of production had not introduced hierarchy and centralization of production.

Figure 1 Innovations of the Piedmontese system of reeling.
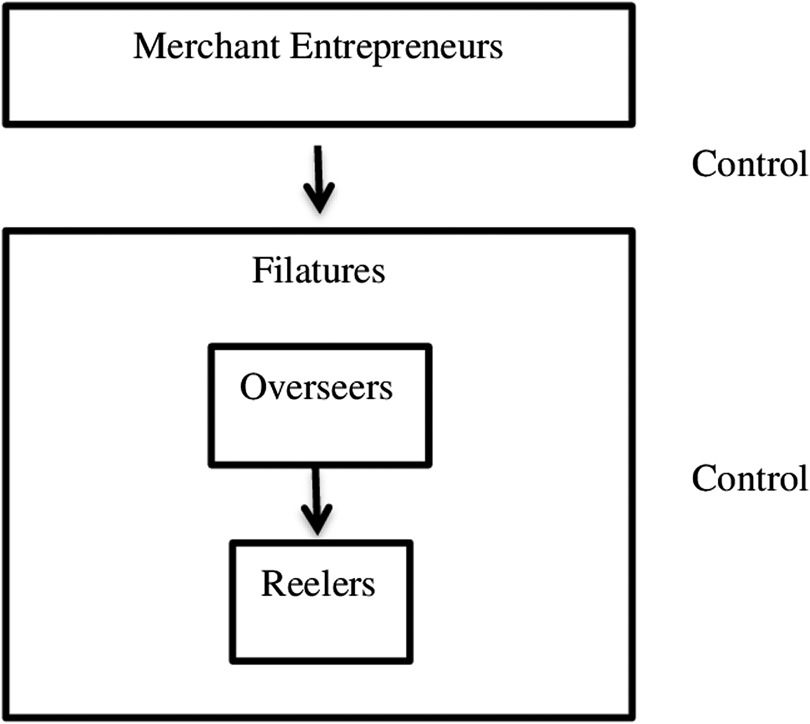
Figure 2 The system of organization of production in the Piedmontese silk reeling in the eighteenth century.
In the Piedmontese silk industry, centralization of production was a response to technological development and the outcome of the requirements on the quality of the silk. In Bengal, dispersed household production was the outcome of lower requirements on the quality of the end product, flexibility of production, social and economic context, and so. In Piedmont, the adoption of the Piedmontese reeling machine led to filature production. Filatures were factory-like establishments that represented an important turn toward a centralized proto-industrial system of production. Filatures were characterized by the supervision of reelers, inflexible discipline, and managerial hierarchy. Reeling silk in filatures was meant to ensure the high quality of reeling as well as the efficiency of reelers. Footnote 47
Implementation of the Piedmontese reeling system necessitated a host of changes, including in the organization of labor in silk reeling and in procurement, along with setting up silk-filatures training for the Bengalese workforce. This explains why the EEIC became directly involved in reeling silk and became a producer of goods rather than just a trader.
In order to implement the Piedmontese system, the company sent the equipment from England to Bengal for setting up the filatures, contracted silk specialists from Piedmont to supervise the building of the filatures in Bengal, and retrained the Bengalese silk reelers. Since the EEIC did not have knowledge of the Piedmontese system, the company sent three silk specialists to Bengal—James Wiss, Pickering Robinson, and William Aubert—to become superintendents of the company’s silk investment in Bengal and to set up silk filatures. Footnote 48 Reelers or mechanics accompanied each superintendent to assist with training the Bengalese workforce in the Piedmontese reeling technology. These silk specialists were contracted by the EEIC on the recommendation of the silk superintendents. Footnote 49 The superintendents were first stationed in Puddapar, Bauleah, and Rungpore, the principal silk production areas of Kasimbazar. Footnote 50 After each silk filature was established in its respective aurung, they were to move to other silk aurungs “in order to encourage a spirit of emulation [so] that the method of spinning and drawing the silk as practiced at Novi … should be entirely adopted throughout the whole Country.” Footnote 51 The principles of transfer and diffusion of knowledge were essential for the venture.
Silk machinery was initially produced in Italy and then later in England, and transported to Bengal. From 1770s, machinery was produced in Bengal according to models sent from London. Due to the differences in climate in Piedmont and Bengal, the machinery needed to be adapted; that is, wood was replaced with iron and brass. Footnote 52 Since the alterations to the technology were made in England, it further prompted the transfer of silk machinery from Europe to Bengal. Overall, from 1769 to 1796, the company sent 3,825 sets of cog wheels and 3,833 double-crossing machines to Bengal. Footnote 53 No image of the Piedmontese reeling machine used in Bengal survived. The only indication on how the machinery looked comes from an 1838 EEIC’s publication, which states that it was identical to that described in Lardner’s book (Figure 3). Footnote 54
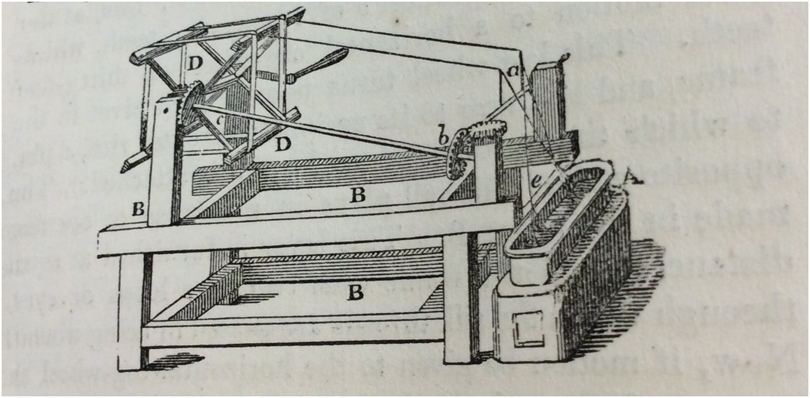
Figure 3 Reproduction of Piedmontese reeling machine from 1838 EEIC publication.
According to Lardner’s description, the reeling machine consisted of three parts: Component A depicts the boiler (or basin); Component B, the frame; and Component D, the reel. The fire in the furnace brought the water in the basin to a boil. The cocoons were placed into the basin in order for the gummy substance covering the filaments to dissolve. A number of filaments were then passed through the reel (D). The reel consisted of wheels with a specific number of teeth, cog wheels, and staves, and a double crossing-machine. Lardner’s image and description of the machine did not mention the double-crossing machine, which was a key innovation of the Piedmontese silk reeling machine. It appears that the double-crossing machine was not known in Britain at the time. In Bengal, it was introduced by one of the silk specialists familiar with the technology. Footnote 55
Reeling was done in filatures. Bengal filatures were larger than the ones in Piedmont and they had to be adapted to the climate. In order to survive the monsoon climate, they were made of bricks and wood, such as bamboo, teak, malaca, and so on. Footnote 56 First, filatures were set up in Bauleah, Commercolly, and Kasimbazar, principal silk-producing regions of Bengal. The Bauleah and Kasimbazar filatures each had 104 furnaces; the Commercolly filature had the largest capacity, with 208 furnaces. Footnote 57 The latter filature was built for 99,452 Sicca Rupees (£10,774); the combined costs of building the Bauleah and Commercolly filatures, with 104 furnaces each, amounted to 184,835 Sicca Rupees (£20,024). Footnote 58 Each furnace had three reels, and thus could accommodate three reelers. Footnote 59 Bengalese reelers did the work; although it cannot be said decidedly, it appears that reelers were paid by the piece. Footnote 60
Overseers supervised the reelers; their tasks were to ensure that the quantity and quality of the reeled silk met company requirements. The aim of the company was to have one overseer per forty furnaces (that is, 120 reelers), similar as in in Italy; however, it can be expected that the numbers of reelers per overseer differed among filatures. Footnote 61 Each filature was managed by a director (sometimes called resident) or by a superintendent. It was supposed to be managed according to the guidelines and orders sent from London, which were sent to the Board of Trade in Bengal. The Board of Trade was supposed to disseminate them to the directors and superintendents in the silk-producing regions.
The switch from a putting-out system to a centralized system of production under one roof reverberated also to the procurement system, which changed significantly as the company started to procure cocoons instead of reeled silk. The EEIC decreased the number of intermediary merchants it needed. The company also stopped needing the services of re-reelers and gomashtas, who were merchant agents that procured goods for the EEIC. It only relied on Pycars—contracted agents—who, at the beginning of the rearing season, advanced money given to them by the EEIC to the peasants rearing silkworms. At the end of the rearing season, the Pycars collected the cocoons for the company. Footnote 62
Role of Centralization for the Transfer of Piedmontese System of Reeling to Bengal
The principal reason that led the EEIC to implement the Piedmontese system was to overcome the opposition of reelers to implement changes to the reeling practices. Such changes were necessary to achieve production of high-quality raw silk. The centralized system of organization of labor was the key factor that allowed changes to the reeling system to be implemented. The adoption of the filature system allowed transmitting the tacit knowledge of reeling through instructing large numbers of reelers in the Piedmontese method. This not only reduced the costs of instructing reelers in the new method, as Mokyr’s theory suggests, but also, and most importantly, made it possible to transfer the knowledge of new reeling methods that were known only to several foreign silk specialists to the silk-producing regions of Bengal. Footnote 63
The greatest challenge faced by the silk specialists who were commissioned to transfer the Piedmontese system of reeling to Bengal was the knowledge transfer of reeling practices. The system of organization of production played an important role for the success of this task. A key element of the Piedmontese reeling system was the silk filature, originally aimed to promote quality enforcement, in Bengal filatures; this played a key role in disseminating the knowledge of the Piedmontese reeling practices.
First, production in a centrally organized filature proved necessary if changes to reeling practices were to be successfully implemented. One of the reasons why reelers refused to implement new practices under a putting-out system was fear that these practices would reduce the speed of reeling and, therefore, the quantities of reeled yarn produced. Footnote 64 In contrast to the previous putting-out system, in filatures’ reelers did not bear the full cost of learning and became willing to implement the new method of reeling.
Second, successful implementation of the Piedmontese reeling method hinged on adoption of the Piedmontese reeling machine. As this was a considerable capital investment, it made a putting-out system impossible. However, it was not only the cost of the technology that caused a change in the organization of labor. The cost of maintaining the reeling machine was equally important. Maintenance necessitated specialized knowledge, and each filature needed specially trained mechanics to carry out maintenance and to repair the machines. The company had to employ expert mechanics from Europe who were familiar with the reeling machine to transmit this knowledge. Footnote 65 This supports the argument that factory establishments emerged because maintenance of complex machinery required expert knowledge that, in general, was not available at the household level of production. Footnote 66
Third, filatures decreased the transmission costs as they enabled a single foreign silk specialist to instruct a number of Bengalese reelers at the same time and to supervise them in the initial stages of learning the new method. In the Bengalese case, without centralization of production, it would be effectively impossible to transfer the knowledge and instruct sufficient numbers of reelers in the new method. The Bengalese reelers had to be instructed in a new reeling method, and setting up centralized plants reduced the costs of disseminating the new practice by making it possible to train multiple reelers at once. The presence of an experienced silk specialist familiar with the method was essential because the technique was not formally codified. Demonstration was also indispensable to overcome the language barrier between the foreign silk specialists who spoke Italian and/or English and the local workforce.
The Effectiveness of the Piedmontese System in Bengal
In order to assess the effectiveness of the transfer of the Piedmontese reeling technology, I examine the quantity of Bengal raw silk imported to the British market, its price, sales, and the quality of the silk.
It is clear from Table 1 that the adoption of the Piedmontese technologies enabled the EEIC to increase its share on the total imports of raw silk into Britain. While Bengal raw silk represented only 8.7 percent of the total imports in the period 1750–1760, after the adoption of the new reeling system, it rose to over 40 percent. The evidence is supported also by data from Bengal filatures. Bauleah filature, with 104 furnaces, produced 533 maunds 10 Seers 9 chhattaks (39,998 lbs.) of silk in the first four years of its existence. The Commercolly filature, with 208 furnaces, produced 1,096 maunds 32 seers 3 chhattaks (82,260 lbs.). As Table 2 shows, the establishment of the Bauleah, Commercolly, and Kasimbazar filatures enabled the company to double the value of silk procured from the Kasimbazar region between 1772 and 1776.
Table 1 The share of Bengal raw silk on the total imports of silk imported into Britain, 1750–1789
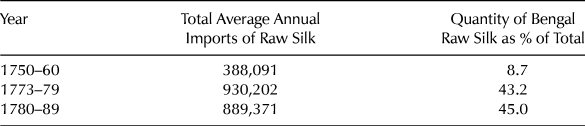
Source: Compiled from Mitchell, British Historical Statistics, 343; Chaudhuri, Trading World, 534; Reports of the Committee of Warehouses, 6, 10, 14 (see note 36).
Table 2 Value of raw silk and silk piece goods procured in Kasimbazar, 1768–1776
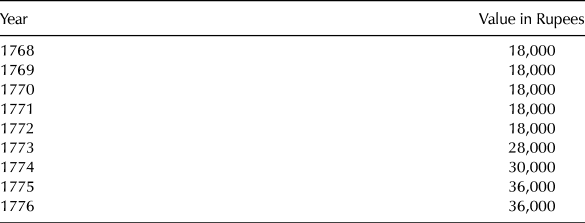
Source: See note 68.
Overall, as shown in Table 3, Bengal became quantitatively the most important exporter of raw silk to Britain. As the importation of raw silk from Bengal increased, importation of raw silk from Aleppo, Valentia, Naples, Calabria, and other places in Mediterranean decreased. Footnote 67
Table 3 Quantities of raw silk imported into Britain, 1773–1792
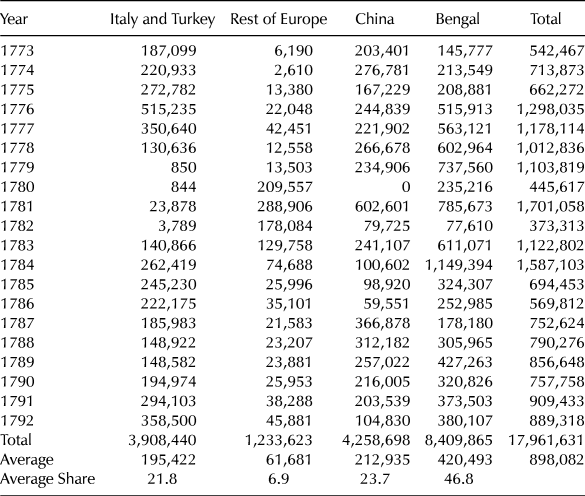
Between 1779 and 1783, Italian raw silk was being imported into Britain mostly via other European countries due to war. This explains the sudden increase in imports from other parts of Europe and decrease in imports from Italy. Source: Reports of the Committee of Warehouses, 6–10 (see note 36).
Along with imports, it is also important to examine the prices of the Bengal raw silk on the British market. The EEIC expected that Bengal raw silk reeled according to the Piedmontese method would attain a price increase of about 25 percent. Footnote 68 The data shows that filature silk attained prices 26 percent higher than the country-wound silk (Table 4.). However, if the price of Bengal raw silk is compared to the price of other types of raw silk imported to the British market, it becomes apparent that Bengal raw silk did not improve its position. Bengal raw silk continued to be considered as the lowest-quality silk in the market. The company had to wrestle with the continuing perception by British manufacturers and contemporaneous economic writers that Bengal raw silk was a material “fit only to be used in the lowest descriptions of manufactured goods, and its price in the English market, generally, was equal to about one-third of that of Italian silk.” Footnote 69 As contemporaneous silk experts claimed, Bengal raw silk was “of the commonest kind and fit only for inferior purposes, acceptable to the English manufacturer.” Footnote 70 The general consensus of the pamphleteers was that the lower quality of Bengal raw silk meant that it could fetch only a third or half of the price of Italian raw silk on the British market. Footnote 71 Attempts by the EEIC to present filature-made Bengal raw silk as a product of significantly higher quality were undermined by a lack of quality enforcement, which led to the frequent occurrence of substandard quality silk on sales. The reputation of Bengal raw silk thus remained low.
Table 4 Prices of filature and country-wound silk at London sales, 1792–1796

Source: IOR/E/4/640, 25 June 1793, ff. 513–514; IOR/E/4/643, 3 July 1795, f. 597; IOR/E/4/645A, 27 July 1796, f. 330.
Even though the adoption of the Piedmontese system of reeling enabled the EEIC to considerably expand exports of raw silk to Britain and the quality of the silk improved, the quality improvement was not sufficient. Figure 4 shows that the company was unable to sell large quantities of the silk it imported. From 1773 to 1795, the EEIC accumulated 651,783 sm.lbs. of unsold Bengal raw silk in its warehouses, and from 1801 to 1805 an astonishing 2,658,693 sm.lbs. Footnote 72 Overall, the inability to sell large quantities of Bengal raw silk was the issue that most severely affected the company’s silk trade, and it was directly linked to the quality of the silk. According to British manufacturers, the silk did not comply to the expected dimensions—that is the length and width of the skein—which created problems in the subsequent process of throwing. Footnote 73 Other complaints received by the company also related to the color of the silk. This was due to the cocoons going moldy or undergoing fermentation as a consequence of being stored incorrectly or because of moths decomposing inside the cocoons. Footnote 74 The silk was also found to be too coarse or too uneven. Footnote 75 The company in London also reported the concerns of throwsters and manufacturers on the “unevenness of threads in the same skain, and of foulness of the Silk.” Footnote 76 These complaints were often accompanied in the buyers’ reports on being deceived at sales because fine silk was mixed with coarse silk in the same hank. Footnote 77

Figure 4 Bengal raw silk imported and sold in Britain by the EEIC, 1773–1806.
Source: Compiled from Reports of the Committee of Warehouses, 6 (see note 36); L/PARL/2/55: Appendix to the Fourth Report of the Select Committee on the Affairs of the East India Company, 218, 232; IOR/E/4/645, 27 July 1796, 552.
Problems With Quality, Principal–Agent Problems and Incentives
The lack of improvement in quality of Bengal silk can be perceived from two angles: it could be put down to the clash of local practices with the Piedmontese technology, or to the failure on the part of the EEIC.
Previous research on the EEIC’s venture into the Bengal silk industry argued that the key problem for the company was the clash between the requirements of the Piedmontese technology and the socioeconomic context of Bengal. Authors such as Bhadra, Bhattacharya, Mukhia, and Ray emphasized the resistance of peasants, reelers, and merchants to the filature system. Footnote 78 They also argued that the EEIC had a considerable power over Bengal silk industry. Bhattacharya pointed to the fact that the introduction of the new system of reeling led to restructuring of the economic relations between peasants, intermediary merchants, and the company, and in this process the peasants largely lost control over production. Footnote 79 However, this loss of control and restructuring of the relations took place only late in the nineteenth century. Davini focused on the eighteenth century and early nineteenth century, and contended that the company’s ability to shape Bengal’s economy was very limited and that peasants could sell their silk on the local market independent of the EEIC. Footnote 80 Ray pointed out that the process of innovations in the Bengal silk industry was not continuous, and that by the late nineteenth century the industry lagged behind its competitors. Footnote 81
The literature on Bengal silk industry does not offer an explanation of why the company was unable to produce uniform quality silk, even though it successfully implemented the Piedmontese system of reeling. For this, it is necessary to consider the system of organization of production. The authors who studied the Bengal silk industry did not pay attention to the problems that the EEIC had in the internal management of the silk venture. The company’s various Governors of Bengal reformed the system of filature silk production in the late eighteenth century, yet none of the reforms eliminated agency problems. Warren Hastings, and later Charles Cornwallis, implemented changes to the system of raw silk investment and management of filature production during their respective time as Governors of Bengal. Footnote 82 In the early 1770s, Hastings implemented a contract system under which the company was contracting for silk from private filatures. The EEIC was forced to implement this system due to financial difficulties that it faced from the 1770s through the 1790s, when it channeled most of its funds into military pursuit in India. Footnote 83 In the case of silk production, it was decided that the easiest way to deal with a shortage of funds was to enable private individuals to build silk filatures in Bengal or to let them rent the company’s filatures to produce raw silk there. In 1786 Cornwallis introduced an agency system under which those in the position of commercial residents—servants of the EEIC in charge of procurement of silk (or other commodity) in specific areas—were commissioned by the company to produce silk in filatures. From the point of agency problems, the switch to the new system did not bring revolutionary change. Under the contract system, commercial residents often owned filatures or rented them from the EEIC and produced silk for the company; under the agency system, they became managers of these filatures. Nevertheless, factors that fostered agency problems, such as geographical distance, asymmetry of information, and lack of incentives on the part of the company’s employees in Bengal, remained present. The principal–agent problems that were at the heart of the problems with quality (and at times fraud) were caused by the conflicting interests of the Court of Directors in London and Board of Trade in Bengal as well as inefficient management practices.
Problems with the quality of export goods were associated not only with Bengal raw silk but also the EEIC had to frequently deal with this issue in its cotton or tea trade. In silk manufacturing, principal–agent problems were at the heart of the production of low-quality silk, which undermined the entire investment into the technology transfer. Centralization helped to reduce transaction costs and principal–agent problems in silk reeling. However, the new reeling methods brought new principal–agent problems and transaction costs, and these were not addressed through innovations in the organization of production. The key problem in silk manufacturing was that the incentives of reelers and the company’s servants employed in silk production were not aligned with the EEIC’s goal of producing high-quality silk.
Filature production was divided into a hierarchy of head factories: large filatures, and subfactories that were smaller filatures scattered in shorter or longer distances around the head factory of a silk production region. The main actors involved in filature silk production in Bengal were the Board of Trade (the highest management body in Bengal that was supposed to supervise the production and transmit guidelines from London), commercial residents (who were to oversee the company’s silk trade and investment into silk manufacturing in particular production regions), directors of filatures (sometimes called also superintendents, who managed particular filatures), and employees of the filatures (that is, the overseers and reelers). The role of the foreign silk specialists was to instruct and transmit best practices. The roles of the main actors were often not strictly separated; for example, commercial residents often acted as directors of filatures. The key issue was that, except for the foreign silk specialists, none of the actors had incentives to focus on producing uniform, high-quality raw silk, which was the goal of the Court of Directors in London (Figure 5).
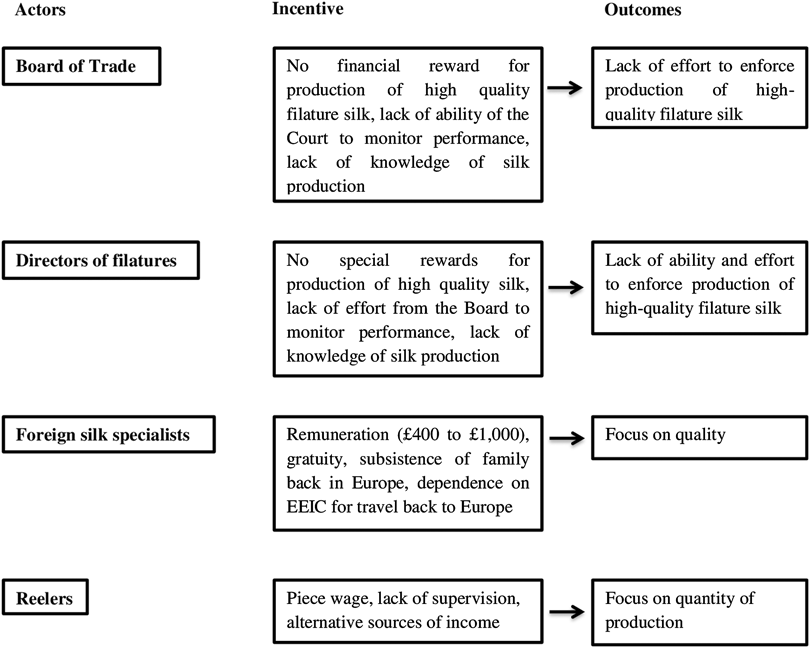
Figure 5 Actors, incentives, and outcomes in filature silk production.
Due to the geographical distance, the Court of Directors in London, the highest management body of the EEIC, had control only over the quality of raw silk. It had to delegate the enforcement of quality control of filature-reeled silk to the Board of Trade in Bengal. The Court believed that transmitting guidelines on the best practices of silk reeling and sending instructions to the Board of Trade would be sufficient for controlling the quality of filature silk. However, since the Court did not innovate the management practices used for controlling servants, it was unable to secure compliance with these guidelines and instructions. Also, the Court did not attempt to influence the incentives of its servants involved in silk production and, since most of the actors involved in silk manufacturing in Bengal (reelers, directors of filatures, commercial residents, and the Board of Trade) lacked incentives to focus on quality of production, the quality of raw silk lagged behind.
The Court seemed to have been unaware of the importance of commercial residents, and it hardly discussed their role in its correspondence to Bengal. Guidelines from London regarding quality enforcement only mentioned directors of filatures, who were supposed to take responsibility for the quality of silk produced in their filatures. Footnote 84 The Court did not consider that commercial residents could be made responsible for the quality of silk produced in the silk region they managed. Therefore, the switch from contract to agency system had only limited effect. The agency system reduced the scope for fraud by limiting the possibility to create collusive contracts, but it had no positive impact on quality of the silk. In the 1770s and 1780s, it was the practice of the Board of Trade in Bengal to make contracts for purchase of silk from private filatures, under which the EEIC paid significantly more for filature silk than the market price. Footnote 85 The profit was divided between the members of the Board of Trade and the participating filatures. Footnote 86 However, besides limiting opportunities for collusive contracts, the scope for opportunistic behavior on the part of the company’s employees in Bengal and the Board of Trade remained large and negatively affected the quality of silk.
The key problem was that the Court of Directors in London relied on the same management practices used for controlling servants, whose task was to procure export goods in silk manufacturing for Europe. Hejeebu pointed that such systems of management were sufficient for export trade. The combination of access to private trade and the threat of losing their privileges if they were dismissed were sufficient incentives to motivate the EEIC’s servants to fulfill orders from London. Footnote 87 Nevertheless, Hejeebu acknowledged the problem that the directors in London faced when attempting to ascertain whether decisions taken by servants in Bengal were acts of “mature consideration” or “malfeasance.” Footnote 88 Such problems were acute in silk production. The Piedmontese success in production of high-quality silk thread was achieved due to a combination of technological leadership, precision, and minute regulation. Footnote 89 These elements were lacking in Bengal filature production. It was difficult for the Court of Directors in London to ascertain whether this was due to a lack of familiarity with the best practice, as the company servants were not experts in silk production, or whether it was due to lack of attention to the task.
The inability of the Court to measure the performance of its servants became a central issue. In the case of procurement of goods for export, the Court was able to monitor whether orders were fulfilled and goods sent to Europe. Monitoring compliance with orders concerning silk production was, however, more difficult because the quality of filature silk was the only reliable indicator. In such a case, the Court needed to present its servants with incentives that would guarantee their focus on improving quality. Douglas W. Allen stated that presenting agents with the right incentives was essential for achieving the goals of the British Crown during the premodern era, when measuring performance and monitoring results was impossible. Footnote 90 Figure 5 shows that the incentives received by the Board of Trade in Bengal, directors of filatures, reelers, and foreign silk specialists were mostly incompatible with production of high-quality silk.
The contracted silk specialists were the only servants employed in the filature production whose conduct could be monitored by the company. There were never more than three silk specialists employed as superintendents of silk filatures and only up to ten silk reelers and mechanics at any one time. Therefore, it was easy to monitor their conduct, especially in the case of superintendents who were frequently in direct contact with London. Moreover, as these specialists were usually foreigners and dependent on the EEIC to travel back to Europe, it was essential for them to satisfy the orders received from London. Footnote 91 Futhermore, silk specialists were not allowed to enter private trade, thus limiting the possibility of a conflict of interest with the Court of Directors in London. Their remuneration did represent a premium high enough to motivate the foreign specialists to commit to contractual obligations. Silk superintendents received between £400 and £1,000 a year, with silk reelers and mechanics earning around £40 per year. To put the remuneration into perspective, it would take eleven years of service in Bengal for a company servant to receive £40 a year. Footnote 92 Furthermore, the families of the silk specialists left in Europe also received subsistence, and the silk specialists could have their contract extended, their salary increased, or obtain a gratuity for their services to the company. Footnote 93
No special incentives were provided for the Board of Trade and the directors of filatures, and the Court of Directors did not put any enforcement mechanisms in place, yet it relied on these servants to carry out quality improvements. I argue that the enforcement of quality improvement did not receive sufficient attention. Providing guidelines from London was simply insufficient. Contemporaneous traders, technicians, politicians, and political economists from all over Europe attributed the Piedmontese success solely to their superior reeling technology but omitted to mention the importance of regulation. Footnote 94 In Piedmont, as well as in other places in Italy, various institutional innovations emerged to regulate the quality of silk. Footnote 95 In Piedmont, merchants as well as the State were dependent on silk exports for income and custom revenues. Footnote 96 The enforcement of high-quality production was essential to success, and both merchants and the State became involved in it. The process of silk-thread production was regulated by the State, and quality was strictly enforced. As emphasized by Mauro Ambrosoli, the State “supervised the whole process of production, issuing instructions, laws, and regulations, granting trading privileges.” Footnote 97 The best practice in reeling was “enforced by minute regulations ordered by the Consulate of Commerce, a direct issue of the King himself.” Footnote 98
In its many attempts to enforce quality of production, the EEIC neglected positive incentives. In 1838 Giuseppe Mutti, a silk specialists employed by the EEIC in India, pointed to the importance of proper instruction for reelers and the benefits of motivating them through rewards. He claimed that to obtain silk of good quality, “It only requires some practice [training] and patience [… and] finally from time to time to reward him [reeler] with some presents for his exertions. —No such things are observed here and as to presents it is said to be an extravagance adding the man has got his (or good) pay.” Footnote 99 The wages the reelers received in Bengal were not high enough to make them commit to this job for a long period of time, and high turnover of reelers in filatures was common. Footnote 100 The essential problem was that reelers’ dexterity relied on long-term training. Therefore, Bengalese reelers could not compete with Piedmontese reelers, who were apprenticed in the trade for up to seven years before becoming master reelers. Footnote 101
It might be argued that the inadequate increase in the quality of Bengal raw silk was due to the quality of cocoons being low rather than due to the lack of quality enforcement in reeling. Footnote 102 It is undeniable that the quality of cocoons in Bengal was lower than in Piedmont, where the merchant-entrepreneurs had control over the production of cocoons. In Piedmont, merchants were able to dictate prices for which they bought cocoons from peasants and they only bought the highest-quality cocoons. Footnote 103 The EEIC, on the other hand, was involved only in silk reeling, sericulture was carried out by peasants, and the company lacked control over them. The EEIC was aware that the methods used in sericulture lagged behind the contemporaneous best practices and that the lack of improvement of the quality of the cocoons represented an impediment to the improvement of the quality of the silk thread. Footnote 104 However, the presence of local markets in which peasants could sell their raw silk limited the control of the company over these workers. The EEIC could not compel the peasants to adopt measures of quality improvement and rearing silkworms under the company’s auspices would have been very expensive. Thus, the company could only experiment with new practices. However, these activities were not successful; for example, the company’s experiments with the introduction of Chinese and Italian breeds of silk worms were without success. Footnote 105 Notwithstanding, in the end, the most serious impediment to the improvement of the quality of cocoons was the way they were handled by the EEIC’s servants. Cocoons often became moldy or entered the process of fermentation due to the inappropriate modes of storing. This had a negative impact on the color and strength of the silk thread as well as the quantity of silk reeled from cocoons. Footnote 106 Therefore, even if the EEIC had been able to effect the quality improvement of cocoons, without appropriate handling and storage their quality would have quickly deteriorated.
Conclusion
Literature that discusses centralization and vertical integration focuses on the role of technology or transaction costs as determining factors. This article found that a decision to transfer technology might also become a determining factor as centralization decreases the transmission costs of a transfer. I relied on Jensen and Meckling’s definition of transmission costs and applied it to manufacturing. Particularly, when knowledge is tacit, transmission costs are high and centralization becomes important. I also found that although centralization increases the possibility of transfer to succeed, agency costs can jeopardize the success of the transfer. Thus, the key is to mitigate agency problems by setting positive and negative incentives and systems of organizational control. This may necessitate innovations of the management practices.
In the case study of the raw silk manufacturing in Bengal, centralization facilitated transfer of the Piedmontese silk technologies because it enabled efficient dissemination of the knowledge of new silk technologies to large numbers of Bengal silk reelers. In this, the article argues along the lines of Joel Mokyr, who argued that centralization of production allowed for a decrease in the cost of instructing, supervising, and coordinating workers, and thus also the cost of knowledge transmission. The case presented here also shows that centralization in early modern period did not necessarily lead to deskilling through specialization. On the contrary, in silk reeling it led to increased precision and dexterity of silk reelers. Thanks to the transfer, the EEIC managed to increase the quantity of Bengal raw silk exported to Britain yet failed to produce silk of uniform quality. This was due to a lack of attention by the EEIC to its management practices and lack of incentives for the actors involved in silk manufacturing in Bengal. If the company paid more attention to the management of its employees in silk production and their incentives, the quality of the silk would have increased significantly.
This article identifies a different set of principal–agent problems than those normally ascribed to early modern trading companies. Instead of focusing on private trade as the main source of principal–agent problems, this article emphasizes the agency problems that arose in manufacturing due to the lack of monitoring and both positive and negative incentives. The key problem the company faced was how to incentivize its employees to focus on quality of production, to enforce precision of reelers, and to adopt the best practices. This was an issue different to the problem of how to ensure that employees did not embezzle from the trading company, did not use the company’s vessels for private trade, and send to Europe the ordered goods.