Aluminium is produced from bauxite via the Bayer process (Hosseini et al., Reference Hosseini, Niaei and Salari2011). Non-bauxite sources of aluminium production include kaolin, alunite, sillimanite, kyanite, fly ash and micas (Altıokka & Hoşgün, Reference Altıokka and Hoşgün2003; Hosseini et al., Reference Hosseini, Niaei and Salari2011). Kaolinite, with a relatively small particle size and large specific surface area, belongs to the group of hydrated aluminium silicates (Cuadros, Reference Cuadros2017). Kaolinite (ideally Al2Si2O5(OH)4) is a 1:1-type phyllosilicate mineral that consists of one silicate tetrahedral sheet and one aluminium hydroxide octahedral sheet in each layer. Kaolinite has properties that are valued in the porcelain, cement, brick, paper and rubber industries, such as brightness, whiteness, a fine grain size and chemical stability. Rocks rich in kaolinite are known as kaolin or china clay (Aghaie et al., Reference Aghaie, Pazouki, Hosseini, Ranjbar and Ghavipanjeh2009; Pohl, Reference Pohl2011; Phipps, Reference Phipps2014; Zhao et al., Reference Zhao, Gao, Tao, Guo and He2018). Kaolin is composed of 35–38% Al2O3 and 42–45% SiO2 and may be mined for the production of alumina (Al2O3) and aluminium (Tang et al., Reference Tang, Su, Li and Wei2010; Hosseini et al., Reference Hosseini, Niaei and Salari2011).
The endothermic dehydroxylation of kaolinite begins at 550–600°C, producing disordered metakaolin, but continuous hydroxyl loss is observed up to 900°C. Although, historically, there has been much disagreement concerning the nature of the metakaolin phase, extensive research has led to a general consensus that metakaolin is not a simple mixture of amorphous silica (SiO2) and alumina, but rather it has a complex amorphous structure that retains some longer-range order (but not strictly crystalline) due to stacking of its layers. The reaction is presented as follows (Bellotto et al., Reference Bellotto, Gualtieri, Artioli and Clark1995):

Thermal treatment such as calcination at 750°C increases the dissolution rate of Al and impurities such as Fe (Groudev & Groudeva, Reference Groudev and Groudeva1986; Altıokka & Hoşgün, Reference Altıokka and Hoşgün2003). Kaolin dissolution occurs under both acidic and alkaline conditions. Bauer & Berger (Reference Bauer and Berger1998) studied kaolinite dissolution using batch experiments in 0.1–4.0 M KOH solutions at 25°C and 80°C. Kaolinite dissolution was characterized by a linear release of SiO2 and Al as a log function of time. This relationship may be explained by a reaction affinity effect that is controlled by octahedral-sheet dissolution. Aldabsheh et al. (Reference Aldabsheh, Khoury, Wastiels and Rahier2015) and Wang et al. (Reference Wang, Feng and Liu2016) showed that silicon extraction from kaolinite was mainly affected by alkali-leaching temperature, alkali concentration and alkali-leaching time, and increasing these parameters enhanced dissolution. In a previous study involving an exhaustive analysis of the solubility of several aluminosilicate minerals in alkaline media, Si and Al dissolved congruently (Cama & Ganor, Reference Cama and Ganor2015). The extent of dissolution was somewhat higher in NaOH than in KOH solution (Aldabsheh et al., Reference Aldabsheh, Khoury, Wastiels and Rahier2015).
Hulbert & Huff (Reference Hulbert and Huff1970) examined the acid leaching of calcined kaolin with 5.9 and 8.6 N solutions of hydrochloric, nitric and sulfuric acids. Kaolin was calcined at 732°C for 2 h and the leaching tests were carried out at 60°C, 80°C and 95°C. The dissolution could be expressed as $ln\displaystyle{1 \over {1-x}} = {\rm k}t^m$, where the parameter m varies between 1.10 and 1.55 and is process specific, x is the fraction reacted and t is the contact time. The activation energy was 121.4 kJ/mol and the dissolution of aluminium with HCl was the fastest, whereas HNO3 had the lowest dissolution rate. Altıokka & Hoşgün (Reference Altıokka and Hoşgün2003) and Lima & Angélica (Reference Lima, Angélica and Neves2014) investigated the kinetics of kaolin dissolution in HCl and H2SO4, respectively. The activation energy was 79 kJ/mol for Al dissolution in HCl and 97 kJ/mol in H2SO4.
Organic acids may also be used to dissolve Al-silicates. Cama & Ganor (Reference Cama and Ganor2006) showed that the dissolution of Al-silicates in oxalic acid and other carboxylic acids is much faster than inorganic acids under comparable pH conditions. Organic acids act as metal-chelating agents and thereby increase the solubility of minerals. Thus, the adsorption of organic acids and anions on the surfaces of clay minerals may accelerate and facilitate metal dissolution, leading to mineral weathering and degradation (Ganor & Lasaga, Reference Ganor and Lasaga1994; Cama & Ganor, Reference Cama and Ganor2006). Protonation caused by organic acids reduces the pH and may shift the equilibrium towards dissolution. The overall dissolution reaction of kaolinite under acidic conditions may be expressed as (Cama & Ganor, Reference Cama and Ganor2006):

The dissolution rate depends on the specific organic acid. Zinder et al. (Reference Zinder, Furrer and Stumm1986) showed that the dissolution rate constants followed the following orders: koxalate > kmalonate > ksuccinate for dicarboxylic anions and ksalicylate > kphthalate > kbenzonate for aromatic ligands. Wang et al. (Reference Wang, Li, Hu, Zhang and Zhou2005) showed that the dissolution of Si and Al from kaolinite increased with increasing concentration of citric, oxalic and malic acid and was most effective with oxalic acid.
The purpose of this study was to investigate the dissolution of aluminium from metakaolin using citric, oxalic and lactic acids in single and binary (citric–oxalic and lactic–oxalic) mixtures. The pulp density, acid concentration, pH, agitation speed, temperature and contact time were evaluated as process parameters and the kinetics of aluminium dissolution in binary organic acids systems and their respective activation energies were determined.
Materials and methods
Characterization and chemical composition
A representative kaolin sample from a concentrate was obtained from the Zonoz processing plant, located in East Azerbaijan Province, Iran. The particle-size distribution of the kaolin sample was determined by a laser particle sizer (Analysette 22, Fritsch Nano-Tec, Idar-Oberstein, Germany) and it was comparable with results for the calcined and leached samples (Fig. 1). The kaolin sample had a median particle size (d 50) of 3.3 µm, d 80 of 7 µm and d 25 of 1.7 µm. Calcination and leaching did not change significantly the particle size, with the d 50 of the calcined and leached samples being 5.9 and 4.7 µm, respectively.

Fig. 1. Particle-size distribution of untreated kaolin (not calcined), calcined and leached samples. d 50 = average particle size.
The kaolin sample was heated at 750°C for 2 h to convert it to metakaolin before the dissolution experiments (Groudev & Groudeva, Reference Groudev and Groudeva1986; Altıokka & Hoşgün, Reference Altıokka and Hoşgün2003). The chemical analysis of the original material and the metakaolin, determined by X-ray fluorescence (XRF) spectroscopy (MagiX-PRO XRF spectrometer, PANalytical), is provided in Table 1. The original kaolin contained 63% SiO2 and 24% Al2O3, while the metakaolin contained 68.8% SiO2 and 25.6% Al2O3. The weight loss (loss on ignition) of the calcined sample was significantly reduced, but other oxides except MgO were slightly increased. Because the exact aluminium content was important and the chemical elemental analysis methods are more precise, an alkaline fusion method in addition to XRF was used to analyse the aluminium content. The chemical analysis of the metakaolin sample by the alkaline fusion method yielded an aluminium content of 12.5%, and this value was used in subsequent calculations.
Table 1. XRF analysis results before and after heating (calcination). The results are expressed as wt.%.

LOI = loss on ignition.
Semi-quantitative X-ray diffraction (XRD) was used to identify the mineralogical composition of the sample. The XRD traces were obtained using a Siemens D-8 Advance diffractometer with Ni-filtered Cu-Kα radiation, a goniometer speed of 1°2θ/min and a scan step of 0.01°2θ from 10 to 70°2θ. Quartz (SiO2), kaolinite (Al2Si2O5(OH)4), goethite (FeO(OH)) and calcite (CaCO3) were the major phases of the original untreated sample. After calcination at 750°C for 2 h, the kaolinite peaks disappeared in the metakaolin sample. Figure 2 presents the result of the XRD analysis of the kaolin and metakaolin samples.

Fig. 2. XRD traces of (a) untreated kaolin and (b) metakaolin.
The morphology and elemental composition of gold-coated samples were examined with a scanning electron microscope (SEM; Philips XL30) equipped with an energy-dispersive spectrometer (EDAX).
Leaching tests and kinetic studies
The chemical leaching tests were performed by adding 20 g of the metakaolin sample to 100 mL of acid solution, which contained 50 g citric, oxalic or lactic acid/L (or their binary mixtures) in 250 mL conical flasks. The initial pH of 0.5 was adjusted with sulfuric acid (96–98% H2SO4). The reaction temperature, stirring speed and reaction time were 50°C, 150 rpm and 6 h, respectively. The leaching solution was removed by filtration and the solids were washed with 50 mL of deionized water before elemental analysis.
Initially, aluminium dissolution from metakaolin was tested with citric, oxalic and lactic acid and their binary (citric–oxalic acid and lactic–oxalic acid) mixtures. The pulp density for further experiments was selected based on the greatest extent of aluminium dissolution. The initial pH values and acid concentrations were also tested for aluminium dissolution, followed by the agitation speed and the reaction temperature. These series of tests were carried out in 500 mL Erlenmeyer flasks with 200 mL of leach solution on a magnetic heater stirrer. Sample aliquots (2 mL) were taken at intervals for analysis of dissolved Al. All chemicals were of analytical grade, and deionized water was used to prepare the test solutions. The experiments were repeated twice and the average results are reported. Loss of volume due to evaporation was compensated for by adding deionized water. Deionized water was first heated up to the reaction temperature and then, after adjusting the pH, was added to the reaction vessel. Sample volumes were replaced with fresh leaching solution and this dilution was taken into account in the results.
In total, eight parameters (type and concentration of organic acid and binary ratios, pulp density, pH, agitation speed, temperature and contact time) were evaluated using the ‘one factor at the time’ methodology.
Results and discussion
Effect of acid type and their binary combinations
The results of the chemical leaching tests to determine the effects of the acid type (citric, oxalic and lactic acid) and their binary ratios on aluminium recovery are listed in Table 2. The aluminium dissolution rates with respect to various ligands were in the following order: oxalic acid > citric acid > lactic acid. Oxalic acid had the highest level of aluminium dissolution among the acids, in accordance with previous studies (Zinder et al., Reference Zinder, Furrer and Stumm1986; Chin & Mills, Reference Chin and Mills1991). The binary 1:4 ratios of citric–oxalic and lactic–oxalic acids yielded the greatest extent of aluminium dissolution, reaching 2.43 g and 2.50 g Al/L and leaching yields of 14.5% and 14.9%, respectively. These binary 1:4 ratios of citric–oxalic and lactic–oxalic acids were used in the remainder of the leaching tests.
Table 2. The effects of acid type and their mixtures on the dissolution of aluminium from metakaolin (50°C, 6 h, 150 rpm, total acid concentration 50 g/L, pulp density 20%, pH 0.5). Standard deviations are also indicated for the percentage dissolution.

Effect of pulp density
Pulp densities were tested at 5%, 10%, 15% and 20% concentrations. The results are shown in Fig. 3. The dissolution of aluminium increased slightly with pulp density. The greatest Al-leaching yields were 14.9% and 14.5% obtained with lactic–oxalic and citric–oxalic acid mixtures and 20% pulp density (Fig. 3).

Fig. 3. The effect of pulp density on the dissolution of aluminium from metakaolin (50°C, 6 h, 150 rpm, total acid concentration 50 g/L). (a) Lactic–oxalic acid mixture and (b) citric–oxalic acid mixture at 1:4 ratios, pH 0.5.
Effect of pH
The effect of pH over the range 0.5–3.5 was tested in suspensions with 20% pulp density. Sulfuric acid and Na-hydroxide were used for pH adjustments. The results are shown in Fig. 4. Aluminium dissolution decreased with increasing pH. The greatest Al-leaching yields of 14.9% with the lactic–oxalic acid mixture and 14.5% with the citric–oxalic acid mixture were obtained at pH 0.5 (Fig. 4).

Fig. 4. The effect of pH on the dissolution of aluminium from metakaolin (50°C, 6 h, 150 rpm, concentration of acid 50 g/L). (a) Lactic–oxalic acid mixture and (b) citric–oxalic acid mixture at 1:4 ratios and 20% pulp density.
Effect of organic acid concentration
The effect of organic acid on Al dissolution was tested at concentrations of 25, 50, 75 and 100 g/L. The results are presented in Fig. 5. Aluminium dissolution increased with acid concentration. In the presence of organic ligands, the rates of Al dissolution were markedly increased, and this increase was directly related to ligand concentration (Chin & Mills, Reference Chin and Mills1991; Cama & Ganor, Reference Cama and Ganor2006). The greatest extent of Al dissolutions of 2.73 g/L with the lactic–oxalic acid mixture and 2.83 g/L with the citric–oxalic acid mixture were obtained with an acid concentration of 100 g/L, corresponding to the respective Al-leaching yields of 16.3% and 16.9% (Fig. 5).
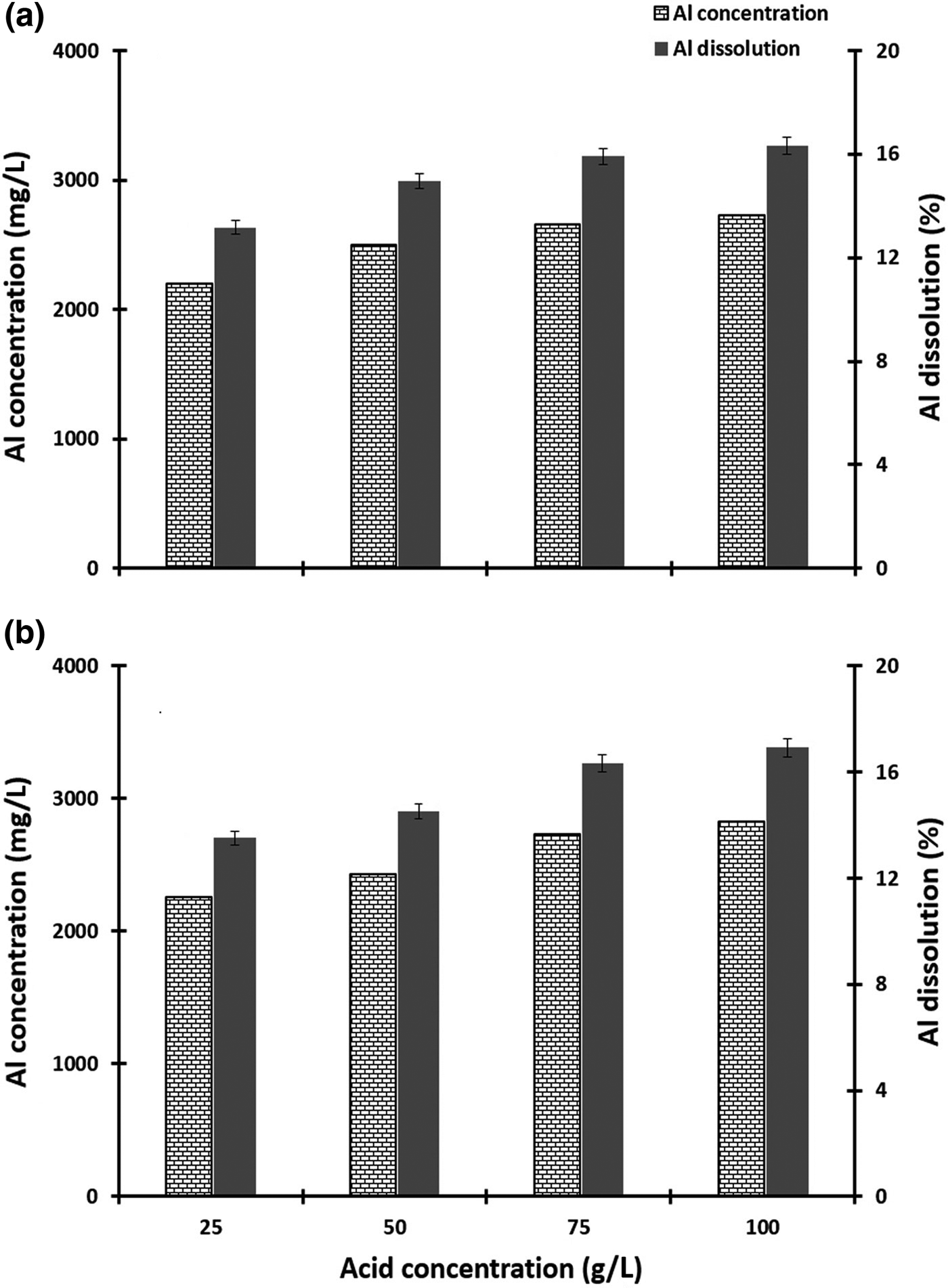
Fig. 5. The effect of acid concentration on the dissolution of aluminium from metakaolin (50°C, 6 h, 150 rpm, pH 0.5). (a) Lactic–oxalic acid mixture and (b) citric–oxalic acid mixture at 1:4 ratios.
Effect of stirring speed
The effect of stirring speed on Al dissolution from metakaolin was tested at 150, 250, 450 and 600 rpm. The results are presented in Table 3. The dissolution rate increased with the agitation speed, probably due to the decrease in the thickness of the metakaolin film layer or the formation of fine particles as a result of disaggregation or abrasion of metakaolin. These fine particles have a large ratio of reactive surface area to specific surface area and therefore the dissolution rate increased with stirring (Metz & Ganor, Reference Metz and Ganor2001; Ajemba & Onukwuli, Reference Ajemba and Onukwuli2012). Aluminium dissolution decreased across the stirring speed range of 250–600 rpm. High agitation speed may cause turbulence, forcing the fluid to rotate like a cyclone and thereby reducing the contact or residence time of the elements. Maximum Al dissolution was obtained at 250 rpm.
Table 3. The effect of stirring speed on aluminium dissolution from metakaolin (50°C, 6 h, pH 0.5, pulp density 20%, lactic–oxalic acid and citric–oxalic acid mixture at 1:4 ratio, total acid concentration 100 g/L). Standard deviations are also indicated for the percentage dissolution.

Effects of temperature and contact time
The effect of temperature was tested at 50, 60, 70 and 80°C. To reduce evaporation, experiments were carried out with 200 mL of solution and the pulp density (20%) was kept constant. Sulfuric acid was used to adjust the pH to 0.5. The results are presented in Fig. 6. After 11 h of contact time with the citric–oxalic acid mixture, the greatest Al-leaching yields increased from 34.3% at 50°C to 76.6% at 80°C. The Al-leaching yields with the lactic–oxalic acid mixture increased from 54.3% at 50°C to 78.3% at 80°C. Kaolinite dissolution is mainly affected by the alkali-leaching temperature, alkali concentration and alkali-leaching time (Aldabsheh et al., Reference Aldabsheh, Khoury, Wastiels and Rahier2015; Wang et al., Reference Wang, Feng and Liu2016). These parameters are also effective in acid leaching. The dissolution of Al increased with these parameters in the acid leaching of metakaolin.

Fig. 6. The time course of aluminium dissolution in the temperature range of 50–80°C. (a) Lactic–oxalic acid 1:4 mixture and (b) citric–oxalic acid 1:4 mixture.
In general, in the series of initial and optimization tests (except for those at 50°C and 50 g/L acid concentration), the initial pH of the solutions was ~0.7 on average. The amount of additional sulfuric acid for pH adjustment was very small and had no discernible effect on the dissolution rate of aluminium. After investigating the effect of acid concentration on the dissolution of aluminium and selecting a concentration of 100 g/L, the initial pH of the solution was ~0.5 and the amount of additional sulfuric acid used to adjust the pH during the leaching tests was negligible. In the final set of tests on the temperature effect, the pH increased and therefore sulfuric acid was titrated in order to adjust the pH during the contact time. Aliquots of 3, 6 and 7 mL of sulfuric acid were used to adjust the pH at 60, 70 and 80°C, respectively. Due to the considerable amount of additional sulfuric acid used in tests with a temperature of 80°C, this temperature was selected for two additional experiments in order to evaluate the effect of additional sulfuric acid on aluminium dissolution (Fig. 6). One test was performed with organic acids without the pH adjustment and the second was carried out with pH adjustment with sulfuric acid. The effect of additional sulfuric acid was lower at the other temperatures.
The concentration of sulfuric acid was the same as that used for pH adjustment. The combination of organic acids and sulfuric acid yielded maximum Al recovery. Organic acids without pH adjustment (i.e. no sulfuric acid) achieved the greatest extent of dissolution in the first 3 h, but the greatest overall aluminium dissolution was obtained with organic acids and pH adjustment with sulfuric acid to pH 0.5.
Kinetic study
Previous kinetic studies have mostly tested inorganic acids such as sulfuric acid and hydrochloric acids, but not organic acids. There is little to no general agreement on the dissolution mechanism and reaction kinetics for describing the dissolution of Al from metakaolin. Altıokka & Hoşgün (Reference Altıokka and Hoşgün2003) and Lima et al. (Reference Lima, Angélica and Neves2014, Reference Lima, Angélica and Neves2017) studied the application of the shrinking core model to spherical particles with a constant size. The dissolution was a chemically controlled process. However, Olsen et al. (Reference Olsen1983) reported that the leaching of metakaolin in boiling HCl solution was a zero-order reaction with diffusion control. The results of the present study indicate that the dissolution was under chemical-reaction control because of the high values of the activation energy and the response of the reaction to temperature. A comparison of the activation energy obtained from the dissolution by organic acids with previous studies shows that the activation energy of organic acids was less than that with inorganic acids.
The reaction model is dependent on the particle size, which does not change upon leaching and calcination. The shrinking core model was applied in order to describe the leaching of spherical and flat particles with constant size (Gharabaghi et al., Reference Gharabaghi, Noaparast and Irannajad2009; Lima & Angélica, Reference Lima, Angélica and Neves2014). According to this model, the rate of the leaching is controlled by diffusion or a chemical reaction. Simplified equations of the shrinking core model for spherical particles with constant size are expressed as follows (Levenspiel, Reference Levenspiel1972; Souza et al., Reference Souza, Pina, Lima, da Silva and Leão2007; Lima & Angélica, Reference Lima, Angélica and Neves2014).


where x is the reacted fraction, k is the rate constant and t is the reaction time; Eq. (3) is the chemical control model and Eq. (4) is the diffusion control model.
Application of the kinetic models of surface chemical reaction and diffusion control is shown in Fig. 7 for specific ranges of particle size and acid concentration at 20% pulp density. The rate constants (k) and coefficients of determination (R 2) for the various temperatures are given in Table 4.

Fig. 7. Kinetic modelling of (chemical control and diffusion control) aluminium leaching from metakaolin at temperatures of 50–80°C. (a,b) Lactic–oxalic acid mixtures and (c,d) citric–oxalic acid mixtures at 1:4 ratios.
Table 4. The rate constants (k) and coefficients of determination for aluminium dissolution at various temperatures. The data were calculated from Fig. 7.

In the Arrhenius equation, k = k0exp(–E a/RT), a plot of ln k versus 1/T is a straight line with a slope of –E a/RT and an intercept of ln k0. Activation energy (E a) values were calculated using the chemical and diffusion-control models (Fig. 8). The data fit better in the diffusion control model. Thus, the dissolution rate of aluminium from metakaolin is subject to diffusion control with activation energy values E a(lactic–oxalic) = 74.6 kJ/mol and E a(citric–oxalic) = 57.8 kJ/mol.

Fig. 8. Arrhenius plots of aluminium dissolution from metakaolin at 50–80°C (323–353 K). Lactic–oxalic acid (1:4) mixtures: (a) chemical reaction control model; (b) diffusion control model. Citric–oxalic acid (1:4) mixtures: (c) chemical reaction control model; (d) diffusion control model.
Although the diffusion model provided a better fit, the E a values are high for diffusion control and are within the range of chemical control reactions. In general, the activation energy for diffusion control is <20 kJ/mol and is >40 kJ/mol for chemical reaction control (Habashi, Reference Habashi1999; Safarzadeh et al., Reference Safarzadeh, Moradkhani and Ojaghi-Ilkhchi2009; Uçar, Reference Uçar2009). The diffusion-control process depends only slightly on temperature, whereas the chemical control process is highly dependent on temperature. The activation energy values for the chemical control model (Fig. 8) are E a(lactic–oxalic) = 41.0 kJ/mol and E a(citric–oxalic) = 32.9 kJ/mol. These activation energy values suggest that both diffusion control and chemical control were effective at the leaching of aluminium from metakaolin.
SEM and EDAX analysis
The results of SEM and the corresponding EDAX mapping of Si and Al of untreated kaolin and residual solids from the leaching of metakaolin by organic acids in binary systems are presented in Fig. 9. Some particles were flat and some were rounded and spherical. The surfaces of the particles in the original sample were nearly smooth and even. After contact with organic acids, the particles showed a more robust, even eroded surface. The amount of Al in the solids after the leaching process was clearly reduced. In contrast, the elemental maps of Si before and after the leaching treatment were comparable.

Fig. 9. SEM images and the corresponding EDAX mapping of Si and Al of (a) untreated metakaolin and residual solids from the leaching of the metakaolin sample with (b) the citric–oxalic acid (1:4) mixture and (c) the lactic–oxalic acid (1:4) mixture.
Conclusion
Oxalic acid dissolved more Al from metakaolin than citric and lactic acids. The dissolution increased with the binary combination of oxalic acid with two other acids at w/w ratios of 1:4 (lactic or citric acid to oxalic acid). Aluminium dissolution was pH and temperature dependent. Pulp density of up to 20% did not increase Al dissolution significantly. The dissolution increased with agitation speed up to 250 rpm and then decreased. The optimal combination of the experimental parameters was: total acid concentration = 100 g/L, pulp density = 20%, pH = 0.5, stirring speed = 250 rpm and temperature = 80°C. Under these conditions, Al dissolution reached 78% and 77% with the lactic–oxalic and citric–oxalic acid mixtures, respectively. In the corresponding control test using only sulfuric acid, aluminium dissolution was 44%. The activation energy values and the temperature dependency indicated that the dissolution was under chemical reaction control, although diffusion also seemed to contribute to the overall kinetic control.
Author ORCIDs
Hadi Abdollahi, 0000-0002-9099-7451.
Acknowledgements
The authors acknowledge with thanks the University of Tehran for financial support. The authors are also thankful to Mr Ali Rezaei for technical assistance.