Natural zeolites possess unique properties of great commercial importance. Their structure is characterized by a network of interconnected micropores and channels that give the material impressive adsorption (Erdem et al., Reference Erdem, Karapinar and Donat2004; Sprynskyy et al., Reference Sprynskyy, Buszewski, Terzyk and Namieśnik2006), dehydration–rehydration (Bish et al., Reference Bish, Carey, Vaniman and Chipera2003), cation-exchange (Lorenz, Reference Lorenz1999) and catalysis properties (Arcoya et al., Reference Arcoya, Gonzalez, Travieso and Seoane1994). The zeolites are considered as inorganic polymers composed of an infinitely extending 3D network of tetrahedral TO4 units, where T is Si or Al. The same TO4 tetrahedron is the basic building unit of the geopolymers. The geopolymers are also inorganic polymer materials with structures similar to zeolites. In fact, in short range order, the geopolymer binder phase is composed of nano-sized crystalline zeolite-type structures (Provis et al., Reference Provis, Lukey and van Deventer2005). However, in long range order, the hardened geopolymer is X-ray amorphous (under Bragg diffraction conditions) and difficult to characterize (Davidovich, Reference Davidovits2011). In some cases, the geopolymer gel eventually begins to crystallize, forming zeolites. This crystallization is promoted by long curing at elevated temperatures (>60°C) and more alkaline systems. The most common structure types formed are sodalite, faujasite, gismondine and Linde type A frameworks (Provis et al., Reference Provis, Lukey and van Deventer2005).
In general, the main precursors of the geopolymers are reactive aluminosilicate powder materials and reagent solutions, namely the ‘hardener’ or ‘activator’. The activator is an alkali solution with pH >13. Usually, the activator is a mixture of alkali hydroxide and silicate (Provis & van Deventer, Reference Provis and van Deventer2009), although in some cases alkali carbonate (Cheah, Reference Cheah, Tan and Ramli2019), sodium sulfate (Criado et al., Reference Criado, Jiménez and Palomo2010), calcium hydroxide (Shi, Reference Shi1996; Ortega et al., Reference Ortega, Alcantara, Knight and Loizidou2000) or sodium aluminate (Phair & Deventer, Reference Phair and van Deventer2002; Brew et al., Reference Brew and MacKenzie2007; Hajimohammadi et al., Reference Hajimohammadi, Provis and van Deventer2008) have been used successfully. The aluminosilicate precursor might be of natural origin, such as kaolin, volcanic glass or natural pozzolans, but better results are obtained using thermally treated materials, such as metakaolin, calcined shales, fly ash, granulated blast furnace slag or other industrial residues. The reactivity of the aluminosilicate precursors is influenced by its specific surface area. Materials with large specific surface area, such as metakaolin (12.7 m2 g–1), are highly reactive. However, the large specific surface area and plate-like particle shape of metakaolin suggest that the water demand of a reacting geopolymer mixture is very high, causing difficulties related to drying shrinkage and cracking (Provis & van Deventer, Reference Provis and van Deventer2009). The raw materials are homogenized and the geopolymerization process takes place in the following overlapping stages: alkali reaction and depolymerization of the aluminosilicate precursor, gel formation of oligo-silate molecules, polycondensation, reticulation and solidification (Davidovits, Reference Davidovits2016). The primary area of application of the geopolymers is currently in the development of construction materials (as an alternative to Portland cements), low-cost ceramics, fire protection of structures, and as a host matrix in waste encapsulation (Provis & van Deventer Reference Provis and van Deventer2009), etc.
The structure of clinoptilolite is characterized by a system of micropores and channels occupied by water molecules and exchangeable cations (Mansouri et al., Reference Mansouri, Rikhtegar, Panahi, Atabi and Shahraki2013). Nitrogen physisorption is the one of the methods that has been used to obtain information on sample structures for decades.
Recent studies have shown that the hardened, silicate-activated clinoptilolite geopolymers possess satisfactory compressive strength and excellent adhesion to concrete (Nikolov & Rostovsky, Reference Nikolov and Rostovsky2017). However, the alkali silicate-activated clinoptilolite geopolymers show significant shrinkage (~14%; Nikolov et al., Reference Nikolov, Rostovsky and Nugteren2017), probably due to the high Si/Al ratio and the significant water demand of clinoptilolite.
Additional work has shown the potential of natural zeolites as geopolymer precursors. Villa et al. (Reference Villa, Pecina, Torres and Gómez2010) used an alkali silicate activator to synthesize geopolymers. The raw material requires thermal activation to obtain a geopolymer with good compressive strength. Geopolymers with compressive strengths equal to that which has been reported previously (~35 MPa) were obtained by alkali activation using calcium hydroxide (Ortega et al., Reference Ortega, Alcantara, Knight and Loizidou2000). In addition, sodium aluminate was used to synthesize silica fume-based geopolymers that set rapidly and harden at ambient temperature (Brew & MacKenzie, Reference Brew and MacKenzie2007). Fly ash, blast furnace slag and sodium aluminate (including waste aluminate) were used to obtain geopolymers with compressive strengths in the range of 40–80 MPa (Nugteren et al., Reference Nugteren, Ogundiran, Witkamp and Kreutzer2011). Phair & van Deventer (Reference Phair and van Deventer2002) successfully used sodium aluminate to activate fly ash. Finally, one-part mix geopolymers were developed using geothermal silica and solid sodium aluminate (Hajimohammadi et al., Reference Hajimohammadi, Provis and van Deventer2008). However, there are no available data on the alkali activation of natural zeolites with aluminate activators or with waste alkali solutions.
The aim of the present work is to improve the properties of geopolymers based on natural zeolite by calcination to prepare metazeolite and to use an alkali aluminate solution as a hardener, including an alkali aluminate waste solution. The natural zeolites are valuable raw materials and so it is more convenient to use low-grade natural zeolites or waste fractions as geopolymer precursors.
Materials and methods
Materials and sample preparation
The natural zeolite used as the aluminosilicate precursor in the present work was clinoptilolite (Z000) from Beli plast deposit, Imerys Minerals Bulgaria AD, with the following chemical composition (wt.%): SiO2 78.86, Al2O3 11.68, CaO 3.43, K2O 3.08, MgO 1.12, Fe2O3 1.12, Na2O 0.44, TiO2 0.19 and MnO 0.09, supplied by Imerys Minerals Bulgaria. The main phase was clinoptilolite, with opal-CT being the major impurity. The material was sieved through a 100 μm sieve. A total of 800 g of the natural zeolite was calcined in a muffle furnace (Naberherm LT 15/12) for 5 h at 900°C to obtain amorphous material. The heating rate was 10°C min–1, allowing for a 90 min preheating period. The material was cooled to ambient temperature in a closed chamber. The procedure was repeated to obtain ~1600 g of calcined zeolite. At 900°C, the clinoptilolite structure was completely destroyed without further recrystallization of opal-CT (Nikolov, Reference Nikolov2016). The calcined zeolite was designated as ‘metazeolite’ (Z900). Thus, the metazeolite is more vulnerable to OH– attack and therefore more reactive as a geopolymer precursor.
Two alkaline aluminate hardener solutions were prepared. The first solution consisted of analytical-grade NaAlO2, KOH pellets and tap water (samples with suffix ‘Al’), and the second hardener reagent was composed of KOH pellets dissolved in waste solutions from the aluminium anodizing industry (samples with suffix ‘ES’). The anodizing company Alumet BV (The Netherlands) generates a stationary rinsing bath waste solution, containing 69 g kg–1 Al and 17 g kg–1 free NaOH. The rinsing batch solution also contained 20–25 g kg–1 of the additive AD-AL-24B (Nugteren et al., Reference Nugteren, Ogundiran, Witkamp and Kreutzer2011). The additive used is a concentrated liquid containing poly-alcohols and sodium thiosulfate. The poly-alcohol has the complexes with the Al, thus preventing the precipitation of Al-oxides or Al-hydroxides. The sodium thiosulfate precipitates base metals as sulfides, as metals in solution such as Zn, Cu and Pb would have a negative effect on the surface of the Al products. Very fine suspended precipitates form in the bath, which gives the liquid a blackish colour (Nugteren, Reference Nugteren2010). A total of 12 geopolymer specimens (three of each series; Table 1) were prepared by homogenizing natural zeolite/metazeolite with the tempered hardener solution. The mixtures were stirred in a mechanical mixer for 1 min and allowed to mature. After 30 min, the mixture was stirred again for 30 s. The fresh metazeolite mixtures were more workable, with pronounced thixotropic behaviour, as opposed to the natural zeolite mixtures. Therefore, the geopolymer pastes based on metazeolite were prepared with a water-to-solid ratio of 0.40 (wt.%), while the pastes based on natural zeolite had a water-to-solid ratio of 0.45. The stoichiometric molar ratio of the prepared geopolymer pastes was H2O/M2O = 10 and the molar ratio of the activators (M2O/Al2O3) was 3.85 (where M2O is the sum of Na2O and K2O). The fresh geopolymer was poured into cylindrical moulds (50 mm × 30 mm). After 3 days of curing at 20°C, the samples were kept at 80°C for 3 days and cured under laboratory conditions, and the compressive strength was recorded on the 28th day.
Table 1. Composition design of the prepared geopolymer samples (in g 100 g–1 zeolite).

Methods of analysis
The powder X-ray diffraction (XRD) traces of the precursors and the geopolymer samples were recorded with a Bruker D-8 Advance diffractometer using Co-Kα radiation, and the samples thermally treated at 1150°C were recorded with a Bruker D-2 Phaser diffractometer using Cu-Kα radiation. The morphology of the samples was studied using scanning electron microscopy (SEM) on carbon-coated broken surfaces with a JEOL JSM-6010LA microscope equipped with an energy-dispersive X-ray spectroscopy (EDS) detector. The chemical composition of the natural zeolite was determined by wavelength-dispersive X-ray fluorescence (XRF) spectroscopy using a Panalytical Axios Max XRF spectrometer.
The specific surface area and pore characteristics were determined from nitrogen adsorption/desorption isotherms obtained at 77 K using a NOVA 1200e instrument (Quantachrome, USA). Prior to the measurements, the samples were outgassed for 16 h at 200°C under vacuum. The isotherms obtained were analysed to evaluate the following absorbance parameters: specific surface area (S BET), total pore volume (V t) and average pore diameter (D av). The S BET values were determined according to the Brunauer–Emmett–Teller (BET) equation. The V t and D av values were estimated according to the Gurvich rule at a relative pressure of ~0.99 (Gurvich, Reference Gurvich1915). The S BET values of micropores (S mi) and the volumes of the micropores (V mi) were calculated according to the V-t method (Allen, Reference Allen1997).
Differential scanning calorimetric, thermogravimetric and differential thermogravimetric (DSC-TG-DTG) analyses were performed using a SETSYS2400 apparatus (SETARAM) under the following conditions: temperature range 20–1150°C; static air atmosphere; heating rate 20°C min–1; and 15–20 mg sample mass.
The compressive strength was measured on cylindrical specimens with polished top and bottom surfaces with a diameter of 30 mm and a height of ~50 mm using a Cyber Plus Evolution press supplied by Mac Ben using a load rate of 0.5 kN s–1. The dimensions of each geopolymer specimen were measured with digital callipers on the 28th day. The average diameter of each cylindrical specimen was measured in six places: two mutually perpendicular at the bottom, middle and top of each cylinder. The shrinkage was calculated based on the average diameter compared to the initial diameter (30 mm). The mass of each specimen was measured using an analytical balance on the 28th day. The compressive strength was determined on the 28th day over the entire load application until fracture. All of the tested specimens were collected and the water content was determined by drying the samples to a constant mass in an oven at 105°C. The apparent density of each series was estimated by dividing the calculated dry mass by the measured volume of each specimen. The specific strength (also known as the strength-to-weight ratio) was calculated from the compressive strength divided by the apparent density.
Results and discussion
Physical properties
On the 28th day, the density, shrinkage and compressive strength of the hardened geopolymers were recorded (Table 2). The calcination of the natural zeolite to metazeolite greatly increased the geopolymer compressive strength from ~11 to 37 MPa. The geopolymers based on waste aluminate solutions showed slightly greater compressive strength, probably due to the presence of the AD-AL-24B admixtures used in the anodizing process.
Table 2. Physical properties of the alkali aluminate-activated clinoptilolite geopolymers.

There were no visible cracks on the samples caused by volume changes during geopolymerization. The recorded shrinkage was ~3%. For comparison, the shrinkage of similar zeolite-based geopolymer specimens activated by sodium silicate is more than fourfold greater, and some of these specimens crack due to such significant volume changes (Nikolov et al., Reference Nikolov, Rostovsky and Nugteren2017). Moreover, when using an aluminate activator, the Si/Al ratio of the system decreased. The Si/Al atomic ratio of the geopolymer gel determines the character of the structure: a low Si/Al ratio (up to 3) confers a 3D network, while an increase in the ratio confers a more linear or 2D framework (Davidovits, Reference Davidovits2011). When sodium aluminate was used as the activator, the shrinkage of the prepared geopolymers was greatly reduced.
The apparent density of the geopolymer samples was relatively low (Table 2) compared to Portland cement paste (1.78 g cm–3; Nikolov, Reference Nikolov2016). The geopolymer samples with natural zeolite contained large quantities of macropores and voids (Fig. 1). The large specific surface area (33 m2 g–1) of the natural zeolite caused air entraining. This effect was hindered after calcination of the natural zeolite; accordingly, the apparent density of the geopolymers increased to 1.50–1.53 g cm–3 for metazeolite-based geopolymers. The observed increase in the apparent density in the metazeolite-based geopolymers was due to the loss of the air-entraining properties of the precursor and the decrease of the water-to-solid ratio.

Fig. 1. Physical appearance and presence of macropores in a geopolymer specimen (Z0Al, diameter 30 mm). Left: canvas view; right: top view.
The relationship between compressive strength and density is expressed by specific strength. Generally, the greater the specific strength, the greater the strength and lighter the weight of the material (Zhang, Reference Zhang2011). Although the apparent density of the metazeolite-based geopolymers increased by ~50% compared to natural zeolite, the increase in compressive strength was greater (~240%). Thus, the specific strength of the prepared materials increased by more than twofold after the calcination of the precursor.
XRD analysis
The natural zeolite (Z000) is composed of clinoptilolite, opal-CT and amorphous matter (Fig. 2). The clinoptilolite content of the sample was ~80% (Lihareva et al., Reference Lihareva, Dimova, Petrov and Tzvetanova2010). The thermal treatment of the zeolite at 900°C led to total amorphization of the clinoptilolite structure, while opal-CT was not affected (Z900). The strong alkaline activator dissolved both opal-CT and clinoptilolite. Nevertheless, some clinoptilolite remained unreacted in sample Z0Al (Fig. 2). The XRD traces of both geopolymer series (Z0Al and Z9Al) showed a hump at 20–40°2θ typical of amorphous matter (Fig. 2). The curing conditions (80°C) promoted the crystallization of two new phases: phillipsite and zeolite Na-P. The XRD traces of the geopolymers based on waste aluminate were identical and are not shown in Fig. 2.

Fig. 2. XRD traces for geopolymer precursors: natural zeolite (Z000), metazeolite (Z900) and geopolymer samples (Z0Al, Z9Al). C = clinoptilolite; O = opal-CT; P = phillipsite; Z = zeolite NaP.
Nitrogen adsorption
The results regarding nitrogen adsorption are summarized in Table 3. The specific surface area of natural zeolite–clinoptilolite (Z000) was 33 m2 g–1 (Table 3), which is greater than that reported for a natural zeolite from Wyoming, USA (18 m2 g–1; Camacho et al., Reference Camacho, Deng and Parra2010) and a zeolitic volcanic tuff from Vrancea, Romania (16.8 m2 g–1; Humelnicu et al., Reference Humelnicu, Drochioiu, Sturza, Cecal and Popa2006), but slightly lower than that for a natural zeolite from Shenyang, China (38.5 m2 g–1; Lin et al., Reference Lin, Liu, Dong, Chen, Huo and Liu2013). The specific surface area of the zeolite used decreased significantly to 4 m2 g–1 (metazeolite, Z900) after calcination. The calcination temperature influences the surface area and microporous and mesoporous volumes, but the pore-size distribution remains unaffected (Menad et al., Reference Menad, Feddag and Rubenis2016). The average pore-size diameter (D av) was >4.5 nm, indicating that the pores in test materials are predominantly mesopores. In addition, the microporous volume values decreased after calcination, indicating deformation of the porous structure. This is probably due to a collapse of the clinoptilolite structure, causing loss of its porous structure and deformation (Menad et al., Reference Menad, Feddag and Rubenis2016)
Table 3. Texture characteristics of the precursor samples (Z000, Z900) and geopolymer samples (Z0Al, Z9Al).

Samples Z0Al and Z9Al exhibit H3-type hysteresis loops according to the International Union of Pure and Applied Chemistry (IUPAC) classification (Fig. 3). The desorption branches contain a steep region associated with a so-called tensile strength effect, generally observed within the relative pressure range of 0.40–0.45. This effect is common in materials with non-rigid aggregates of plate-like particles, giving rise to narrow slit pores (ALOthman, Reference ALOthman2012).

Fig. 3. Nitrogen adsorption–desorption isotherms of the geopolymer materials (Z0Al and Z9Al).
Thermal behaviour
The behaviour of the geopolymers at elevated temperature affects the thermal and fire-resistance properties of the geopolymers. The thermal behaviour of samples Z0Al and Z9Al is shown in Fig. 4. Because the samples contained abundant zeolite, dehydration is associated with the release of pore water (zeolite-type water) and dehydroxylation. Physisorption water is in the range of 1–2% released at the beginning of the first endothermic stages for both samples. Water molecules were gradually released. Sample Z0Al showed more complicated thermal behaviour in comparison to sample Z9Al. The water molecules were released in five stages in the case of sample Z0Al, while four stages were registered in the case of sample Z9Al. The total mass loss was 15.85% for sample Z0Al and 13.48% for sample Z9Al.

Fig. 4. DSC-TG-DTG curves of the geopolymer samples Z0Al and Z9Al.
Exothermic effects without mass loss related to crystalline phase transformations were observed for both samples starting at ~600°C. Powder XRD analysis was conducted on the samples after the DSC-TG measurements. The thermal treatment of samples Z0Al and Z9Al at 1150°C showed that clinoptilolite, phillipsite and zeolite NaP recrystallized to leucite (Fig. 5). In sample Z9Al, the phase transformation to leucite was gradual, characterized by a single broad exothermic peak. On the other hand, sample Z0Al showed two distinct exothermic peaks, marked as ‘Exo1' and ‘Exo2' in Fig. 4. The difference between the two samples was the presence of unreacted clinoptilolite (Fig. 2). The total collapse of the clinoptilolite structure in raw natural zeolite occurs at 900°C (Nikolov, Reference Nikolov2016). This temperature marks the onset of the exothermal effect ‘Exo2' in sample Z0Al (Fig. 4). The thermal destruction of the unreacted clinoptilolite in sample Z0Al provides an amorphous phase that recrystallizes to leucite starting at ~900°C.

Fig. 5. XRD traces of thermally treated geopolymer samples heated at 1150°C. L = leucite.
Scanning electron microscopy
The SEM images of natural zeolite (Z000), metazeolite (Z900) and geopolymer pastes (Z0Al, Z9Al) are presented in Fig. 6. The morphology of the metazeolite is characterized by a smoother surface than the original zeolite (Fig. 6a,b). This is associated with the significant decrease in the specific surface area from 33 m2 g–1 for natural zeolite to 4 m2 g–1 for metazeolite. The varying particle morphologies of the precursors affected the rheology of the fresh mixtures. At the same water-to-solid ratio, the metazeolite-based mixtures displayed greater workability.
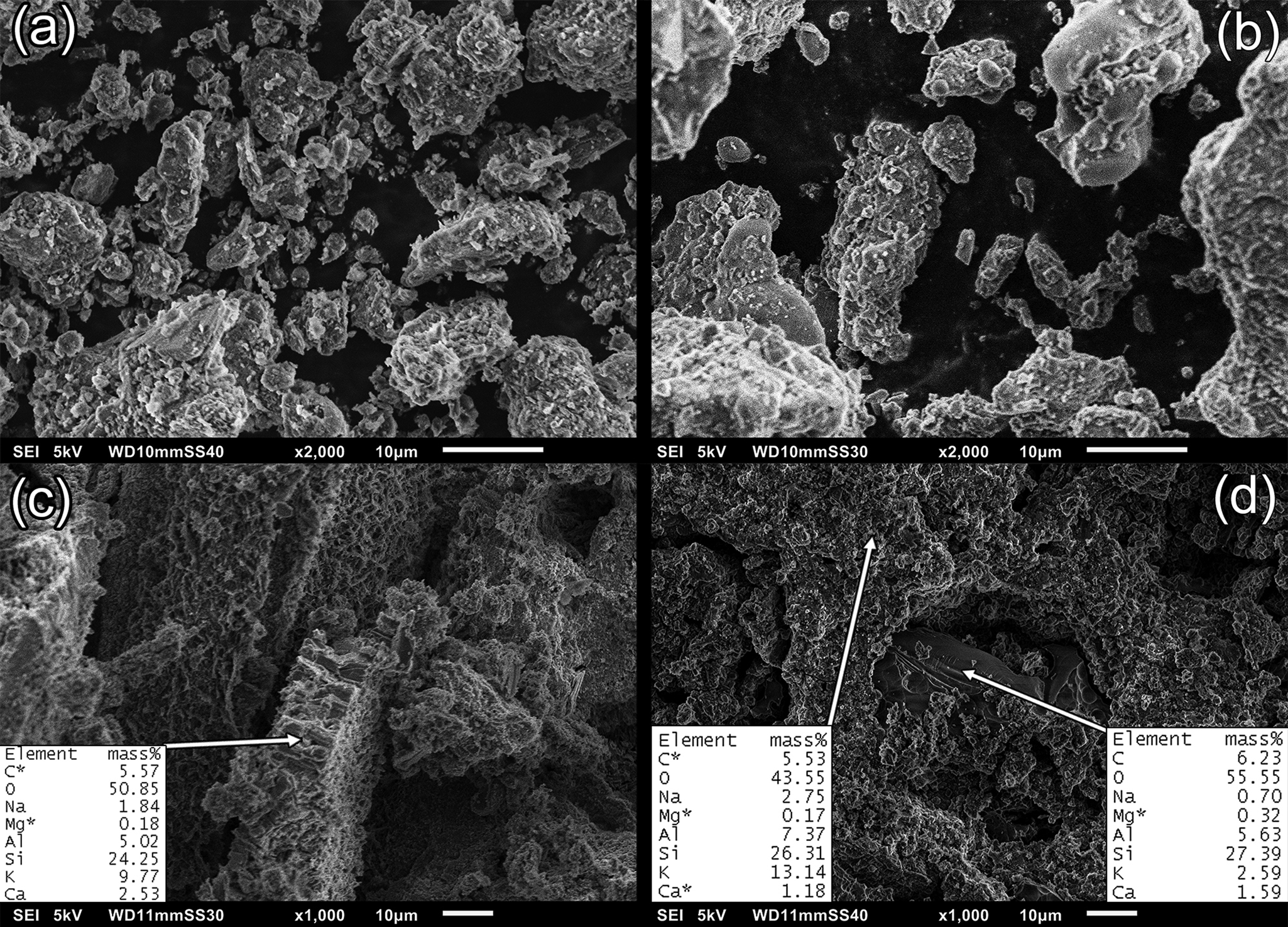
Fig. 6. SEM-EDS images of geopolymer precursors: (a) Z000 and (b) Z900; and geopolymer pastes: (c) Z0Al and (d) Z9Al.
The geopolymer samples showed a porous structure formed by unreacted particles and geopolymeric gel that was produced during the geopolymerization (Fig. 6c,d). Domains with varying surface morphologies were observed, characterized by reduced K and Na contents (Fig. 6d). These domains might belong to non-reacted metazeolite particles.
Conclusions
The synthesis of natural zeolite and metazeolite geopolymers using sodium aluminate as the activator led to the following conclusions:
• The calcination of the natural zeolite (clinoptilolite) greatly reduced the specific surface area from 33 to 4 m2 g–1. The surface of the metazeolite particles displayed a smoother morphology. Thus, the water demand of metazeolite is decreased, which favours the workability of the fresh geopolymer mixture.
• The calcination of clinoptilolite to metazeolite at 900°C greatly increased the geopolymer compressive strength from 11 to 37 MPa.
• The shrinkage of the clinoptilolite geopolymers based on sodium aluminate is relatively low, at ~3% (i.e. 4.5 times less than the silicate-activated clinoptilolite geopolymers). Thus, sodium aluminate is a suitable activator for Si-rich geopolymer precursors in materials with an insufficient aluminium content.
• There is no difference in the properties of the geopolymers using equal concentrations of analytical-grade sodium aluminate and waste solution from local industry. Hence, the utilization of corrosive industrial waste solutions has important economic and ecological benefits.
• The clinoptilolite-based geopolymer contains X-ray amorphous phases and newly formed phillipsite and zeolite NaP. The presence of zeolites in the final material might be beneficial in products with specific qualities and properties, such as ion exchange, passive cooling, antimicrobial activity, etc.
• Thermal treatment of the clinoptilolite geopolymers at 1150°C formed amorphous matter and allowed for crystallization of leucite.
Acknowledgements
The authors acknowledge Imerys Minerals Bulgaria AD and the international exchange programme Erasmus+ for their financial support.