Historical monuments are tangible witnesses to the evolution of civilizations over time. In Morocco, several cities are renowned for their historical sites, because the Amazigh, Arab and Andalusian cultures, which succeeded each other over time, blend perfectly to enrich the Moroccan heritage. Today, eight sites have been classified as ‘world heritage’ by UNESCO, with the main sites located in the imperial cities of Fez and Marrakech, which have been the kingdom's capital for nearly 900 years (Paccard, Reference Paccard1981).
Among the most fascinating historical sites, the El Badi Palace in Marrakech reflects the glory of the Saadian dynasty that governed Morocco from 1554 to 1659 (Touri, Reference Touri1999). The construction of this magnificent palace took 16 years (1578–1594). The general layout (Fig. 1) and decoration show the beauty and perfection of Moroccan architecture at that time. The mosaics and ceramics used to decorate the building constitute key elements of this exciting architecture. The palace was partially demolished at the time of the Ismaili dynasty a century after its construction, and a large proportion of the construction material was transferred to Meknes for reuse in the construction of the royal town of Moulay Ismail (Terrace, Reference Terrasse1949; Deverdum, Reference Deverdum1957). The remains of this building have now reached an advanced deterioration phase and its ceramic materials have been increasingly weakened due to human impacts over time. Restoration attempts following inspection of the historical monuments of Marrakech have not been successful because the new materials used in the restoration have deteriorated faster than the old ones. Traditional restoration methods that do not take into account the chemical and mineralogical characteristics of the raw materials are still practiced. Therefore, studies on the old building materials must be conducted as a first step before taking any conservation or restoration decisions (Barluenga et al., Reference Barluenga, Estirado, Raimundo, Conde, Agua, Villegas and García-Heras2013). In fact, with the exception of some recent studies that concern mainly Saadian tombs (Casas et al., Reference Casas, Briansó, Álvarez, Benzzi and Shaw2008; Bendaoud et al., Reference Bendaoud, Guilherme, Zegzouti, Elaatmani, Coroado, Carvalho and Queralt2013; Gradmann et al., Reference Gradmann, Bertlhold and Schussler2015) and the Saadian sugar factory of Chichaoua (Gamrani et al., Reference Gamrani, R'khaChaham, Ibnoussina, Fratini, Rovero, Tonietti, Mansori, Daoudi, Favotto and Youbi2012, Reference Gamrani2014), very few scientific studies have been undertaken to characterize the materials used in the construction and restoration of these Saadian monuments.

Fig. 1. Geographical location and plan of the El Badi Palace, Marrakech.
This study aimed to characterize the ‘zellige’ ceramics used in the construction of the El Badi Palace in order to understand the technical practices adopted by the Saadian dynasty in the sixteenth century. The physical and chemical properties and the texture of the ancient ceramics are mainly influenced by the composition of the raw material (Tschegg et al., Reference Tschegg, Ntaflos and Hein2009; De Vito et al., Reference De Vito, Medeghini, Mignardi, Orlandi, Nigro, Spagnoli, Lottici and Bersani2014), amounts of inclusions in the ceramic fabric and firing conditions (Riccardi et al., Reference Riccardi, Messiga and Duminuco1999; Rathossi & Pontikes, Reference Rathossi and Pontikes2010; İssi et al., Reference İssi, Kara and Oğuz Alp2011). The purpose of the present study was to determine how these parameters control the formation of these handmade materials and the choice of the raw material used in the manufacture of various Saadian ceramics. This study will permit selection of appropriate materials and the development of a specific approach to the restoration, maintenance and enhancement of El Badi Palace decorative ceramics.
MATERIALS AND METHODS
Materials
The mosaic ceramics, also referred to as ‘zellige’, constitute fundamental and characteristic elements of the Saadian monuments (Fig. 2). More than 20 different patterns have been identified in the walls of the El Badi Palace, the main pattern being composed of a basic element with an eight-pointed star called Kahtem (Benamara et al., Reference Benamara, Schvoerer, Haddad and Akerraz2003). This technique simultaneously appeared in different regions under the control of the Almohads (1130–1269) and the Merinides (1244–1465) in Fes (Morocco), the Zayanids (1236–1554) in Tlemcen (Algeria), the Nasrids (1232–1492) in Granada (Spain) and the Hafsides (1229–1574) in Tunis (Tunisia) (Erzini, Reference Erzini, Hedgecoe and Damluji1993; Hattstein & Delius, Reference Hattstein and Delius2000).

Fig. 2. Main Islamic forms of ‘zellige’. (1) El Badi Palace, Marrakech; (2) Royal Palace, Fes; (3) El Glaoui Kasbah, Fes; (4) Alhambra Palace, Granada; (5) names of the main forms of ‘zellige’ found in the El Badi Palace; and (6) Saadian Tombs, Marrakech.
The samples studied include nine decorative ceramics with different shapes and colours (Fig. 3). The samples were either taken directly from the wall using a micro-sampling procedure adopted by the General Inspectorate of Historic Monuments of Marrakech or were obtained directly from the palace reserve (Table 1).
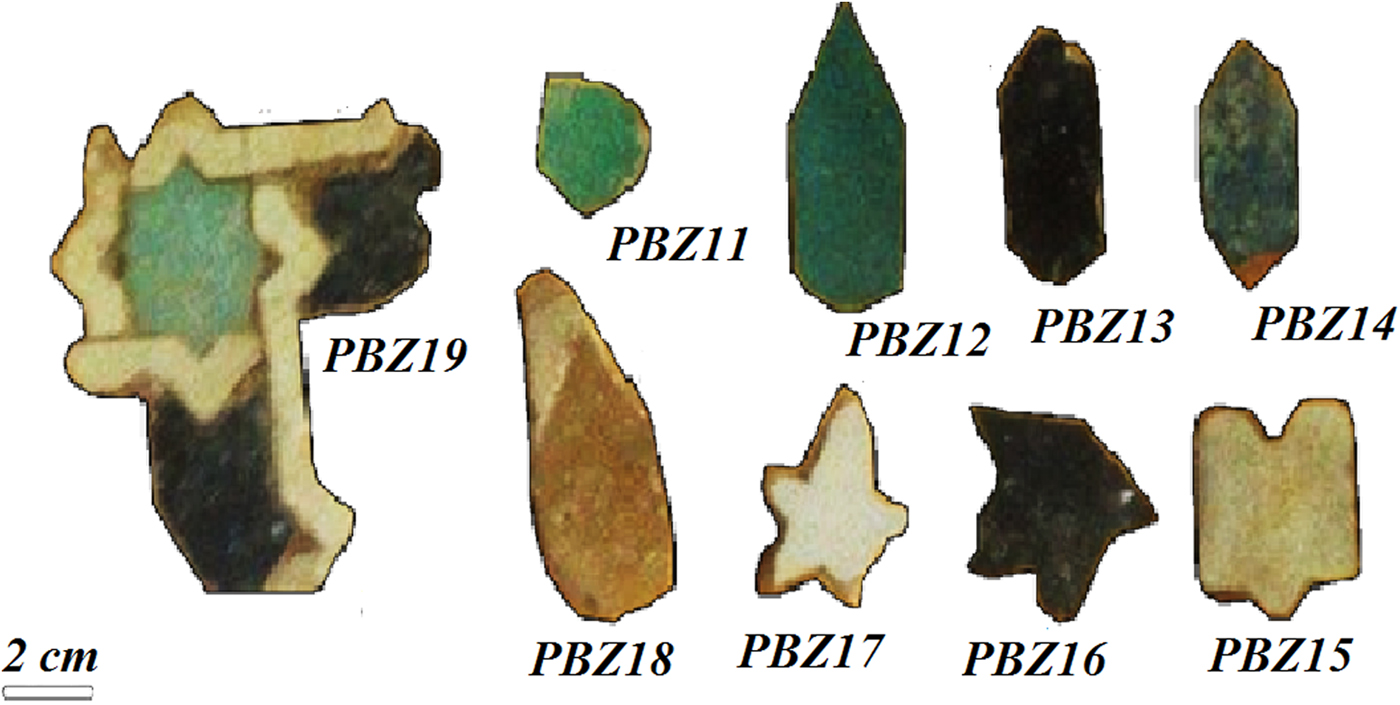
Fig. 3. The studied ceramic samples from the El Badi Palace.
Table 1. Characteristics of samples analysed from the palace reserve.

Methods
The textures of the samples and their surface characteristics were examined using a binocular loupe. More detailed observations of the textures were made successively by optical microscopy (CETI, Gx1500, Laboratory AGEs, University of Liege), scanning electron microscopy (SEM; XL-FEG-ESEM, University of Liege) and cathodoluminescence (Technosyn Cold cathodoluminescence 8200 Mk3, Laboratory of Sedimentology, University of Liege). For this last technique, samples were placed in a nuclide-type chamber under a vacuum of 0.20–0.01 Torr and bombarded with a beam of electrons accelerated by a voltage varying from 15 to 20 kV. The recording of the emissions from the sample was performed using a 3CCD high-definition camera (Sony DXC-930P).
Subsequently, the materials were carefully ground and homogenized and a portion was crushed in an agate mortar for X-ray diffraction (XRD) analysis. The mineralogical phases present in the terracotta were identified with an XRD powder diffractometer (Bruker Eco D8-Advance using Cu-Kα radiation) at the Laboratory AGEs, University of Liege, in the range 2–60°2θ. The XRD patterns were handled by the DIFFRACPlus.EVA software to remove the background noise and to calculate line positions and peak intensities.
The maximum firing temperature of the ceramics studied was determined by re-firing tests. Aliquots of each sample were ground in agate mortar and were annealed for 4 h in a furnace in the temperature range of 500–1000°C. The relative abundance of minerals was detected and estimated using TOPAS and DIFFRACPlus.EVA software.
Powdered samples were mixed with Spectromelt A12 flux in a sample:flux ratio of 1:9 and then analysed by X-ray fluorescence (XRF) using a PanalyticalAxios spectrometer equipped with an Rh tube for major element analysis (Laboratory of Petrology, University of Liege) using argon–methane gas. The data were treated with IQ+ software. The loss on ignition was determined by heating the samples at 1000°C for 2 h.
The elemental compositions of the glazes were determined by non-destructive XRF analysis applied directly on an area of 108 µm × 88 µm on the surface of each sample (Laboratory of Sedimentology, University of Liege). Quantitative analysis was performed using a hand-held XRF Analyser (X-MET8000, Oxford Instruments, Fremont, CA, USA) with metal standards, synthetic compounds and natural minerals. The elemental contents represent an average of three to five measurements.
RESULTS
Petrographic analysis of the ceramic body
Observation in natural light by optical microscopy allowed examination of pore shape and abundance at the edges and on the ceramic shards, as well as the percentage, grain size and distribution of inclusions (Fig. 4). The main features in terms of microstructure, groundmass and inclusions were described according to the criteria of Whitbread (Reference Whitbread1986, Reference Whitbread1995). The porosity of all samples varied from 10% to 15% of the total volume, which consists mainly of meso-vescicles and rare macro-vughs. The pore diameter varies from a few micrometres in the shard to 1 mm in the glaze, and their shape is angular to sub-rounded. The absence of a vitreous phase surrounding the grains indicates that no melting occurred during firing. The glaze–shard interface of the ‘zellige’ samples is poorly defined due to the penetration of the glaze mixture into the open pores of ceramics. The glaze was applied directly to the ceramic support without an intermediate layer. The thickness of the glaze is 250–350 µm. The groundmass is generally homogeneous and optically inactive with a beige to light brown colour. The inclusions are mainly represented by equidimensional grains of quartz, iron oxides and rare mica.
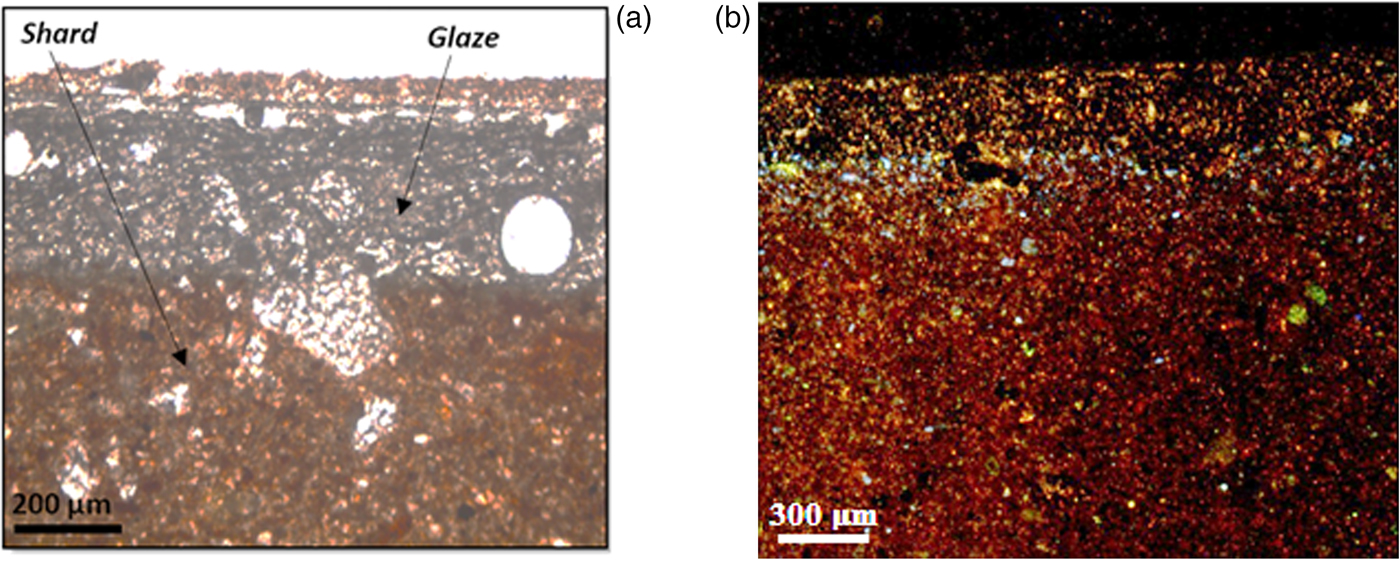
Fig. 4. Light microscopy (a) and cathodoluminescence (b) of the glaze–shard interface.
Cathodoluminescence can provide general information about the distribution and nature of the chemical elements in the glaze/shard boundary (Piponnier, Reference Piponnier1990) (Fig. 4). Under the effect of electronic bombardment, the white (PBZ15, PBZ17 and PBZ19) and yellow (BPZ18) glazes luminesce slightly in blue, indicating the presence of tin in the form of cassiterite (El Marraki, Reference El Marraki1998). Heavy minerals appear bright yellow in colour; they are clearly visible in the glaze, intruding deeply into the ceramic shard that is generally purple in colour because of the large number of quartz inclusions (Bechtel & Schvoerer, Reference Bechtel and Schvoerer1984). The orange colour reflects the abundance of calcite, whereas the associated green areas are indicative of plagioclase (Duttine, Reference Duttine2008; Müller et al., Reference Müller, Herrington, Armstrong, Reimar, Douglas, Nina and Kronz2010).
Mineralogical and chemical composition of the shards
The ‘zellige’ samples have similar mineralogical compositions (Fig. 5). The sherds are rich in quartz (26–34 wt.%), plagioclase and alkali feldspar (17–29 wt.%) and calcite (10–12 wt.%). The small amount of hematite (~3 wt.%) is responsible for the light colour (light brown) of the ceramic sherds. The XRD patterns also revealed the presence of enstatite (Mg2Si2O6), which may be attributed to the presence of MgO in the raw clay material (Hernandez et al., Reference Hernandez, Romero and Rincon2005). Ca silicates phases (i.e. gehlenite; Ca2Al [AlSiO7]) and diopside (CaMgSi2O6) are transitional phases formed at high temperature (≥700°C) (Maniatis et al., Reference Maniatis, Simopoulos, Kistikas and Perdikatsis1983; El-Ouahabi et al., Reference El Ouahabi, Daoudi, Hatert and Fagel2015). Gehlenite forms by grain boundary reaction between CaO, Al2O3 and SiO2 (Rathossi et al. Reference Rathossi and Pontikes2010; De Vito et al., Reference De Vito, Medeghini, Mignardi, Orlandi, Nigro, Spagnoli, Lottici and Bersani2014, Reference De Vito, Medeghinia, Mignardia, Coletti and Contino2016). It crystallizes preferentially in comparison with other anhydrous Ca–Al silicates (Goldsmith, Reference Goldsmith1953). The presence of Mg in the carbonate–quartz interface also favours the formation of diopside (Jordán et al., Reference Jordán, Sanfeliu and de la Fuente2001).

Fig. 5. (a) XRD traces showing the uniformity of mineral compositions of zellige samples. (b) Firing test of zellige sample (PBZ12). Qtz = quartz; Kfs = potassium feldspar; Pl = plagioclase; Cal = calcite; Di = diopside; Gh = gehlenite; Hem = haematite; Sd = siderite; En = enstatite; Ms = muscovite.
All nine ‘zellige’ samples studied are lime (CaO)–silica sherds (Table 2), with SiO2 contents of 38.9–57.7 wt.%, being less, on average, than the other materials studied. In addition, they contain 8.8–12.8 wt.% Al2O3, 4.7 wt.% Fe2O3 and 15 wt.% CaO, on average.
Table 2. Bulk chemical compositions (%) of the ceramic shard samples from the El Badi Palace.

LOI = loss on ignition.
The sherds studied display limited variation in terms of the total amorphous phase content (18–22%) (Table 3).
Table 3. Quantitative XRD analysis (%) of the El Badi Palace ceramics.

Elemental analysis of the glazes
Glaze plays decorative and protective roles for the shard surface, being responsible for its smooth and tight appearance. There is evidence for decreases in lead, copper, tin and iron oxide contents from the glaze exterior to the shard (Table 4). All glaze samples display enrichment of Pb and Sn in accord with previous reports that ancient ceramists often used lead oxide mixed with tin as an opacification agent (Hochuli-Gysel, Reference Hochuli-Gysel1977; Hatcher et al., Reference Hatcher, Kaczmarczyk, Scherer and Symonds1994; El Marraki, Reference El Marraki1998; Gliozzo et al., Reference Gliozzo, Lepri, Saguì and Memmi2015). The Pb and Sn oxides define two contrasting areas, as evidenced by SEM in backscattered electron mode. The dark area is rich in Pb (45.2 wt.%) with relatively less Sn (10.7 wt.%). The light area is richer in Sn (12.6 wt.%) and poorer in Pb (36 wt.%) (Fig. 6; Table 4).

Fig. 6. SEM images of the surface of the lead glaze (a, b) and the shard–glaze interface (c), with respective energy-dispersive X-ray analysis (EDS).
Table 4. Elemental composition of glazes expressed as oxide wt.%.

nd = not detected; <1 = element detected but at <1%.
The chemical composition of the various colours of glazes suggests the use of conventional dyes (Table 4). Hence:
– Copper (Cu2+) was used for the green glaze (2.95 wt.% of CuO);
– Iron (Fe3+) and manganese (Mn2+) were used for the black glaze (9.61 wt.% Fe2O3 and 2.99 wt.% MnO);
– Lead (Pb) and tin (Sn) associated with traces of iron (2.05 wt.%) and lime (4.15 wt.%) were responsible for the yellow–brown (honey) colour;
– Phosphorus (P2O5) was responsible for the blue glaze opalescence.
The greater lime contents observed in the P-rich glaze (8.4 wt.% of CaO) might be due to efflorescence of the shard surface made from calcareous clays (Walton et al., Reference Walton and Tite2010).
All glazes except for the yellow–brown ones were opacified with tin, with the glaze being rich in SnO2 (13.4 wt.%). A glaze becomes opaque with just 5 wt.% SnO2 (Rhodes, Reference Rhodes1978). The high proportion of SiO2 (39.4–50.4 wt.%) favours the formation of vitreous phases during firing.
The Fe2O3 gives the black, manganese-coloured glaze a brown hue. In the black samples, the MnO2 is present as idiomorphic Mn-rich crystals (Fig. 7). About 3.0 wt.% MnO2 is present in the upper part of the ceramic–glaze interface beside the major components SiO2 (39.5 wt.%), Fe2O3 (9.6 wt.%), PbO (38.2 wt.%) and CaO (2.16 wt.%).

Fig. 7. SEM-BSE image of a black glaze from the El Badi Palace. The long prismatic precipitates are Mn-rich crystals.
Yellow–brown and blue glazes have greater CaO contents (4.15 and 8.4 wt.%), whereas the K2O content does not exceed 2 wt.% in all glazes. The small amount of Cl found in the yellow–brown glaze (1.23 wt.%) may be attributed to the calcium chloride used as a flocculating agent in the glazes.
DISCUSSION
Mineral phases and firing conditions
Clayey raw materials undergo a complex set of thermal modifications during firing; thus, it is often difficult to predict the phase changes in fired ceramic clays (Jordán et al., Reference Jordán, Sanfeliu and de la Fuente2001; Pardo et al., Reference Pardo, Meseguer, Jordán, Sanfeliu and González2011). However, the disappearance of certain mineral phases and the neoformation of others may constitute a good indicator of the firing temperature (Cultrone, Reference Cultrone, Rodriguez-Navarro, Sebastian, Cazalla and De la Torre2001; Maritan et al., Reference Maritan, Nodari, Mazzoli, Milano and Russo2006; Trindade et al., Reference Trindade, Dias, Coroado and Rocha2009; Rathossi & Pontikes, Reference Rathossi and Pontikes2010). Decomposition of clay minerals begins at 300°C, and of carbonates from 700°C (Périnet, Reference Périnet and Courtois1983; Chen, Reference Chen, Lan and Tuan2000; Toledo, Reference Toledo, dos Santos, Faria, Carrió, Auler and Vargas2004). The decomposed elements produce new mineral phases, the nature and abundance of which depend on the chemical and mineralogical composition of the raw materials, the maximum heating temperature, the heating rate, the duration of firing and the kiln redox atmosphere (Brown & Bailey, Reference Brown and Bailey1963; Khalfaoui & Hajjaji, Reference Khalfaoui and Hajjaji2009; Pardo et al., Reference Pardo, Meseguer, Jordán, Sanfeliu and González2011).
The ‘zellige’ shards studied display similar chemical and mineralogical compositions (Fig. 8), reflecting the homogeneity of the raw clay material used for the El Badi Palace decoration. The absence of vitreous phases and the presence of Ca silicates confirm that calcareous clays were used as raw materials in the manufacture of ‘zellige’ (Riccardi et al., Reference Riccardi, Messiga and Duminuco1999; Cultrone et al., Reference Cultrone, Rodriguez-Navarro, Sebastian, Cazalla and De la Torre2001). The samples show a good linear correlation between CaO–Al2O3 (r2 = 0.878) and CaO–SiO2 (r2 = 0.921). Only the‘zellige’ sample PBZ14 plots separately in all binary diagrams. This sample is characterized by very high CaO contents and relatively small amounts of Fe2O3 and SiO2. The firing time and the placement of the articles in the traditional Saadian kilns were probably responsible for minor differences in the mineral constituents of each ‘zellige’.

Fig. 8. Binary diagrams of Al2O3–Fe2O3, Fe2O3–TiO2, CaO–Al2O3 and CaO–SiO2, showing compositional differences among the ‘zellige’ samples.
Upon firing, the disappearance of the total clay peak at 4.47 Å occurs at 550°C in the calcareous raw clay materials (Cultrone et al., Reference Cultrone, Eduardo, Kerstin, Maria José, Olga and Carlos2004). The absence of this peak in the XRD traces of the El Badi Palace ceramics (Fig. 5) attests that the firing temperature was >550°C. Otherwise, the zellige sherds have moderate calcite content. Decomposition of CaCO3 into CaO and CO2 occurs between 600 and 800°C, depending on the grain size, kiln atmosphere and duration of firing of the system (Riccardi et al., Reference Riccardi, Messiga and Duminuco1999; Cultrone et al., Reference Cultrone, Rodriguez-Navarro, Sebastian, Cazalla and De la Torre2001). Calcite resists longer in well-crystallized, coarse granules, at very fast heating rates, at short soaking times in the critical temperature interval and in conditions of a reducing atmosphere during firing (Maritan et al., Reference Maritan, Nodari, Mazzoli, Milano and Russo2006). SEM observations show that the primary calcite identified in the ‘zellige’ shards studied is well crystallized (Fig. 9), suggesting that the firing temperature was probably ~800°C.

Fig. 9. SEM images showing the presence of a calcite crystal in a ceramic shard (a) and neoformed melilite (gehlenite) crystals formed during firing (b) with accompanying EDS analyses.
On the other hand, the evolution of carbonates during firing in this type of calcareous raw material is responsible for the neoformation of gehlenite and diopside at ~700°C (Maggetti, Reference Maggetti and Olin1982; Périnet et al., Reference Périnet and Courtois1983; Echallier, Reference Echallier and Mery1989; Dondi et al., Reference Dondi, Ercolani, Fabbri and Marsigli1999). The formation of Ca silicates reduces the amount of free lime, and consequently the possibility for re-carbonation. The formation of Ca silicates also depends on the grain size and the crystalline form of the starting raw material (Maggetti et al., Reference Maggetti, Galetti, Schwander, Picon and Wessicken1981; Jordán et al., Reference Jordán, Boix, Sanfeliu and de la Fuente1999; Nagy et al., Reference Nagy, Kuzmann, Weiszburg, Gyökeres-Tóth and Riedel2000; Maritan et al., Reference Maritan, Nodari, Mazzoli, Milano and Russo2006; Nodari et al., Reference Nodari, Marcuz, Maritan, Mazzoli and Russo2007; Tschegg et al., Reference Tschegg, Ntaflos and Hein2009). Thermal reactions between the decomposed calcite and the relics of clay minerals to produce Ca silicates may be incomplete. New Ca silicates may be observed together with calcite in the case of excess calcite, large calcite grains and the well-crystallized form of calcite (Fabri et al., Reference Fabri, Gualtieri and Shoval2014). Accordingly, the coexistence of primary calcite and the Ca silicates in the ‘zellige’ samples studied indicates that the firing temperature was between 700 and 800°C.
The firing temperatures thus determined were checked by an ‘experimental firing test’. Firing below 600°C yielded a similar mineralogical composition. At 700°C, the calcite peaks (d = 3.04–3.01 Å) decreased in intensity and disappeared completely at 800°C, with an increase in gehlenite, diopside and hematite contents (Fig. 5b).
Glaze characterization
The visual appearance of the ‘zellige’ samples indicates that the glaze does not flow to the edges of the sherds, highlighting that the glaze mixture had been applied previously to the fired clay sherds as 15 cm × 15 cm tablets, and then a second firing was applied. Subsequently, the pieces were carved into smaller pieces like puzzles. This technique is still used by artisans in Fez (i.e. the main production centre of ‘zellige’ in Morocco since the fourteenth century) (Erzini, Reference Erzini, Hedgecoe and Damluji1993), with the difference being that the shelves currently used have dimensions of 10 cm × 10 cm. The ‘zellige’ pieces used in the construction of the El Badi Palace were therefore either imported from Fez or manufactured locally in Marrakech according to the current standards and procedures in Fez. The glaze technique used by the Saadians seems to be similar to that used currently in Fez; it consists of immersing the upper face of the ceramic articles directly in the glaze mixture and then letting them dry in air. The glaze is therefore applied to the ceramic sherd without slip or intermediate coating. The glazes are very rich in PbO (41.5–20.9 wt.% PbO) with a SiO2 content in the range 50.4–37.1 wt.%. The mixtures of PbO and SiO2 react to form the glaze that then interacts with the clay body. Although the amounts of SiO2 in the glazes are slightly smaller than those in the sherds, this feature suggests that siliceous sand was used as a source of silica in the glaze mixture. The PbO/SnO2 ratio of the glaze samples was very high, ranging from 3.1 to 41.3, indicating high viscosity of the glaze (high PbO) and a firing of temperature <700°C (Tite et al., Reference Tite, Pradell and Shortland2008; Gliozzo, Reference Gliozzo, Lepri, Saguì and Memmi2015).
CONCLUSION
The application of a multi-analytical approach to archaeological ceramics (zellige) of the El Badi Palace (Morocco) yielded three main conclusions:
– The similar mineralogical and chemical compositions of the studied ‘zellige’ samples from the El Badi Palace demonstrate that all of these ceramics were made from the same raw calcareous clay material.
– All of the ceramics were fired in traditional furnaces under similar temperatures and kiln oxidizing atmospheres. The maximum firing temperature ranged between 700 and 800°C.
– The lead-type glazes were applied directly to the ceramic pieces without any intermediate layers according to the technique that has been used for a long time in Fez. The ‘zellige’ pieces were therefore either transported from Fez or manufactured locally in Marrakech according to the standard procedures in Fez.
ACKNOWLEDGMENTS
Financial support was provided by a bilateral cooperation project Wallonie Bruxelles-Maroc (WBI 2015-2017 project 2.7) and by the PPR-CNRST (Centre National de Recherches Scientifiques et Techniques) program (grant PPR1/2015/63), which is gratefully acknowledged. The first author acknowledges EU financial support through a 12 month grant at the University of Liege through the Erasmus+ program for foreign PhD students. Mr Féréderic Boulevain from the University of Liege is thanked for comments that greatly improved the manuscript.